Inteligentne systemy transportu, które niezależnie sterują poszczególnymi przenośnikami, otwierają drogę do masowej produkcji partii jednosztukowych. Jedynym sposobem, aby takie rozwiązanie naprawdę działało, jest istotne ograniczenie wymaganego ręcznego programowania ruchu przenośników, przy użyciu oprogramowania systemowego, jak np. mapp Trak firmy B&R.
Wyroby niepowtarzalne nie tylko przyciągają uwagę, rozbudzają także w konsumentach głęboką chęć ich posiadania. Coraz większa liczba producentów dąży do zapewnienia sobie udziału w zyskach wynikających z masowej standaryzacji poprzez wyposażanie fabryk w inteligentne systemy transportu w oparciu o wyznaczone ścieżki. Jednak masowa standaryzacja opłaca się tylko wtedy, gdy system ścieżek jest na tyle elastyczny, aby dostosować go do różnych wariantów wyrobów lub do całkowicie nowych wyrobów szybko i niedrogo.
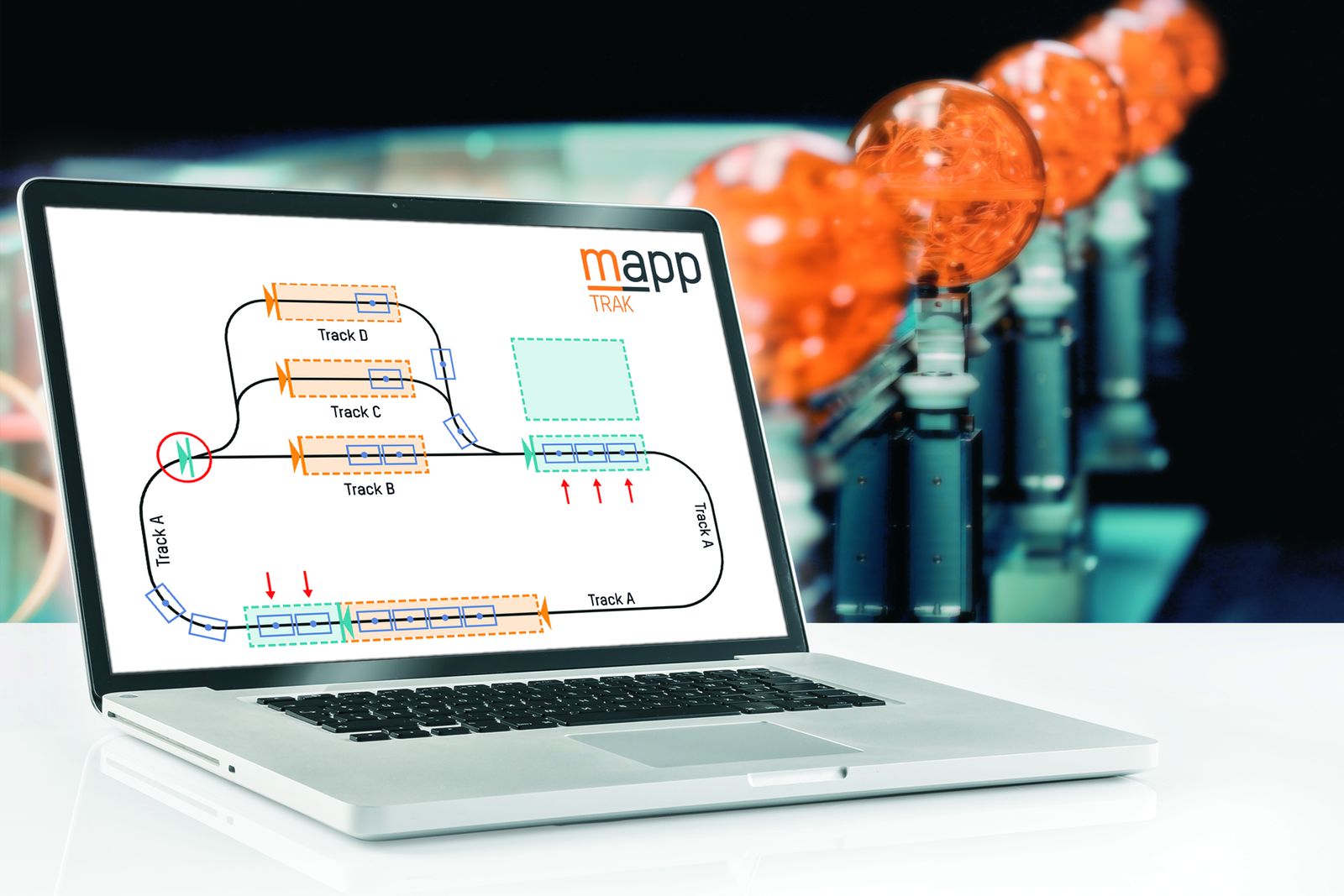
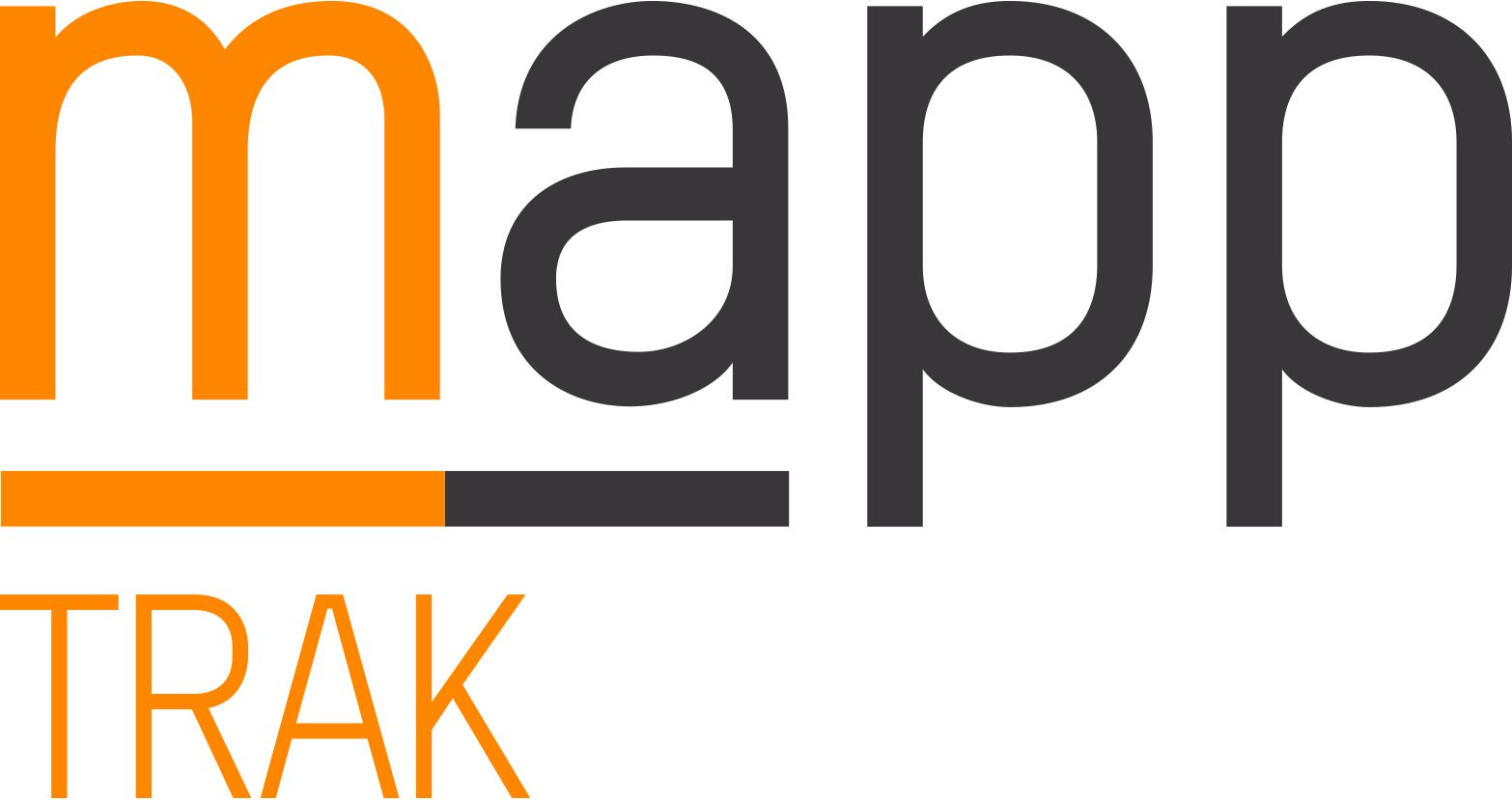
Inteligenty system transportu ACOPOStrak firmy B&R spełnia wszystkie te wymogi. System posiada strukturę modułową – cztery podstawowe elementy ścieżek i elementy przekierowujące pozwalają na połączenie ich praktycznie w dowolny układ oraz na łatwe dostosowanie i rozszerzenie w każdym momencie. Elektromagnetycznie napędzanymi wózkami można sterować niezależnie nawet wtedy, gdy znajdują się one po różnych stronach elementu przekierowującego.
Wysoce skalowalna architektura systemu pozwala na tworzenie układów o długościach ścieżek przekraczających 100 metrów, po których poruszają się setki wózków. Ponadto: „Pomimo złożoności systemu jest on bardzo łatwy w obsłudze”, wyjaśnia menedżer ds. technologii mechatronicznych w B&R, Robert Kickinger. B&R uprościła proces projektowania rozwiązań ACOPOStrak, aby wspomóc budowniczych maszyn i firmy produkcyjne w szybkim wprowadzaniu wyrobów na rynek. „W momencie ograniczenia ilości projektowania i związanych z tym kosztów, można osiągnąć atrakcyjny zwrot z inwestycji”, dodaje Kickinger.
Żadnych kolizji
Do tego celu producent OEM lub operator maszyny potrzebuje oprogramowania systemowego mapp Trak, który współdziała z systemem ACOPOStrak. „Wspomniane oprogramowanie to praca naszych najlepszych programistów”, wyjaśnia specjalista ds. mechatroniki. Wykonali wiele skomplikowanych zadań matematycznych, które kryją się za funkcjonalnością ACOPOStrak, w tym zapobieganie kolizjom, dzielenie i łączenie strumieni wyrobów przy pełnej prędkości oraz obliczanie optymalnych ścieżek.
Dzięki czemu bezpośredni programiści tworzący aplikację oszczędzają cenny czas. Kolizje nie występują nawet w przypadku wyrobów o różnych wielkościach i wagach. Wielkość wyrobu można skonfigurować ręcznie lub zmierzyć czujnikiem, a mapp Trak automatycznie dostosuje sterowanie wózkiem w celu uniknięcia kolizji.
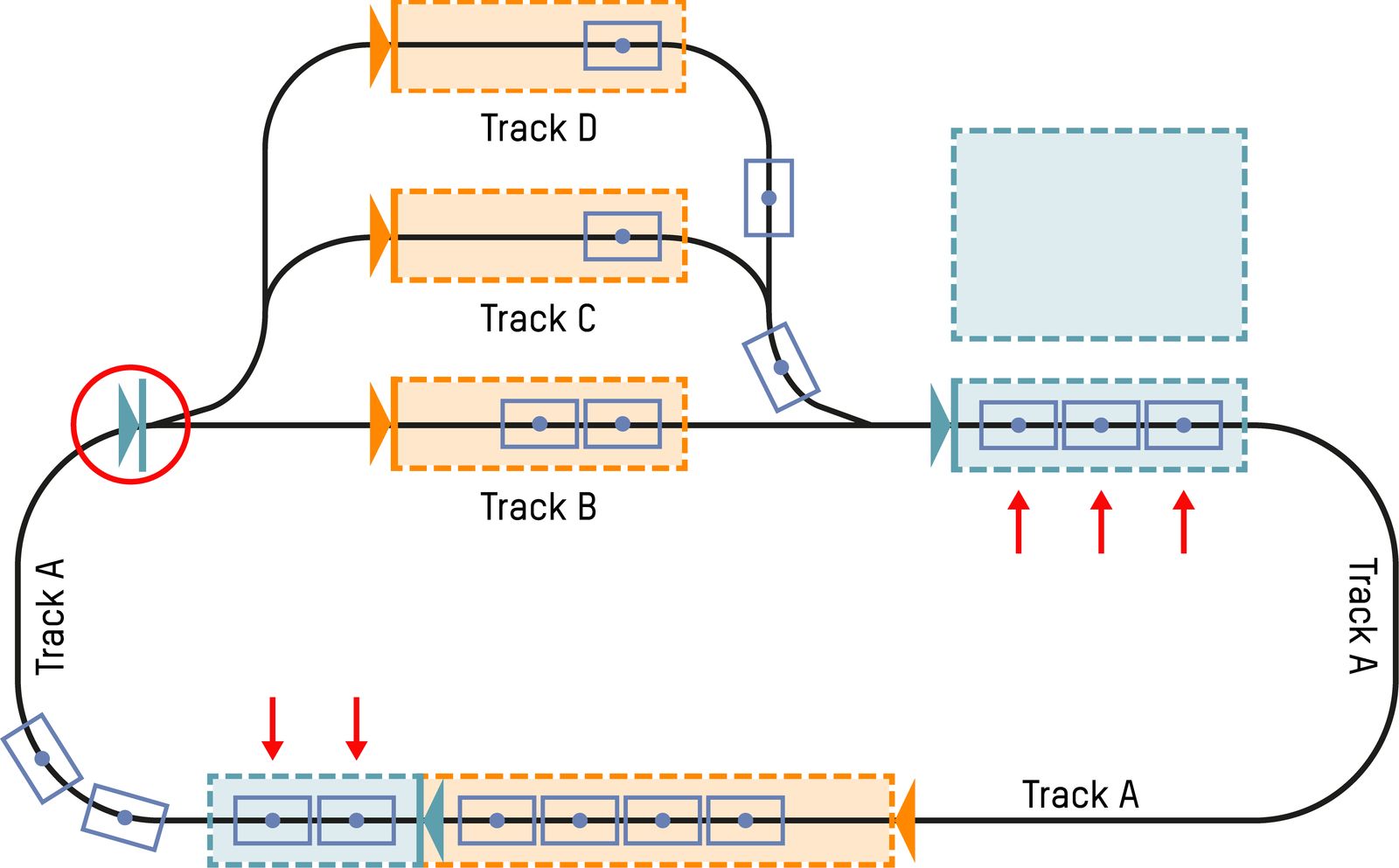
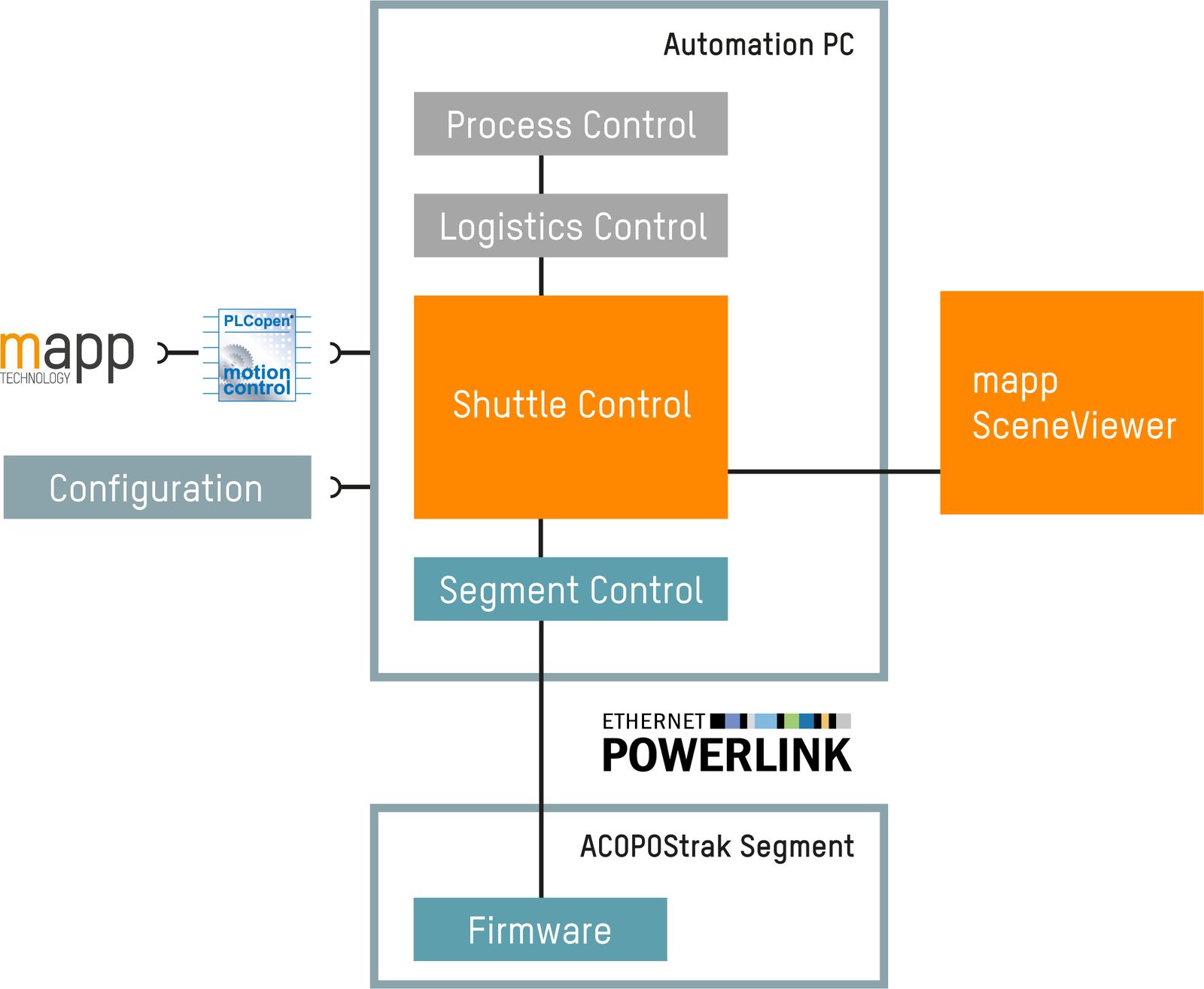
Programowanie ukierunkowane na procesy
Kolejnym czynnikiem, który istotnie upraszcza projektowanie jest programowanie ukierunkowane na procesy. Przy użyciu mapp Trak programista aplikacji opisuje zasady zachowania się wózków na trasie. Tworzone w ten sposób zasady aktywowane są w momencie, kiedy wózek przekracza zdefiniowany wcześniej, wirtualny punkt (trigger). Ta prosta metodologia oparta na maszynach stanów sprawia, że wdrożenie sekwencji ruchu jest wysoce skuteczne.
Dzięki ACOPOStrak nie ma potrzeby projektowania osi i profili ruchu oddzielnie dla każdego wózka,
czyli wyeliminowano czasochłonne zadanie w przypadku setek wózków poruszających się po wielu możliwych ścieżkach.
Kolejną korzyścią płynącą z programowania ukierunkowanego na procesy jest możliwość wycofywania wózków ze ścieżki lub ich dodawanie w razie potrzeby, bez jakichkolwiek zmian w oprogramowaniu aplikacji.
Symulowanie efektywnego działania
Możliwości symulacji zawarte w mapp Trak zapewniają wyraźne wizualne potwierdzenie, że system może działać bezproblemowo. Programiści mogą przetestować najwyższy poziom wydajności bez względu na liczbę wózków czy zadaną przez aplikację prędkość ruchu. „Programiści mogą sprawdzać wiele scenariuszy na swoim komputerze biurowym bez ograniczeń i ryzyka występującego w przypadku rzeczywistego systemu”, twierdzi kierownik projektu B&R ds. systemów transportu Davide Migliorisi. System, który działa na komputerze programisty jest identyczny z tym, który zostanie później zastosowany w sterowniku. Możliwe jest przełączanie pomiędzy środowiskiem symulacyjnym a rzeczywistym w każdym momencie.
Narzędzie Scene Viewer firmy B&R można również wykorzystać do wizualizacji współpracy wózków wahadłowych z dodatkowymi elementami mechanicznymi, jak śrubokręty, etykieciarki czy roboty. Wystarczy tylko zaimportować plik STEP odpowiedniego elementu maszyny i modelować jego ruch w przestrzeni i czasie.
Pozwala to programiście na symulację nie tylko ścieżki ruchu, lecz także integracji z pozostałymi elementami maszyny. „Nasi klienci najbardziej doceniają praktycznie rozwiązania symulacyjne systemu mapp Trak”, potwierdza Davide Migliorisi. „Natomiast interakcja z zewnętrznymi elementami maszyny działa tak idealnie dlatego, że ACOPOStrak ma geny całej rodziny serwonapędów ACOPOS”, dodaje. Rodzina produktów ACOPOS jest wyposażona w wyszukane funkcje obsługi systemów jedno i wieloosiowych, a także w rozbudowane opcje synchronizacji osi.
W ten sposób można ściśle skoordynować ruch wózków z osiami napędzanymi za pomocą serwonapędów ACOPOS przy użyciu poleceń PLCopen i wyświetlić je jako symulowane obiekty w oprogramowaniu Scene Viewer.
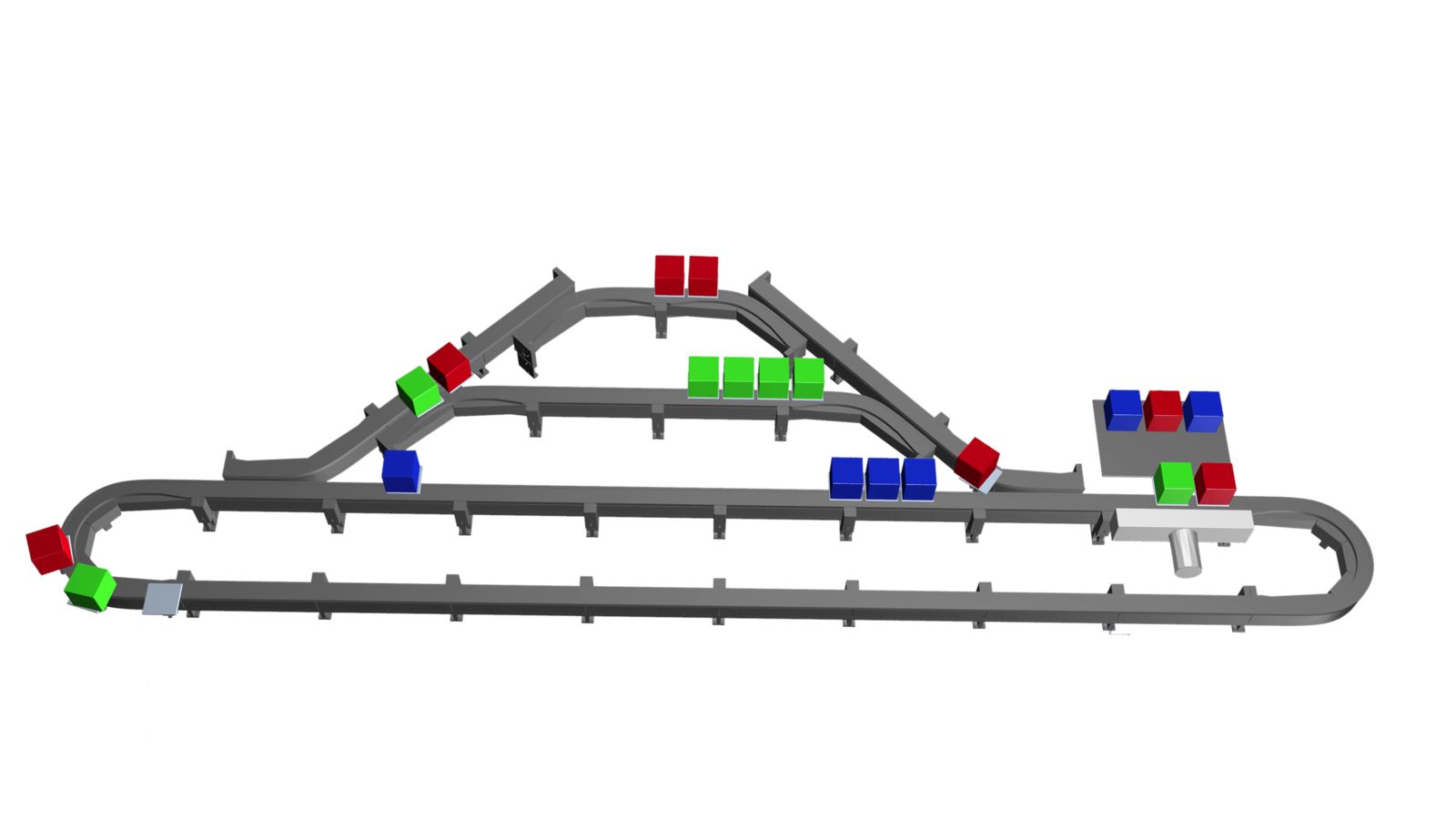
Maksymalna elastyczność
Klienci już potwierdzili, że ACOPOStrak jest łatwy w obsłudze. Klickinger twierdzi, że jeden z klientów, który rozszerzył istniejącą maszynę o dodatkowe segmenty silnika liniowego za pomocą ACOPOStrak, poświęcił tylko piętnaście minut na opracowanie oprogramowania przed ponownym uruchomieniem maszyny. Koncepcja rozdzielenia programowania od rzeczywistych urządzeń wprowadzona do systemu ACOPOStrak naprawdę robi wrażenie.
Dzięki oprogramowaniu systemowemu mapp Trak dane wyrobów można wyraźnie połączyć z konkretnym wózkiem, na którym dany wyrób znajduje się w danym momencie. „Jest to najwyższy poziom elastyczności”, twierdzi Kickinger. Przykładowo zapisane dane wyrobu na farmaceutycznej linii produkcyjnej mogą zawierać dokładny skład substancji czynnej oraz niepowtarzalny identyfikator wyrobu. Możliwe jest także przechowywanie danych i czasu przejścia poszczególnych wyrobów przez każdą ze stacji produkcyjnych. Ułatwia to programistom aplikacji wdrożenie śledzenia zgodnego z wymogami FDA.
Złożoność łatwa w obsłudze
mapp Trak sprawia, że wózki nie wchodzą ze sobą w kolizje, nie przekraczają barier wirtualnych ani nie naruszają zadanych limitów prędkości. Takie możliwości, łatwość programowania oraz zintegrowana funkcja symulacji sprawiają, że elastyczny system transportu ACOPOStrak firmy B&R jest bardzo prosty w obsłudze. Dzięki niemu wdrażanie nowych wyrobów w partiach o dowolnej wielkości jest szybkie i generuje minimalne koszty dodatkowe. Jest to kluczowy aspekt pozyskiwania nowych zamówień produkcyjnych z krótkim terminem realizacji.
Przygotował: Carmen Klingler-Deiseroth, niezależny dziennikarz
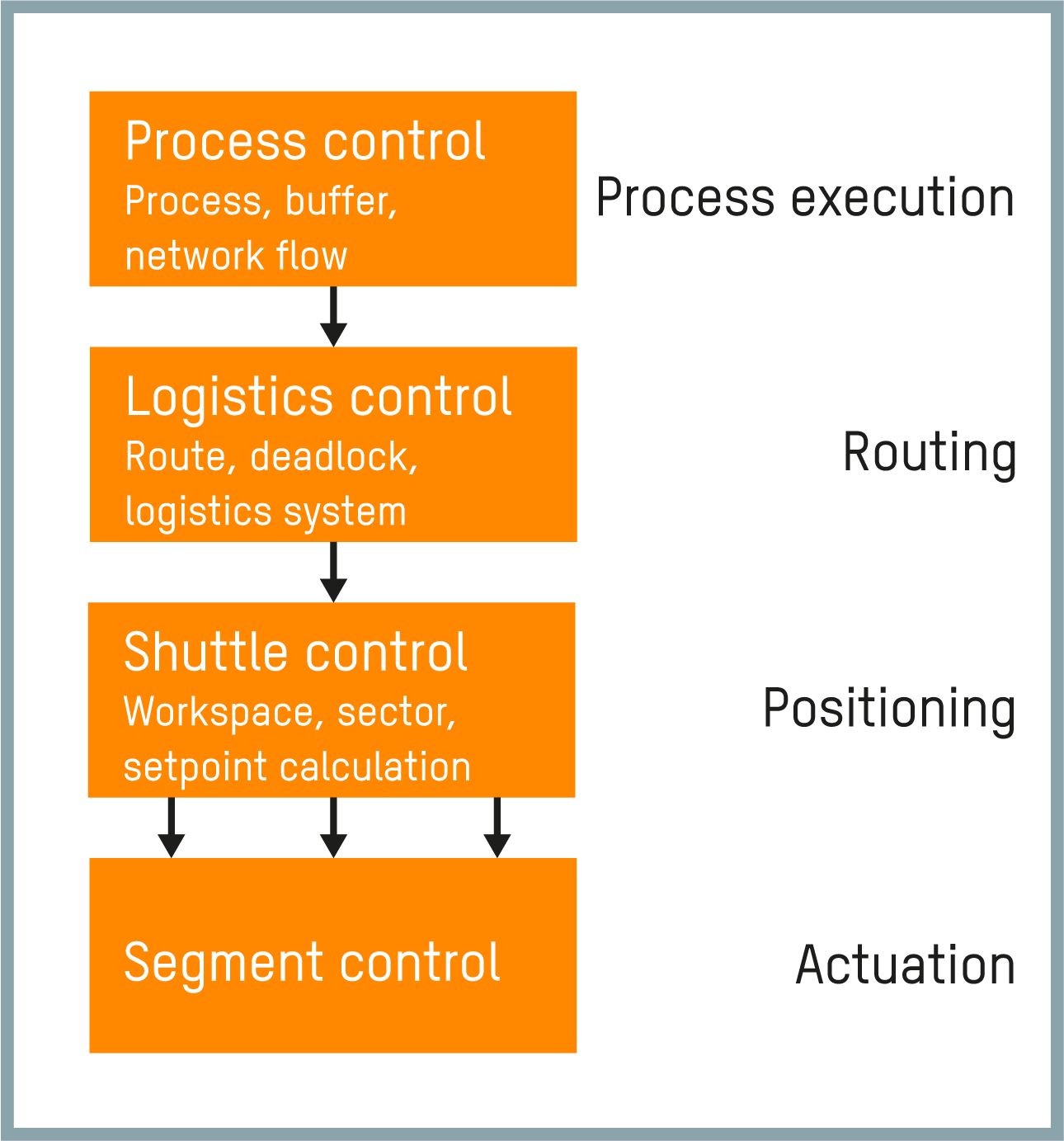
Architektura mapp Trak
Architektura oprogramowania mapp Trak jest podzielona na cztery podstawowe poziomy. Najniższy – poziom sterowania segmentami – steruje ruchem wózków znajdujących się w danym segmencie.
Kolejny poziom – sterowanie wózkami – służy między innymi do obliczania punktów przełączania wózków. Jeżeli programista aplikacji chce połączyć wózki z zewnętrzną osią lub innym wózkiem, na przykład przy użyciu bloków funkcji modułowych PLC, odbywa się to właśnie na tym poziomie. Również na tym poziomie obsługiwane jest dodawanie wózków do ścieżki lub ich wyłączanie ze ścieżki, np. gdy system ACOPOStrak jest stosowany w połączeniu z tradycyjnymi przenośnikami taśmowymi lub jeżeli wózki wahadłowe są usuwane lub dodawane przez ludzi albo roboty.
Elementy oprogramowania na trzecim poziomie – sterowanie logistyką – tworzą automatyczne ścieżki pomiędzy poszczególnymi stacjami produkcji. Czwarty poziom służy sterowaniu procesem. Jest to również poziom interfejsu programowania, który służy projektantowi do opisania przebiegu procesu.