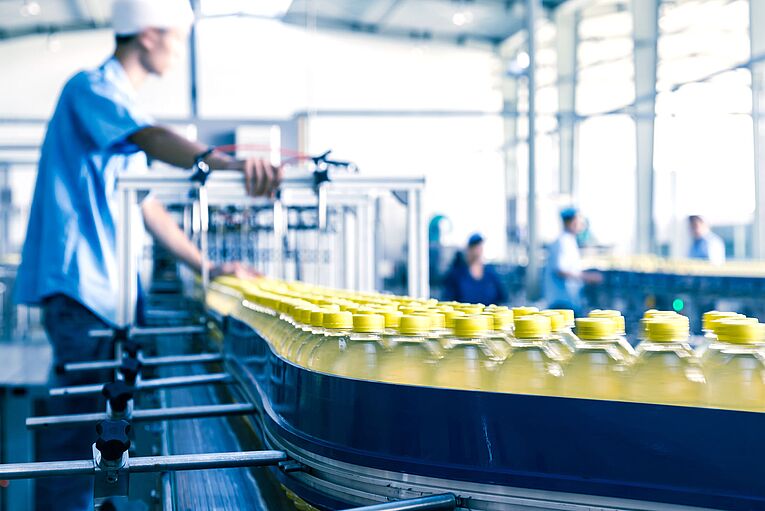
Off-the-chart speed with an off-the-shelf solution
B&R reACTION distributes computational load to boost performance of time-critical processes
B&R reACTION distributes computational load to boost performance of time-critical processes
Większość producentów potrafi zapewne wskazać kilka kluczowych procesów w swojej branży, w których czas jest szczególnie ważny – obszarów, gdzie precyzyjne wykonanie jest niezbędnym warunkiem wysokiej jakości i wydajności produkcji. Gdy liczy się każda mikrosekunda, nawet najpotężniejszy sterownik PLC może znaleźć się u kresu swoich możliwości. Technologia reACTION firmy B&R zapewnia ultraszybkie czasy reakcji przy niskich kosztach i niewielkim wysiłku dzięki wykorzystaniu gotowego sprzętu i oprogramowania.
Butelkowanie jest dobrym przykładem procesu, w którym czas odgrywa krytycznie ważną rolę. Najwyższa jakość i maksymalna przepustowość możliwe są tylko przy ścisłej synchronizacji czujników i zaworów w czasie rzeczywistym. Podobne wymagania występują przy nakładaniu kropek kleju na opakowania, sortowaniu przedmiotów w zakładzie recyklingu czy laserowym cięciu blachy. „Niegdyś krótkie czasy reakcji potrzebne w takich zastosowaniach wymagały użycia specjalnego sprzętu” – opowiada Andreas Hager, menadżer produktu B&R ds. systemów sterowania.
Swoją technologią reACTION firma B&R udowadnia, że można to zrobić inaczej. Programy opracowane w języku FBD (Function Block Diagram ), w środowisku inżynierskim Automation Studio są wykonywane bezpośrednio na modułach I/O B&R z serii X20 i X67. W ten sposób moduły I/O zostają przekształcone w „ministerowniki” zdolne do niezależnej obsługi określonych procesów i rozłożenia obciążenia obliczeniowego na wiele systemów.
Zlecanie modułom I/O czasowo-krytycznych programów pozwala osiągnąć ultrakrótkie czasy reakcji – do 1 µs. Mniej obciążony sterownik PLC nie musi wówczas mieć aż tak dużej mocy. A co ważne: możliwe jest również oddzielenie czasu reakcji od czasu cyklu sieci przemysłowej. Optymalizacja czasu cyklu może przynieść znaczny wzrost wydajności. Dzięki atrakcyjnej cenie modułów reACTION firmy B&R korzyści płynące z ultraszybkiej automatyzacji stają się teraz udziałem szerszej niż dotąd gamy maszyn.
Jak każdy inny program sterowania, program reACTION może być opracowany w Automation Studio przy użyciu bloków funkcyjnych, zgodnie z normą IEC 61131-3. Jest on zapisywany centralnie w sterowniku PLC, w zależności od potrzeb przekazywany do jednego lub kilku modułów I/O i tam przechowywany. Różne produkty wymagają, rzecz jasna, różnych receptur, dlatego możliwe jest również załadowanie nowych programów do modułów podczas pracy, a zapisane programy mogą być w każdej chwili skopiowane do innych modułów. Wybór bloków funkcyjnych reACTION stale się zwiększa, a nowe bloki można dodawać do już działających maszyn, po prostu aktualizując oprogramowanie sprzętowe. Użytkownicy mogą również tworzyć własne bloki funkcyjne w oparciu o bloki dostarczone i wykorzystywać je do nadania przejrzystości złożonym programom. Programiści, którzy już pracują z Automation Studio nie potrzebują żadnego dodatkowego szkolenia.
Moduły reACTION, dostępne z maksymalnie ośmioma dowolnie konfigurowanymi wejściami i wyjściami analogowymi lub cyfrowymi, działają jako małe samodzielne sterowniki. „Przetwarzają one sygnały wejściowe, uruchamiają swój program i generują dane wyjściowe” – dodaje Hager. Podczas odczytu wejść cyfrowych program reACTION może określić nie tylko aktualny stan na początku cyklu, ale także dokładny punkt przełączenia z rozdzielczością 20 ns. Dodatkowo moduły mogą wykorzystywać POWERLINK, X2X lub X2X+ do komunikacji z dowolnymi innymi modułami X20 i X67 oraz oczywiście przesyłać dane do sterownika. W zależności od potrzeb swojej aplikacji, użytkownicy mogą wybierać pomiędzy modułami o stopniu ochrony IP20 do montażu w szafie sterowniczej a wariantami o stopniu ochrony IP67 do bezpośredniego montażu na obiekcie.
Inteligentne moduły I/O firmy B&R sprawdzają się w wielu zastosowaniach. Szczególnie dobrym przykładem jest maszyna drukarska do materiałów opakowaniowych jednego z klientów B&R. Andreas Hager wyjaśnia: „Obecnie pracuje z prędkością wstęgi 600 m/min, ale są już plany opracowania nowej, szybszej wersji. Aby obsłużyć wyższe prędkości, trzeba było znaleźć dodatkowe rezerwy w rozwiązaniu automatyzacji.”
Drukowanie materiału opakowaniowego to pierwszy etap procesu. Po nim, numer seryjny jest nanoszony laserowo na każdym opakowaniu w ściśle określonym miejscu. Czujnik wykrywa miejsce, w którym powinien znajdować się numer seryjny i generuje sygnał cyfrowy. Moduł X20 reACTION ocenia ten sygnał i generuje cyfrowy sygnał wyjściowy dla markera laserowego. Aby zminimalizować błędy podczas przyspieszania maszyny, czujnik i znacznik laserowy muszą być umieszczone jak najbliżej siebie. Ze względu na konstrukcję maszyny, minimalna odległość między nimi wynosi 55 mm. Czujnik wykrywający znaki rejestracyjne podłączony jest do kanału 1 modułu I/O, sygnał startowy dla znacznika laserowego do kanału 3.
Parametry dla modułu reACTION są wyliczane na podstawie aktualnej prędkości taśmy. Od odczytania pozycji przez czujnik do momentu, gdy można rozpocząć znakowanie, upływają następujące czasy: 1 ms czasu martwego w czujniku, 0,5 ms czasu filtra (krótsze sygnały nie mogą być przetwarzane), 0,04 ms czasu przetwarzania przez moduł reACTION (dwukrotność czasu cyklu reACTION, gdyż w najgorszym przypadku sygnał jest odbierany krótko po skanowaniu) oraz 2 ms czasu martwego w laserowym urządzeniu znakującym. Tym samym najkrótszy możliwy czas reakcji wynosi 3,54 ms.
Przy podanej odległości 55 mm daje to następującą prędkość maksymalną: 55 mm / 3,54 ms = 15,5 m/s = 932 m/min. Innymi słowy: drukarka może pracować nawet o 55% szybciej niż jej obecna prędkość 600 m/min – nic więc nie stoi na przeszkodzie, aby nowa generacja maszyn pracowała z większą prędkością wstęgi i wyższą przepustowością. Takimi historiami, jak ta klienci B&R raz po raz potwierdzają, że doskonałą wydajność automatyki można osiągnąć przy niskich kosztach i niewielkim wysiłku dzięki wykorzystaniu gotowego sprzętu i oprogramowania.