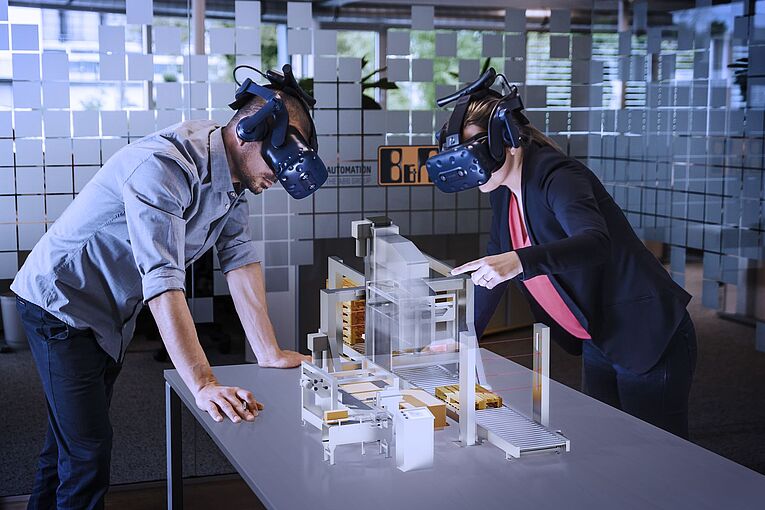
Virtual meets reality
Changes to a finished machine cost time and money, but you can save both. How? By testing a virtual model of your machine through simulation. That way, you can identify necessary changes early – when they are much cheaper and easier to implement.
Changes to a finished machine cost time and money, but you can save both. How? By testing a virtual model of your machine through simulation. That way, you can identify necessary changes early – when they are much cheaper and easier to implement.