Machine vision cameras can be found in an increasing number of manufacturing systems – controlling processes, sorting products or performing quality inspection. Easily overlooked, however, is the important role played by lighting in helping these cameras achieve precise, repeatable results.
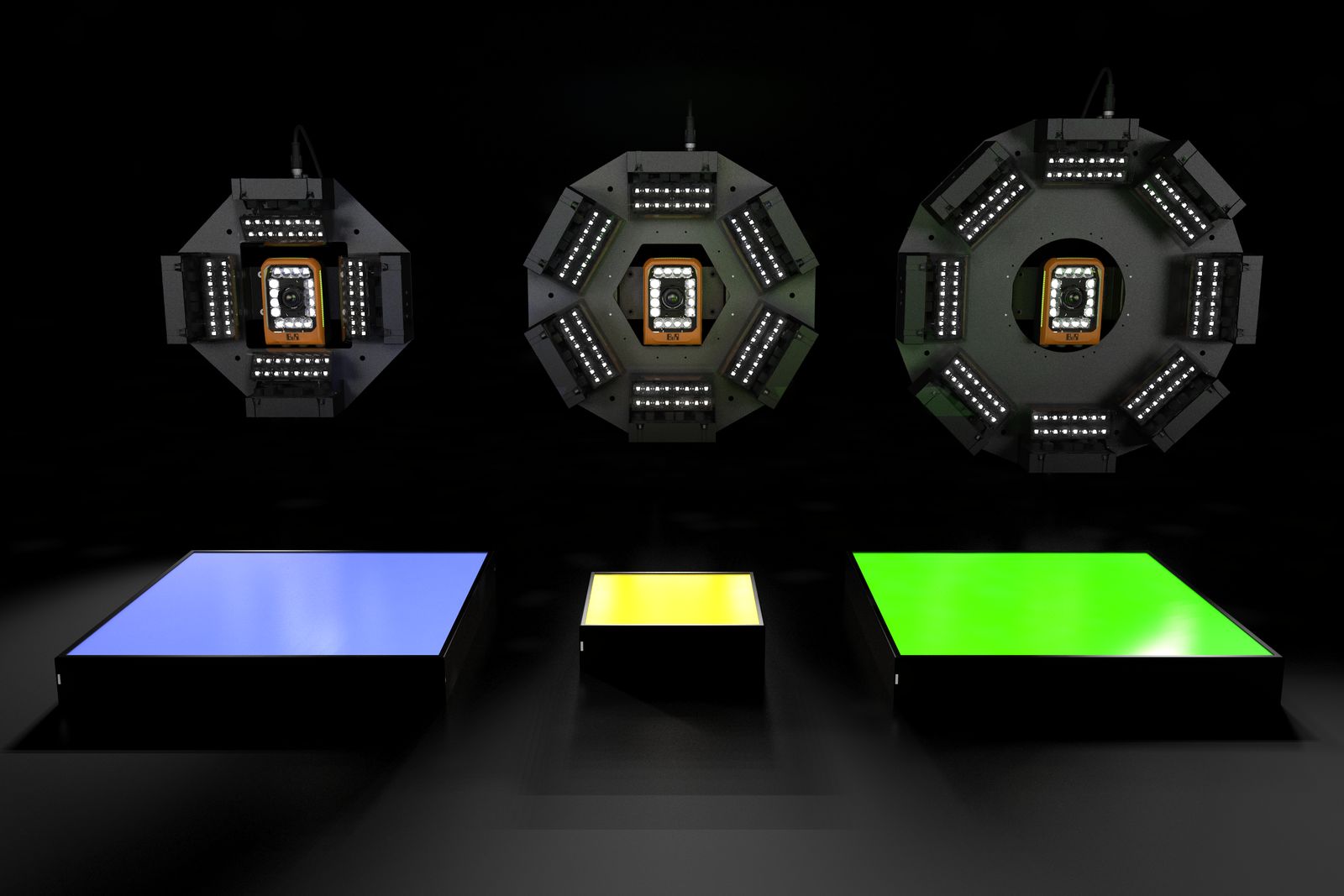
"Lighting is a key element of any machine vision system," clarifies B&R's machine vision expert, Andreas Waldl. It's the lighting that determines if and how the camera sees the targeted object. In addition to the intensity, angle and wavelength of the beam, two factors that make all the difference are precise timing and intelligent control.
In the real world, however, the potential for synchronization is severely limited. "The vision sensors, lighting, strobe controller and machine controller each come from a different supplier," explains Waldl. Without a common communication protocol, all the data exchanged between these devices has to pass through digital inputs and outputs.
Tight synchronization
This introduces a variety of delays and sources of imprecision. Timing the strobe to fire at the exact microsecond the camera opens its aperture, for instance, is simply impossible. "As an engineer, all you can do is extend the duration of the strobe pulse to ensure that it's on while the camera is exposing," says Waldl. Doing so shortens the lifespan of the LEDs dramatically, however.
The engineer could compensate by reducing the intensity of the light, but that would in turn require a longer exposure. In high-speed applications, a longer exposure can easily result in blurry images. The other option would be to amplify the sensor signal. "Doing that adds noise and lowers the quality of the captured image," Waldl points out. "It's really a catch-22."
In B&R's machine vision solution, the camera, strobe controller and lights are all part of the same system. This has some decisive advantages. Since the lighting control and automation system are synchronized with sub-microsecond precision, the light pulses can be extremely short. This extends the life of the LEDs while still ensuring razor sharp images of even the fastest moving objects. The illumination coverage is also extremely uniform and highly reproducible. Quality is increased across the board.
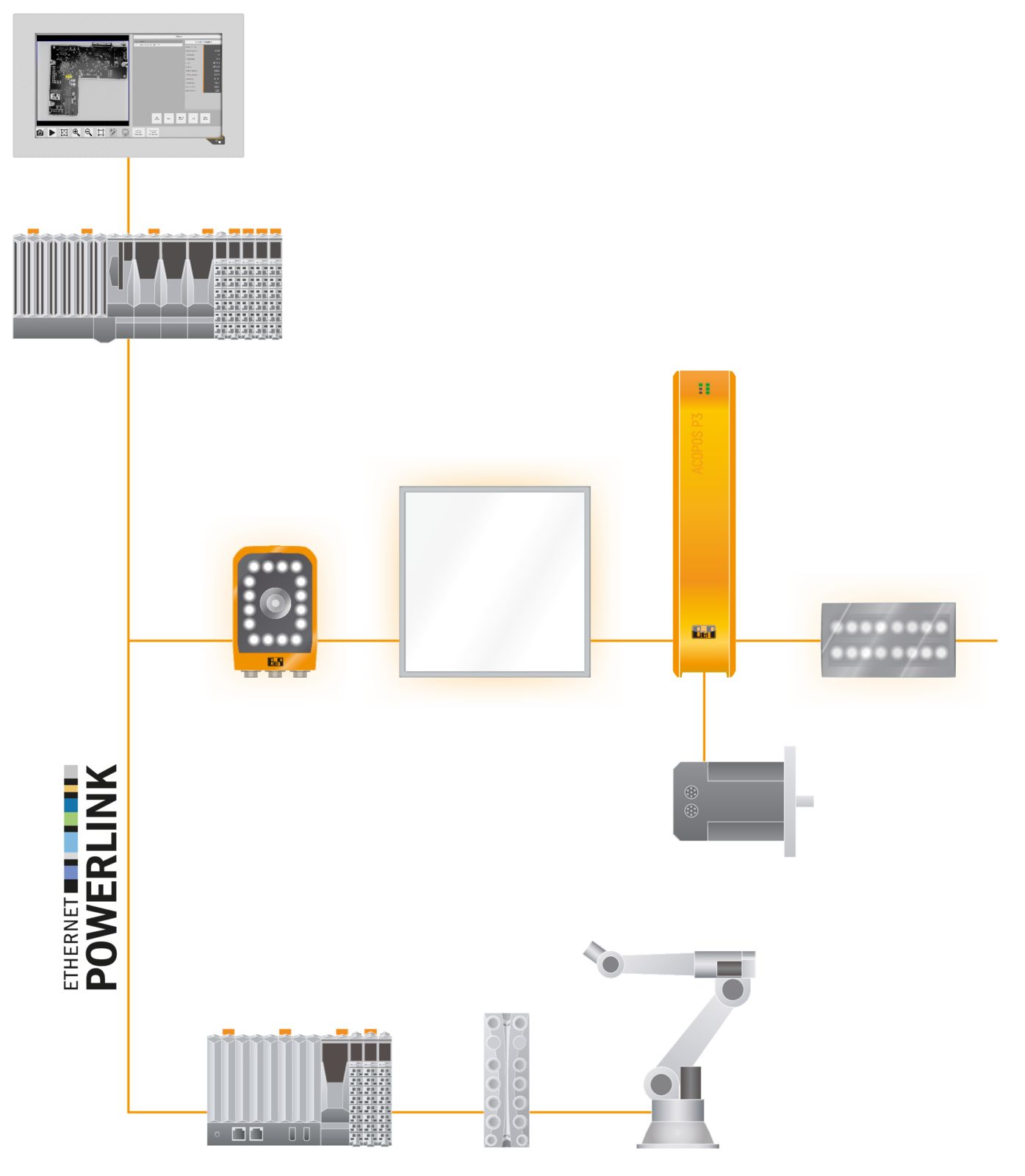
High intensity
"The extremely short strobe pulse allows us to operate the LEDs at up to 300% of their rated current," notes Waldl. B&R is able to achieve a level of intensity that would be impossible with conventional continuous lighting. The enables very short exposure times and reduces noise while at the same time making the solution virtually immune to the effects of extraneous light.
"Machines stand in production halls, where the lighting conditions are difficult and change over the course of the day," says Waldl, "so extraneous light is a notorious source of problems." Eliminating that factor can substantially improve the quality of measurement and inspection results. The machine builder can achieve that either by encasing the machine in a bulky, costly housing – or by using high-intensity strobe lighting.

Uniform illumination
For a machine vision application to produce consistent results, objects must be illuminated as uniformly as possible. This can be achieved through intelligently designed lights. Each LED in the B&R solution has a special lens to ensure that the light is radiated evenly. The lights are factory calibrated by B&R, so there's no need to perform manual calibration in the field or during series production. Temperature fluctuations and the passage of time affect the intensity of light generated by an LED – but B&R's intelligent lights compensate for these effects automatically.
Flexible application
"A machine vision solution that can do one specific thing really well is simply not enough," emphasizes Waldl. In the age of Industry 4.0 and the Industrial IoT, on-the-fly product changeovers are becoming an everyday occurrence – and a vision solution must be able to accommodate that. B&R's fully integrated solution adapts with ease: all the parameters can be stored in recipes and recalled as needed.
At any time, the user can adjust the color of the lights, the duration or focal length of the strobe pulses, the exposure time of the camera or the angle of the light bars – simply by changing a few software settings. With the same lighting components, they can implement both bright-field and dark-field illumination simply by using different parameters.

The significance of color
"Many machine builders underestimate the potential of using different flash colors," notes Waldl. The choice of color can either highlight or hide specific product features or registration marks, for example. That's why B&R offers each of its lighting products – even the camera-integrated LEDs – with up to four different colors, including infrared and ultraviolet.
With different LED colors, it's possible to take multiple photos of a product under different lighting conditions to capture a variety of features. And they can be taken in such rapid sequence that only a single camera is needed.
Configuring instead of programming
"By the way," adds Waldl, "setting up a machine vision system no longer requires any real programming in the traditional sense." B&R has developed ready-made software components that enable users to set up their application via drag and drop. The machine vision software components can simply be linked to other components that implement things like motion control, user management, recipe management and alarm systems. Since they are an integral part of the machine network, comprehensive diagnostics are available in real time. B&R has drastically reduced the development overhead involved in creating a machine vision application.
Author: Stefan Hensel, Corporate Communications Editor, B&R
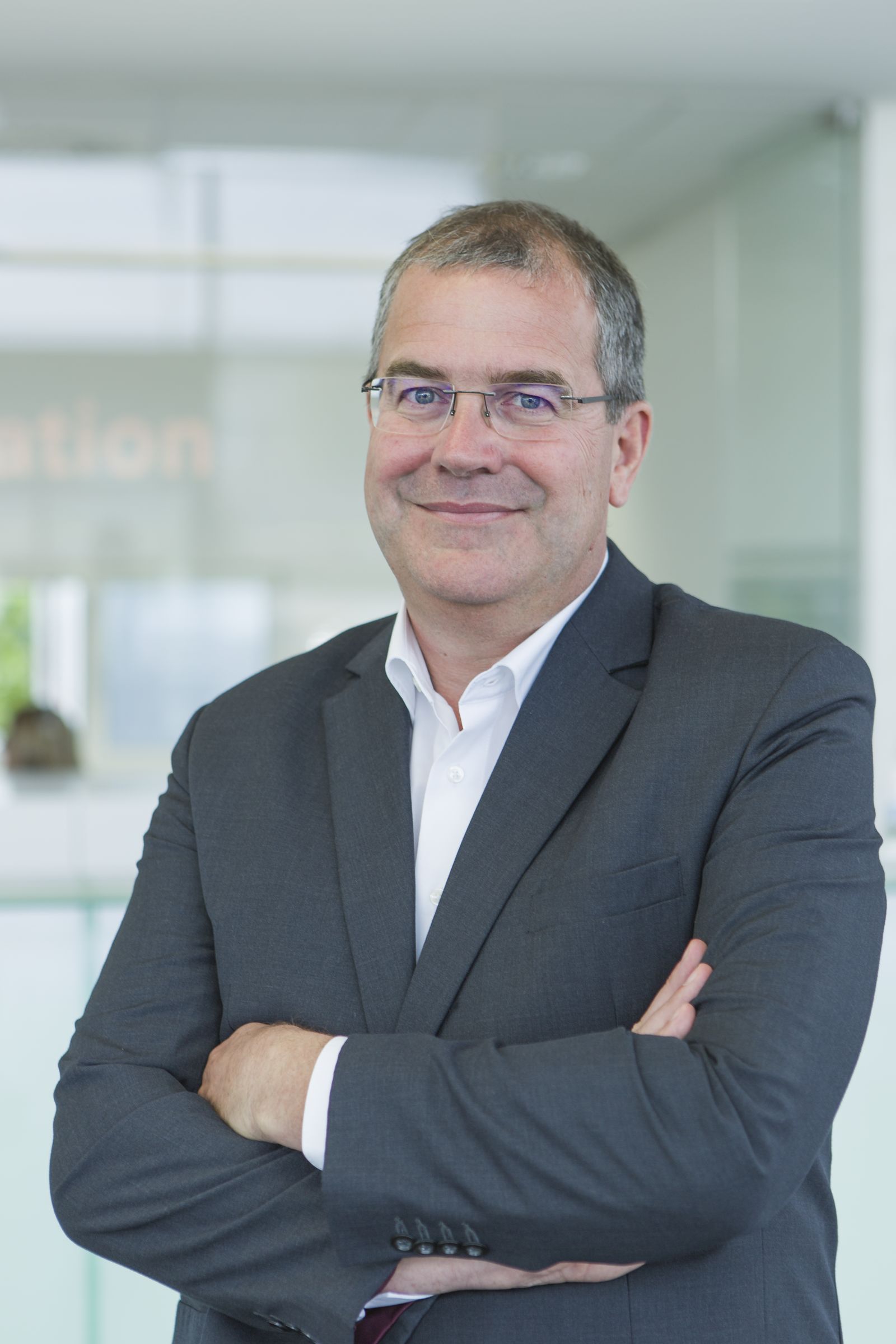
Andreas Waldl, Product Manager - Integrated Machine Vision, B&R
The B&R lighting portfolio
B&R's lighting portfolio includes flexible light bars, light rings and backlights. Cameras are available with up to 64 integrated LEDs. Each light has an integrated strobe controller and can feature up to four different LED colors at a time. The selection ranges from white and various visible colors to infrared and ultraviolet. This makes it possible to achieve just the right contrast, color, illumination and intensity for any application.
B&R's flexible light bars feature electronic angle adjustment from -40° to 90°. The light bars are also available as pre-assembled ring lights in groups of four, six or eight. Integrated into the machine network via an M12 hybrid connector, which also supplies the necessary 24 VDC power, B&R lighting systems each need only a single cable. A second hybrid connection enables daisy-chain cabling with additional lights or cameras.