Jak powiedział grecki filozof Arystoteles: „Całość jest czymś więcej niż sumą części”. Choć wniosek ten został sformułowany na długo przed powstaniem koncepcji Industry 4.0 i Inteligentnej Fabryki, jego trafność w odniesieniu do produkcji maszyn jest uderzająca. W wyniku połączenia sprzętu, oprogramowania i kodu programu nie powstaje automatycznie funkcjonalna maszyna. Tylko doskonałe współdziałanie tych połączonych ze sobą „części” daje w rezultacie funkcjonującą „całość”. W osiągnięciu tego celu kluczową rolę odgrywa symulacja.
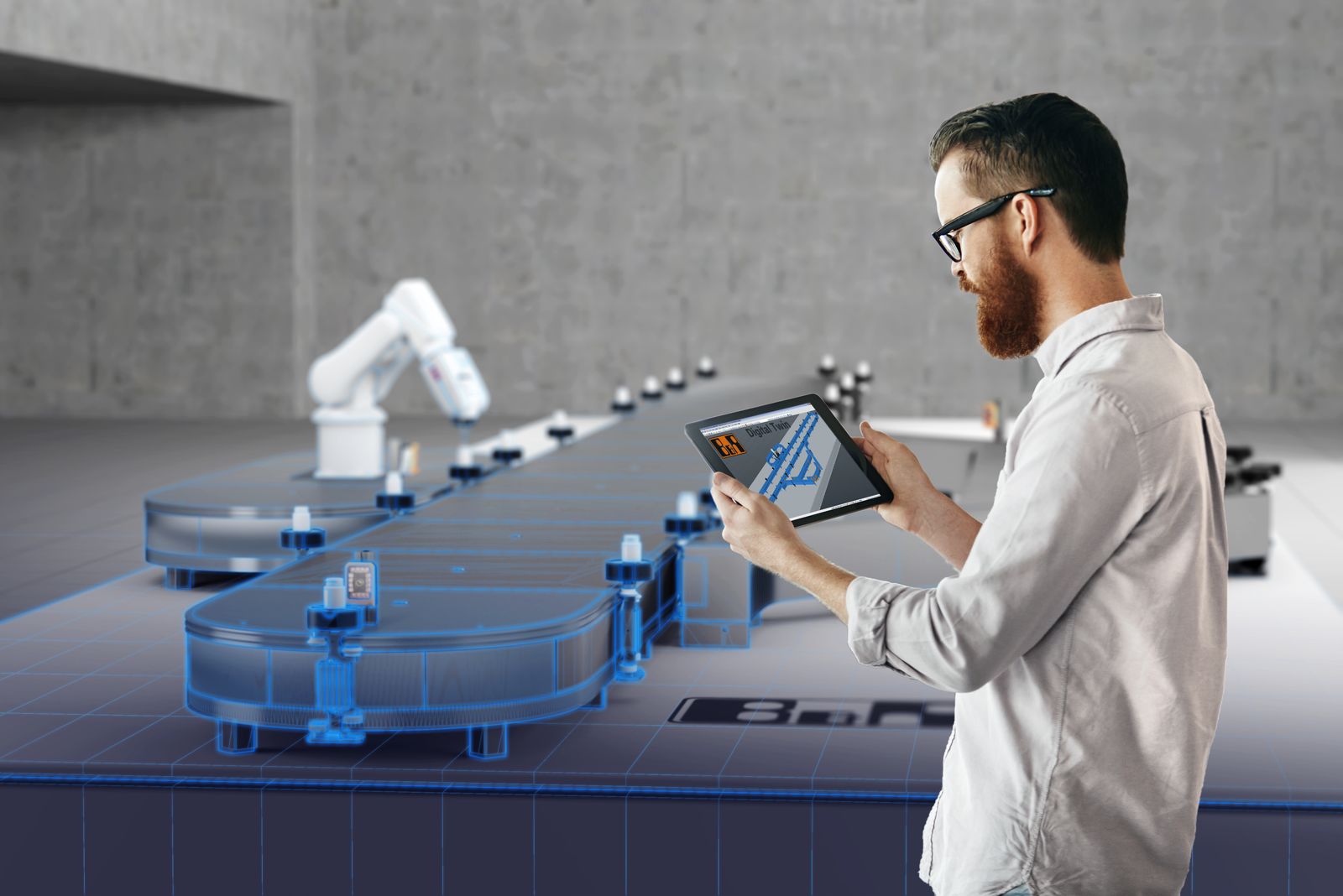
Jaką rolę w produkcji maszyn i inżynierii instalacji odgrywa symulacja? „Odpowiedź jest prosta” – mówi Isabella Laasch, menedżer produktu ds. symulacji w B&R. „Jest to klucz do osiągnięcia kolejnego poziomu efektywności w każdej fazie cyklu życia maszyny.”
Maszyny stają się coraz bardziej złożone. Oznacza to również, że współdziałanie części mechanicznej, urządzeń elektrycznych i automatyki staje się coraz trudniejsze. Testowanie możliwych sekwencji maszyny bezpośrednio na fizycznym systemie wiąże się z wysokimi kosztami i jest ogólnie rzecz biorąc nieefektywne. Dotyczy to każdej fazy życia maszyny: projektowania, uruchamiania i bieżącej eksploatacji.
Kosztowne i czasochłonne wady projektowe
Nawet w pierwszej fazie cyklu eksploatacji maszyna przechodzi przez wiele etapów. W każdym z nich mogą wystąpić poważne usterki. Zasada dziesięciu stanowi, że koszt naprawy usterki wzrasta dziesięciokrotnie na każdym etapie rozwoju maszyny, na którym usterka nie została wykryta. Jak najszybsze usunięcie usterki przyspiesza zatem proces rozwoju i pozwala zaoszczędzić koszty.
Jeśli jednak usterki występują w całym procesie rozwoju, nie zostaną wykryte aż do etapu uruchomienia. „Jeśli podczas uruchamiania maszyny będzie pojawiał się jeden problem za drugim, ostateczny efekt będzie katastrofą” – twierdzi Laasch. Nie dość, że poniesiono już koszty produkcji prototypu, to teraz zespół programistów jest zajęty poszukiwaniem i usuwaniem źródła problemów. W przypadku uszkodzenia części sprzętowej pojawiają się dodatkowe koszty części zamiennych oraz ewentualne opóźnienie z powodu długiego czasu dostawy. W najgorszym przypadku konstruktor maszyny może nawet zostać obciążony karami umownymi, jeśli nowa maszyna nie zostanie dostarczona na czas.
Symulacja jest kluczem
Zdaniem Laasch: „Musimy zasadniczo znaleźć sposób na cyfrowe odwzorowanie maszyny w każdej fazie jej cyklu życia. Według mnie, jedynym takim sposobem jest symulacja.” W środowisku wirtualnej symulacji tworzony jest cyfrowy bliźniak maszyny. Za pomocą cyfrowego bliźniaka można sprawdzić współdziałanie poszczególnych komponentów podczas projektowania i wirtualnie uruchomić maszynę.
![]() | Philipp Wallner Kierownik Branżowy, MathWorks „Dzięki konstruowaniu opartemu na modelach, można zapewnić, że maszyna będzie działać na wczesnym etapie, co zmniejsza ryzyko awarii do minimum. Modele symulacyjne stanowią podstawę fazy projektowania, wirtualnego uruchomienia i cyfrowych bliźniaków. Inwestycja w symulację zwraca się zwykle w ciągu pierwszego roku.” |
Ścisła współpraca z ekspertami ds. symulacji
Konstruktorzy maszyn mogą wybierać spośród szerokiej gamy narzędzi symulacyjnych. Oferta obejmuje zarówno narzędzia do symulacji sprzętu i maszyn, jak i symulacji procesów. Z tego względu firma B&R poświęciła wiele lat na współpracę z różnymi ekspertami w dziedzinie symulacji i integrację różnych narzędzi w swoim systemie automatyki.
„We współpracy z naszymi partnerami – firmami MathWorks, Maplesoft, machineering, ISG i innymi – oferujemy szeroki zakres opcji symulacji i mamy odpowiednie rozwiązanie dla każdej aplikacji. „Decydującym czynnikiem jest tutaj fakt, że nasi klienci mają swobodę wyboru narzędzia symulacyjnego, które najlepiej nadaje się do ich maszyny. Środowisko rozwoju B&R jest w każdym przypadku głównym narzędziem.”

Właściwe narzędzie do każdego wymogu
Oprogramowanie symulacyjne firm Maplesoft i MathWorks może na przykład wydajnie i dokładnie mapować komponenty maszyn, a także symulować momenty i siły na mechanice maszyn. Pozwala to łatwo przetestować różne przypadki obciążeń. Testy na prawdziwym systemie wymagałyby wielu godzin pracy i wielu zasobów. Nadmierne obciążenie może doprowadzić do uszkodzenia cennego sprzętu, który potem trzeba będzie wymienić. Dzięki symulacji konstruktor maszyny może jednak od razu stwierdzić, czy maszyna poradzi sobie z danym obciążeniem.
![]() | Chris Harduwar Wiceprezes ds. rozwoju biznesu, Maplesoft „Kiedy konstruktorzy maszyn napotykają na problemy z wydajnością, potrzebują szybkiego rozwiązania, które nie zagrozi planowanej marży zysku. Dynamiczne, oparte na fizyce cyfrowe bliźniaki pozwalają konstruktorom maszyn wykrywać problemy w ich projektach i wymyślać sposoby ich rozwiązania bez dodatkowych kosztów sprzętowych. |
Narzędzia firm machineering i ISG obejmują z kolei obszar symulacji procesów. Pokazują one dynamiczne zachowanie kompletnej maszyny w trzech wymiarach. Dzięki temu wszystkie czynniki dynamiczne, które mają wpływ na przepływ materiału, mogą być badane w czasie rzeczywistym za pomocą cyfrowego bliźniaka. Konstruktor maszyny otrzymuje natychmiastową wizualną informację zwrotną o tym, jak różne kombinacje komponentów maszyny wpływają na jej zachowanie. Na wczesnym etapie można również zidentyfikować i wyeliminować niepotrzebne przestoje.
Wykorzystanie danych na potrzeby konserwacji predykcyjnej
Nawet po opracowaniu i wdrożeniu maszyny, cyfrowy bliźniak nie przestaje wnosić wartości dodanej. Cyfrowy bliźniak nadal działa w szafie sterowniczej jako wirtualna kopia maszyny, wykorzystując dane operacyjne w czasie rzeczywistym do tworzenia dokładnych prognoz dotyczących stanu i pozostałego okresu eksploatacji komponentów maszyny. „Jeśli zachowanie rzeczywistej maszyny odbiega od zachowania cyfrowego bliźniaka – na przykład z powodu zużytego łożyska – różnica jest natychmiast wykrywana” – wyjaśnia Laasch. Zebrane dane są wykorzystywane do predykcyjnego utrzymania ruchu, dokumentacji usterek, systemów zdalnego utrzymania ruchu itp.
![]() | Dr Georg Wünsch Dyrektor zarządzający, machineering GmbH & Co. KG „Nasze oprogramowanie symulacyjne iPhysics zapewnia spójność w inżynierii. Łączy w sobie wszystkie dziedziny, począwszy od MCAD, ECAD i automatyzacji, aż po produkcję i serwis posprzedażowy. Dzięki dodatkowemu połączeniu systemów AR i VR, złożone maszyny mechatroniczne są w każdej chwili całkowicie zabezpieczone.” |
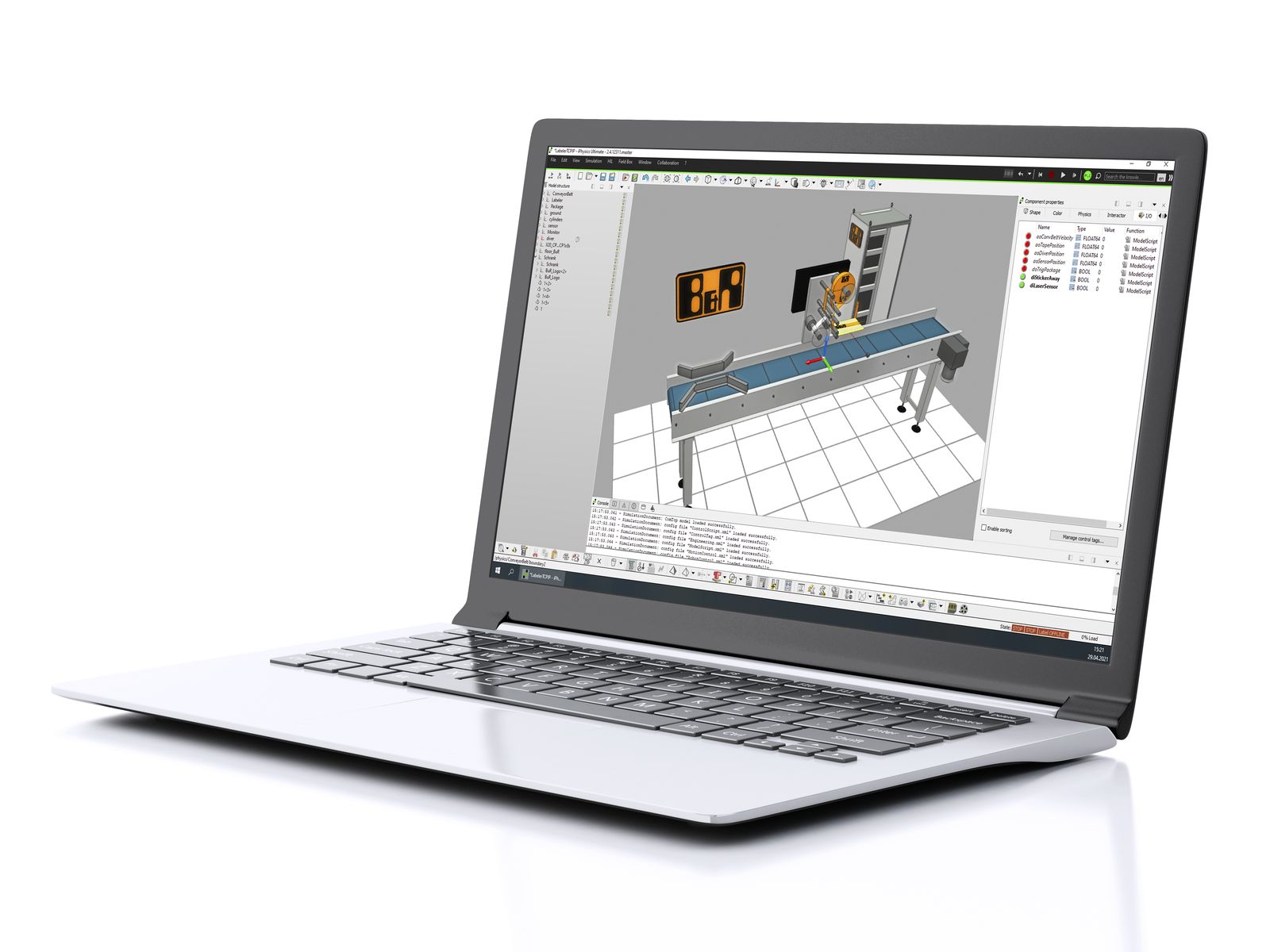
Krótszy czas szkolenia
Cyfrowy odpowiednik maszyny otwiera również nowe możliwości szkolenia operatorów maszyn i techników serwisowych. Teoretycznie mogą oni nauczyć się, jak pracować z interfejsem człowiek-maszyna lub z samą maszyną, zanim jeszcze zostanie ona dostarczona na miejsce. Dzięki temu znacznie skraca się czas potrzebny na przeszkolenie nowych operatorów.
Cyfrowy bliźniak jest również coraz częściej wykorzystywany w wirtualnych salonach wystawowych, co pozwala działowi sprzedaży na prezentowanie nowych maszyn potencjalnym klientom w dowolnym czasie, nawet poza targami czy imprezami. Za pomocą zestawów do rzeczywistości rozszerzonej można nawet nałożyć cyfrową maszynę na realistyczne otoczenie. Umożliwia to testowanie scenariuszy warunkowych w przypadku projektowania i opracowywania maszyn z ruchomymi obiektami.
![]() | Dr Christian Daniel Menedżer biznesu ds. technologii symulacji, ISG Industrielle Steuerungstechnik GmbH „Jeśli skonfiguruje się scenariusze symulacyjne jako cyfrowe bliźniaki z wirtualnymi komponentami wielokrotnego użytku z biblioteki, wówczas mogą one być również wykorzystywane przez właściciela instalacji do optymalizacji produkcji, modernizacji oraz jako podstawa innowacyjnych koncepcji szkoleniowych i serwisowych.” |
Szybszy rozwój maszyn
„Cyfrowy bliźniak towarzyszy maszynie na każdym etapie jej cyklu życia” – zapewnia Laasch. „Ponadto stanowi punkty wyjścia do opracowania nowych funkcji i przyszłych ulepszeń maszyny.” Konstruktor maszyn może na przykład wykorzystać wiedzę uzyskaną podczas pracy do optymalizacji systemu. Model symulacyjny może być następnie wykorzystany do przetestowania planowanych modyfikacji. Skraca to do minimum czas przestoju w przypadku modernizacji i przyspiesza proces projektowania kolejnej generacji maszyn.
![]() | Isabella Laasch Menedżer produktu ds. symulacji, B&R „We współpracy z naszymi partnerami – firmami MathWorks, Maplesoft, machineering, ISG i innymi – oferujemy szeroki zakres opcji symulacji i mamy odpowiednie rozwiązanie dla każdej aplikacji. Nasi klienci mają swobodę wyboru narzędzia symulacyjnego, które najlepiej nadaje się do ich maszyny. Środowisko rozwoju B&R jest w każdym przypadku głównym narzędziem.” |
Autor: Carola Schwankner, redaktor działu komunikacji korporacyjnej B&R