Produkcja płytek półprzewodnikowych jest procesem złożonym. Aby je zbadać, igły próbników muszą być prowadzone tak, aby miały kontakt z podkładkami, które mierzą na boku jedynie mikrometry. Sterowniki dla tego procesu muszą spełniać ekstremalne wymagania ochrony kompatybilności elektromagnetycznej (EMC) i niezawodności. Firma Cascade zbadała rynek pod kątem optymalnego rozwiązała – i znalazła je w B&R.
Co wspólnego ze sobą mają piekarnik wielofunkcyjny, zegar cyfrowy, toster i nawigacja GPS? Po prostu: wszystkie one korzystają z maleńkich zintegrowanych obwodów lub mikrochipów. Na współczesnym rynku konsumenckim niemal wyzwaniem jest znalezienie produktu, który nie ma w sobie jakiegoś rodzaju elektroniki. Produkcja płytek półprzewodnikowych jest procesem złożonym. Aby je zbadać, wtyki próbników muszą być prowadzone tak, aby miały kontakt z podkładkami, które mierzą na boku jedynie mikrometry. Sterowniki dla tego procesu muszą spełniać ekstremalne wymagania ochrony kompatybilności elektromagnetycznej (EMC) i niezawodności. Firma Cascade zbadała rynek pod kątem optymalnego rozwiązała – i znalazła je.
Ogromna szerokość pasm w aplikacjach stanowi znaczne wyzwanie dla konstruktorów komponentów półprzewodnikowych. Stają oni stale wobec presji, aby integrować rosnący zakres funkcji na coraz mniejszych chipach, a jednocześnie redukować koszty produkcji.
Już obecnie nawet smartwatch na twoim nadgarstku jest tańszy i ma większe możliwości niż biurowy komputer PC, jakiego używałeś zaledwie 10 lat temu. Plasterki materiału półprzewodnikowego – znane jako "wafelki" – zawierają więcej niż 1 000 chipów z miliardami tranzystorów i innych komponentów i obecnie mają do 300 milimetrów średnicy. Taka złożoność sprawia, że metody projektowania i zatwierdzania nowych projektów oraz metody produkcji stały się bardzo wymagającymi procesami. Niemniej jednak ilość czasu przeznaczanego na projektowanie gwałtownie spada.
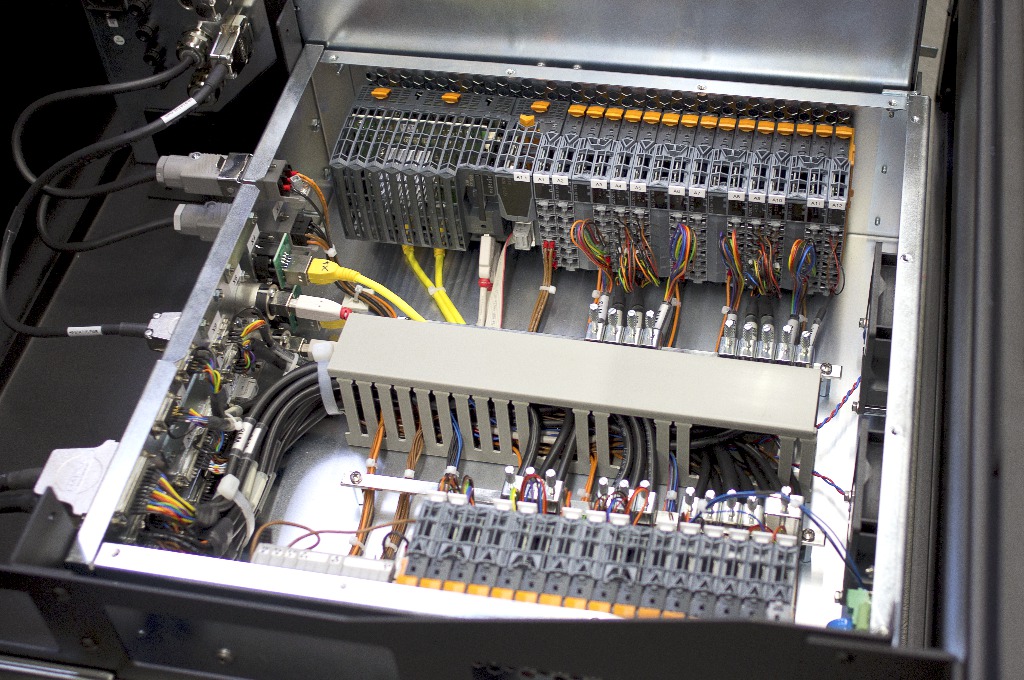
Dokładne badanie zapewnia wysoką jakość
Aby zatwierdzić funkcjonalność nowo zaprojektowanych komponentów i zapewnić jednolitą jakość po osiągnięciu przez nie produkcji seryjnej, płytki są poddawane szerokim badaniom na stanowiskach testowania natychmiast po ich wyprodukowaniu. Każda płytka jest przekazywana do komory pomiarowej, unieruchamiana z dokładnością do mikrometra przy pomocy uchwytu i doprowadzana do określonej temperatury. Następnie wtyki są wprowadzane do specjalnie zaprojektowanych punktów kontaktowych na chipie.
Pomiary zewnętrzne i instrumenty badające, które same mogą wypełnić całą szafę sterowniczą, dyktują pozycje na podstawie programu testującego, a następnie inicjują pomiary. Badanie jest przeprowadzane w temperaturze wahającej się od -55 °C do 300 °C. W zależności od aplikacji, mierzone natężenia prądu mogą sięgać od kilkunastu femtoamperów (liczba z 15 zerami po przecinku, lub 6 250 elektronów na sekundę), do 400 amperów. Nierzadko częstotliwości pomiarów sięgają rzędu gigaherców –na przykład na chipach wykorzystywanych w systemach radarowego pomiaru liczby pojazdów przejeżdżających w zadanym interwale czasu. Znaczącą cechą tych specyfikacji wymagań jest więc wykluczenie wszystkich źródeł zakłóceń elektromagnetycznych.
Najnowocześniejsza komora pomiarowa zapobiega powstawaniu interferencji w czasie badań
Cascade Microtech GmbH, jednostka zależna Cascade Microtech Inc., z główną siedzibą w Beaverton (USA), dobrze zna te wymagania. Jako wiodący światowy producent rozwiązań sondujących płytki półprzewodnikowe, firma ta w roku 1992 jako pierwsza wprowadziła swoje opatentowane stanowiska probiercze i od tego czasu stale je ulepsza. Mając ponad 50-letnie doświadczenie w projektowaniu technologi precyzyjnego pozycjonowania, biegłość w posługiwaniu się związanymi z tym procesami jest integralną częścią codziennych czynności.
– W danych warunkach istnieje mnóstwo czynników, które należy wziąć pod uwagę, aby poprowadzić wtyki sondy tak, aby zetknęły się z podkładkami, które mierzą na boku jedyne 30 mikrometrów – wyjaśnia dr Jörg Kiesewetter. Kiesewetter jest kierownikiem działu R&D dla systemów sondujących w biurze Cascade Microtech'w Dreźnie. Tutaj 140 pracowników projektuje i buduje te układy dla ponad 800 klientów na całym świecie, w tym dla producentów półprzewodników takich jak IBM, Intel i Infinion, a także wielu organizacji, takich jak Interuniversity Microelectronics Center (IMEC) – czyli największe w Europie centrum badawcze dla nano- i mikroelektroniki.
Precyzyjne pozycjonowanie
Jeśli chodzi o osiągnięcie koniecznej precyzji, eksperci z Cascade Microtech mają w zanadrzu wiele mechanicznych i elektrycznych trików – co zostało dowiedzione imponującą liczbą 190 patentów. Na przykład wiele spośród 25 osi stołu krzyżowego, kamery cyfrowej czy innych urządzeń pomocniczych wymaga chłodzenia. – Nie ma możliwości bezpośredniego zmierzenia jakości kontaktu z chipem – wskazuje Kiesewetter, – jest więc sprawą zasadniczą, aby proces ten był sam w sobie niezawodny. Pojedynczy błąd pozycjonowania, nawet rzędu kilko mikrometrów, może skutkować tym, że cała płytka półprzewodnikowa lub karta stykowa z ponad 10 000 styków będzie bezużyteczna. Powodowałoby to wydatek setek tysięcy euro na odszkodowania, nie wspominając o nadwyrężeniu wizerunku firmy. Jednak wymagania nadal gwałtownie rosną. – Podkładki kontaktowe zajmują cenną powierzchnię, więc są one wykonywane w coraz mniejszym rozmiarze. Wkrótce ich boki będą mierzyły 20 mikrometrów – mniej niż jedna czwarta przekroju ludzkiego włosa. Do tego wszystkiego dochodzą jeszcze liczne żądania specjalne użytkowników urządzeń. Aby nadążyć za wymaganiami dotyczącymi montażu, firma Cascade Microtech rozpoczęła ocenę koncepcji nowej konstrukcji sterownika.
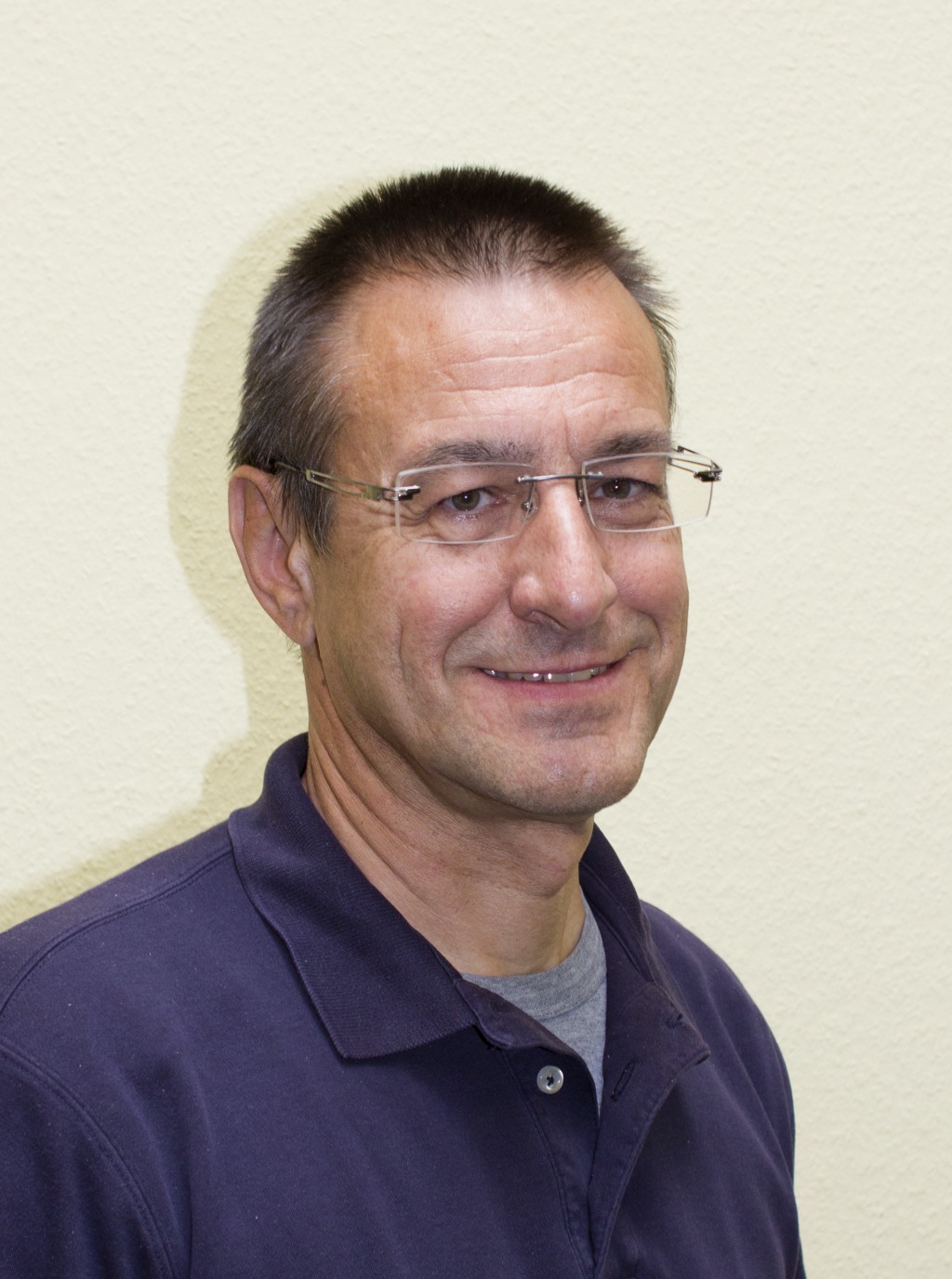
– Pełna modułowość, jaką uzyskaliśmy, pomogła nam znacząco zredukować czas konstruowania – relacjonuje Kiesewetter. – Wyjątkowe wsparcie ze strony inżynierów B&R w Lipsku oszczędziło nam cennego czasu. dr Jörg Kiesewetter, Kierownik Działu R&D, Cascade Microtech
Modułowość przyspiesza rozwój
Poza długoterminową dostępnością produktu, ochroną EMC i dostępem do światowej sieci sprzedaży i serwisu, również modułowość układu sterowania była kluczowym kryterium. Byłoby również konieczne kontynuowanie rozwoju istniejącego kodu programu C++. Firma B&R oferowała najbardziej kuszące rozwiązanie, a Cascade Microtech ma już plany wdrożenia go w urządzeniach dodatkowych. Konstruktorzy mieli pełną wolność decydowania, czy zastosować silniki DC czy krokowe dla różnych zadań sterowania napędami. Przy pomocy oprogramowania Generic Motion Control firmy B&R, służącego do sterowania osiami, firma Cascade Microtech miała możliwość utrzymania osobno sprzętu i oprogramowania oraz dostosowania różnych typów silników bez potrzeby wprowadzania jakichkolwiek zmian kodów. – Pełna modułowość, jaką uzyskaliśmy, pomogła nam znacząco zredukować czas konstruowania – relacjonuje Kiesewetter. – Wyjątkowe wsparcie ze strony inżynierów B&R w Lipsku oszczędziło nam cennego czasu.