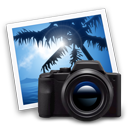
Gruppieren ohne Lücken
Einzelne Maschinenmodule miteinander zu verbinden, erfordert häufig einen großen Aufwand und viel Platz. Mithilfe von ACOPOStrak hat es das Unternehmen Optima geschafft, einen nahtlosen Übergang herzustellen.
Einzelne Maschinenmodule miteinander zu verbinden, erfordert häufig einen großen Aufwand und viel Platz. Mithilfe von ACOPOStrak hat es das Unternehmen Optima geschafft, einen nahtlosen Übergang herzustellen.