From printing and packaging to woodworking and wastewater treatment – nearly every industry relies on the power of blown air and suction to perform key technological functions. As diverse as the potential uses for moving air are the requirements placed on the vacuum pumps and compressors that move it. How well these supply systems match the needs of their users determines not only the stability of the process and the quality of the end product, but also important factors like energy efficiency and customer satisfaction. These challenges are no problem for Becker, whose scalable VARIAIR Controller+ features a new standardized BECKER control panel based on B&R technology.
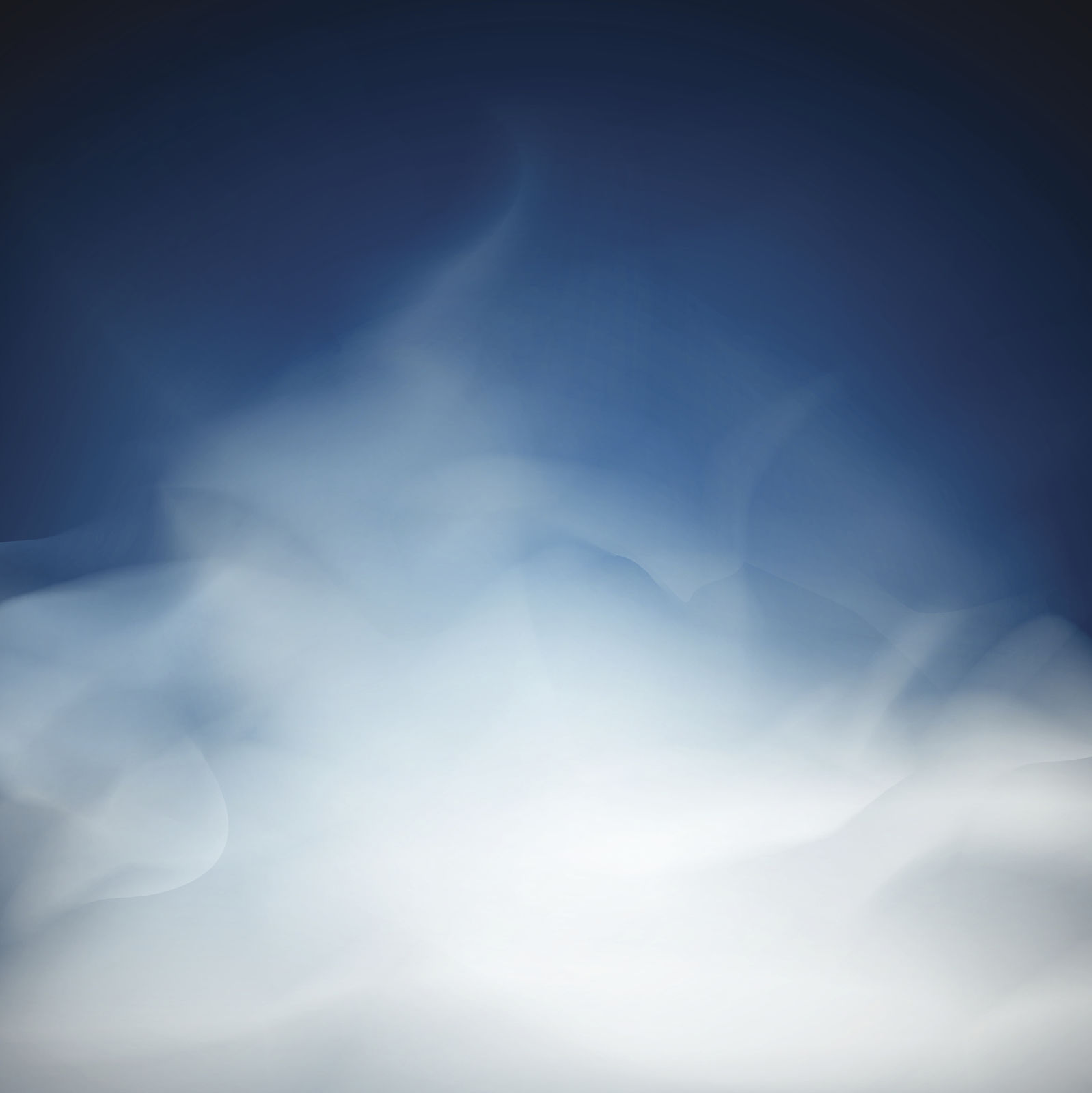
Energy costs are a cost driver for most manufacturing companies. This is in large part due to the units that supply suction and blown air to various steps throughout the packaging process – from handling to vacuum packing. Although modern compressors are relatively energy efficient, the sheer number of individual units and lack of coordination between them are responsible for the high energy consumption.
Intelligent systems for high energy efficiency
Well aware of this problem, Becker has over 800 employees worldwide working to create custom tailored solutions for energy-efficient compressors and air supply systems. These mainly include flow-optimized vacuum pumps as displacement and flow machines. "The value we offer goes beyond our innovative devices and systems," says Stefan Beierlein, head of product management and marketing at Becker. "What's much more important is that the solutions are perfectly tailored to our customers' needs. These systems can only be energy efficient if they're able to closely follow a constantly changing operating point." Even greater efficiency gains can be achieved when the air supply is coordinated and controlled centrally.
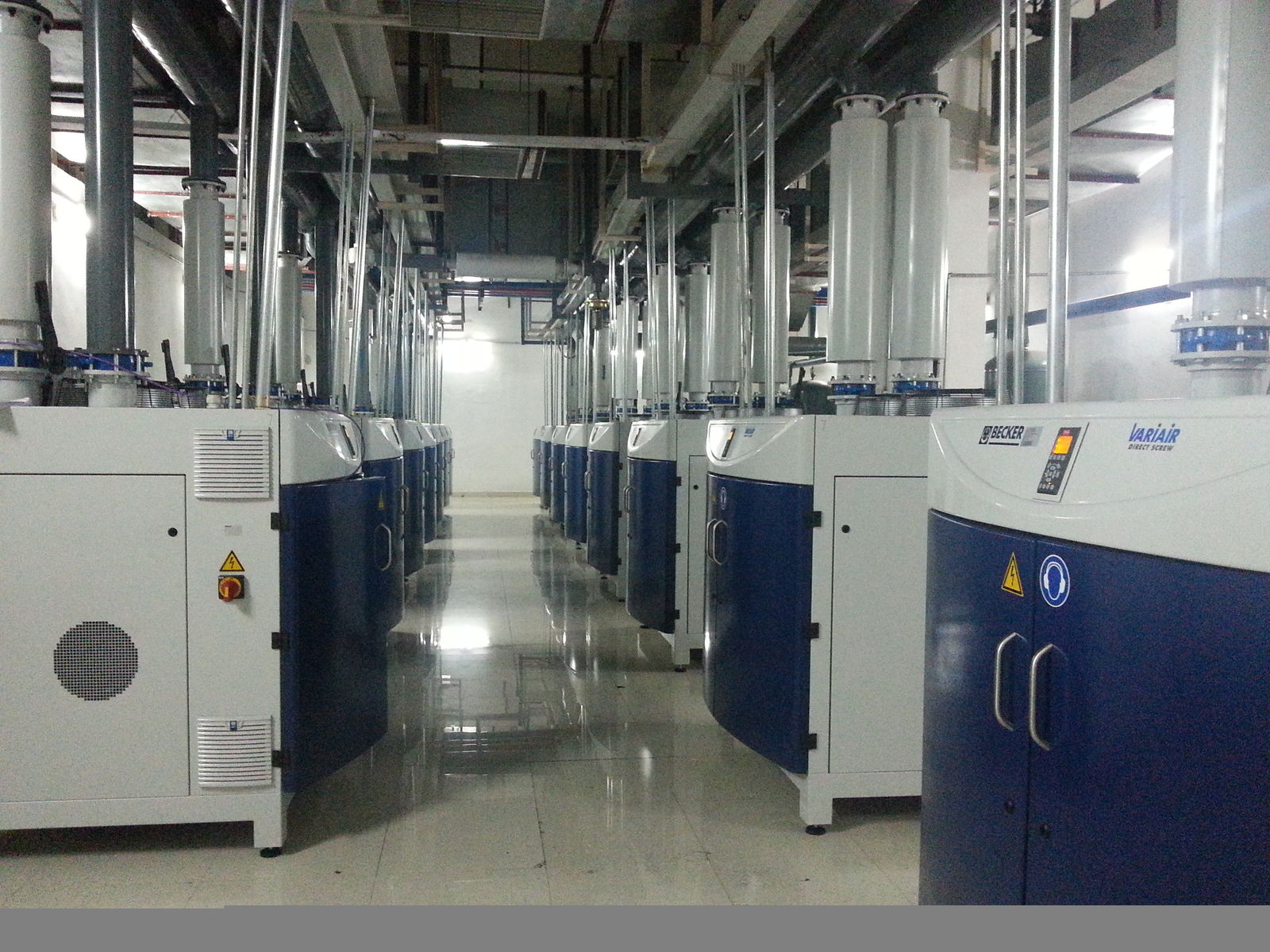
One control software for all devices and systems
To carry out this task and implement new ideas, Becker developers began the search for an automation system that would be future proof and, above all, modular. "Our goal was to cover all possible variants of our system with a single software project. That would give our developers the freedom to work on new functions instead of constantly building new customer software," says Project Manager Ralf Trinler. At the same time, Becker was looking for ways to streamline its entire project workflow – from the initial customer meeting through production, commissioning and service. "We were won over by the B&R system from the outset. The availability of text-based configuration for the application software in B&R Automation Studio would allow us to meet all of our goals," says Trinler.
One hardware unit for control, configuration and simulation
The results speak for themselves. The VARIAIR Controller+ features a Power Panel C70 and a variety of X20 I/O modules and can communicate directly with vacuum pumps and compressors of all sizes. Sophisticated control software from Becker ensures efficient operation, and all relevant data can be backed up.
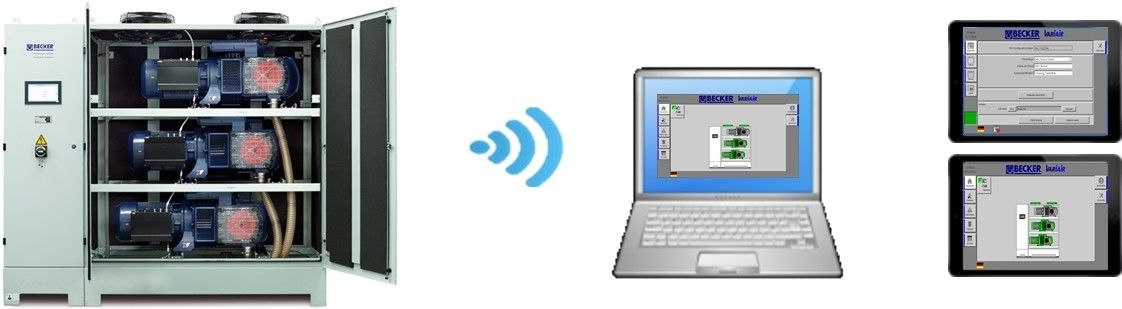
This way, on-site service technicians are always informed of the current configuration and system status. The array of optional interfaces offered by B&R enables direct communication with virtually any customer system. Trinler is particularly proud of another highlight: "Now, when our engineers sit down with the customer to determine their requirements, they are able to configure and simulate a perfectly tailored solution right there on site."
Three HMI applications running in parallel
In order to achieve this, the developers took full advantage of the opportunities for modularization built into the B&R system. In addition to the control program itself, they created separate software modules for configuration and simulation and grouped them all together in one software project. The HMI applications for the three modules can be viewed either on the Power Panel C70 or one of two WLAN-connected tablets. Without leaving the customer's side, the system configuration file and final HMI application can be generated with a few clicks of the mouse. Following this with a simulation gives the customer a live experience of future user interface.
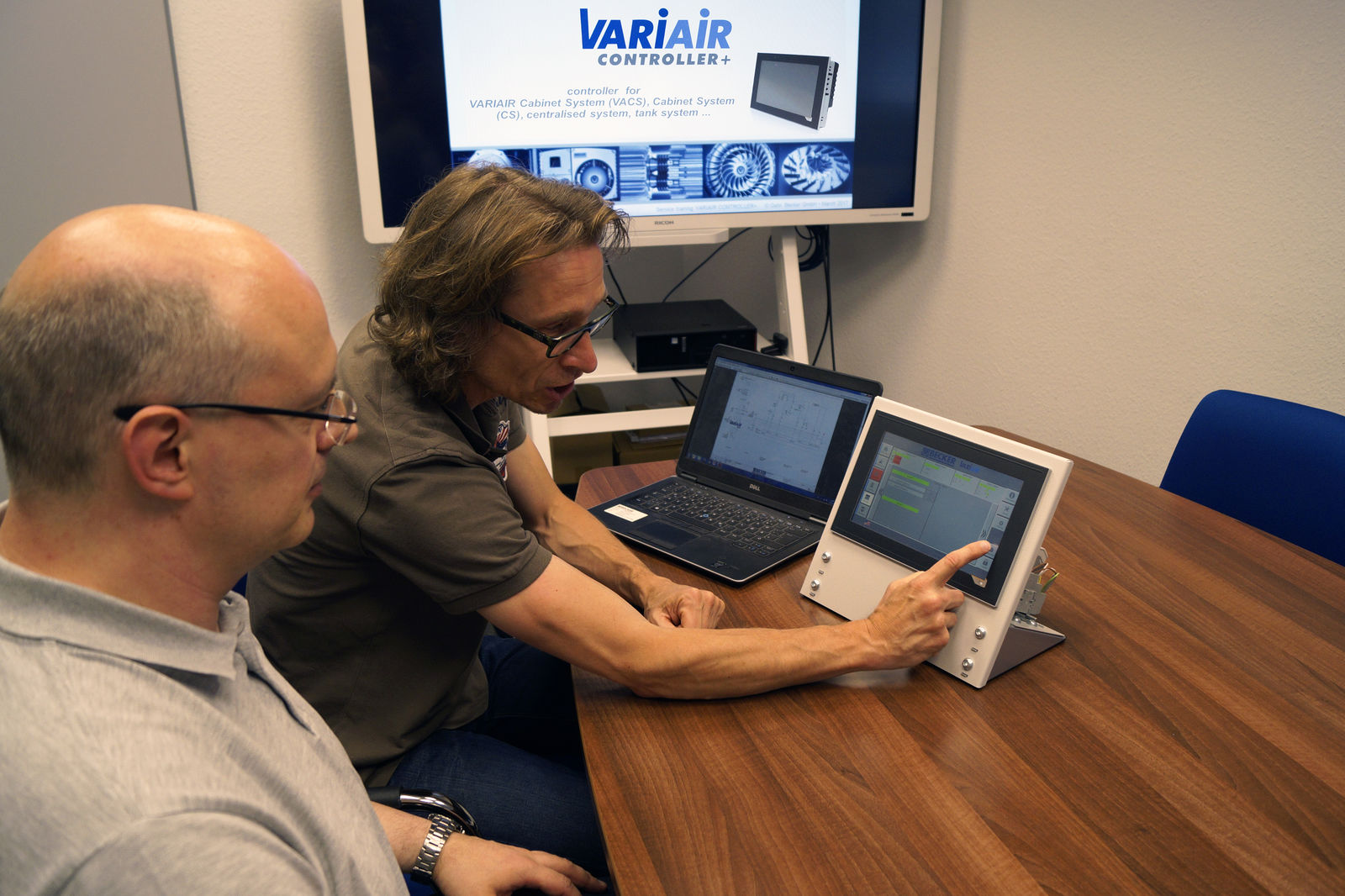
Efficient production through text-based configuration
With the push of a button, the entire system configuration laid out in consultation with the customer is saved in the B&R as a text file. The system configuration file and the main control application are stored on a central server that can be accessed from anywhere in the world. Prior to delivery, the system data is loaded directly from here onto the VARIAIR CONTROLLER+ along with the main control software – without any additional programming. Any adjustments to the system that become necessary later on can be performed by engineers on site without outside assistance, documented and returned to the server.
The company is well equipped for the future. Without any changes to the core software, the Power Panel C70 can easily be replaced by an X20 Compact CPU. In a further stage of development, operation can alternatively be carried out using a wireless tablet. "The interoperability of B&R's hardware and software and their global availability give us all the freedom we need to implement future projects," praises Trinler.
![]() | Stefan Beierlein Head of Product Management & Marketing, Becker "The ability to manage everything in a single software project and perform text-based configuration have given us a major competitive edge in terms of both productivity and customer satisfaction." |