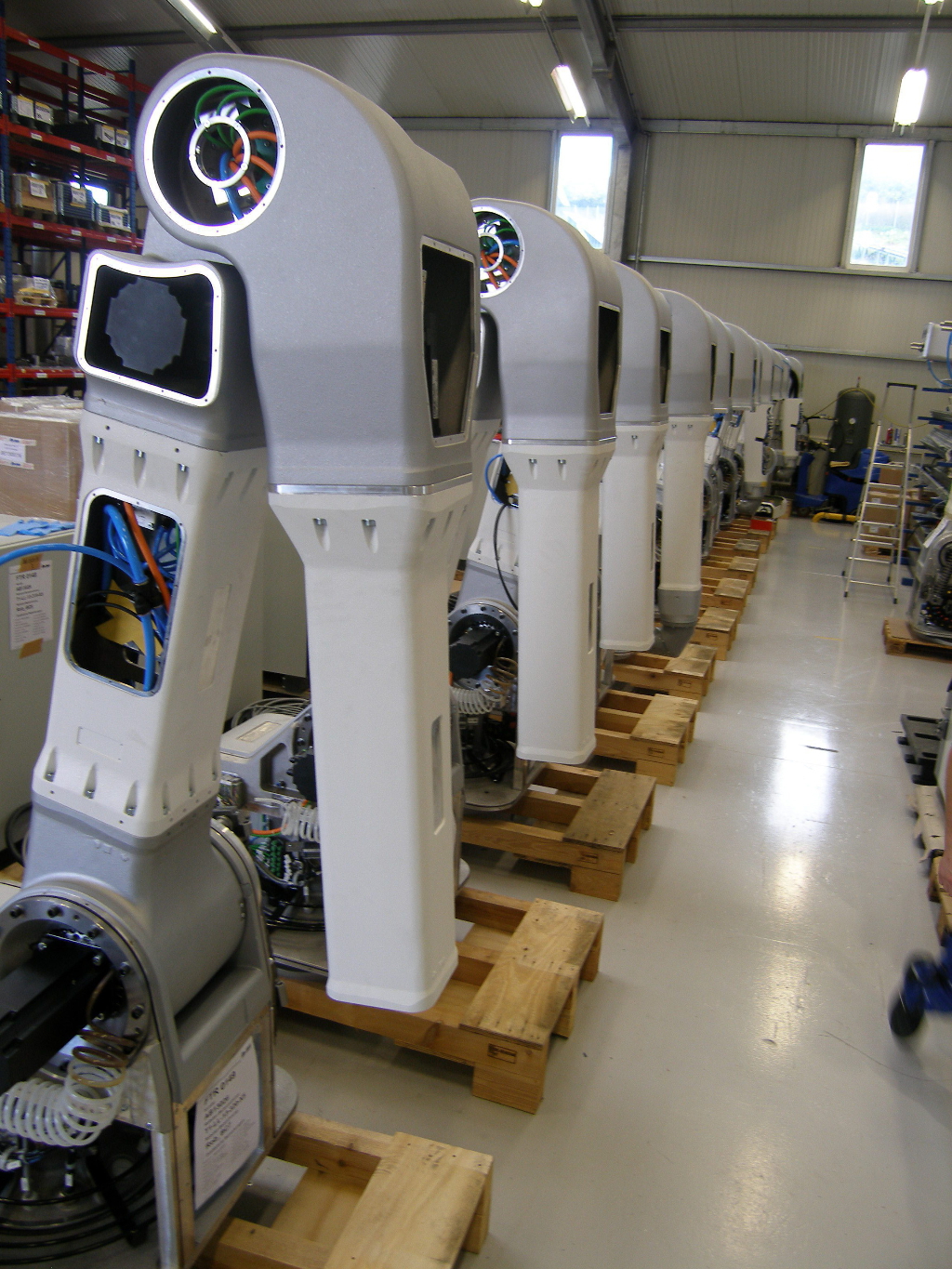
For its newest generation of painting robots, b+m surface systems asked automation partner B&R to help them accelerate the process of getting their custom-built, fully automated painting lines up and running – without compromising on the strictest of safety requirements. The results speak for themselves: Just 18 months into series production, the company had already built and delivered more than 100 robots featuring the new controller.
b+m generally has only 12 months to both design and implement a turnkey painting line. Specializing in painting plastic parts – particularly for the automotive industry and its subcontractors – b+m has one very clear advantage in its hotly contested market. Not only is the company offer full end-to-end solutions, it also controls the entire technology supply chain, enabling it to perfectly tune the components to one another.
The T1 series of b+m's six-axis painting robot plays a central role in this strategy and must therefore live up to some extremely high requirements. "Our robots and handling robots are two different species," emphasizes b+m's head of robotics development. "To achieve the best results, our robots' movements must be rapid, fluid and uniform – at speeds up to two meters per second along a continuous path. On top of all that, they need to be prepared to operate in potentially explosive environments."
Painting robot: Fast and accurate
b+m began development of its 5th robot generation in 2010. Dubbed T1 X5, the new series was designed to serve as a new benchmark in efficiency, flexibility and reliability for years to come. One of the primary goals was therefore to take full advantage of the most advanced closed-loop and motion control available to achieve faster, more consistent path speeds while simultaneously minimizing wear. The new generation presented a perfect opportunity to streamline the control cabinet design by reducing the number of electronic components, with the added benefit of cutting development and commissioning times.
With the heightened safety requirements from DIN ISO 10218:2011 taking effect right at the beginning of the project, these new specifications had to be accounted for when developing the new robot generation.
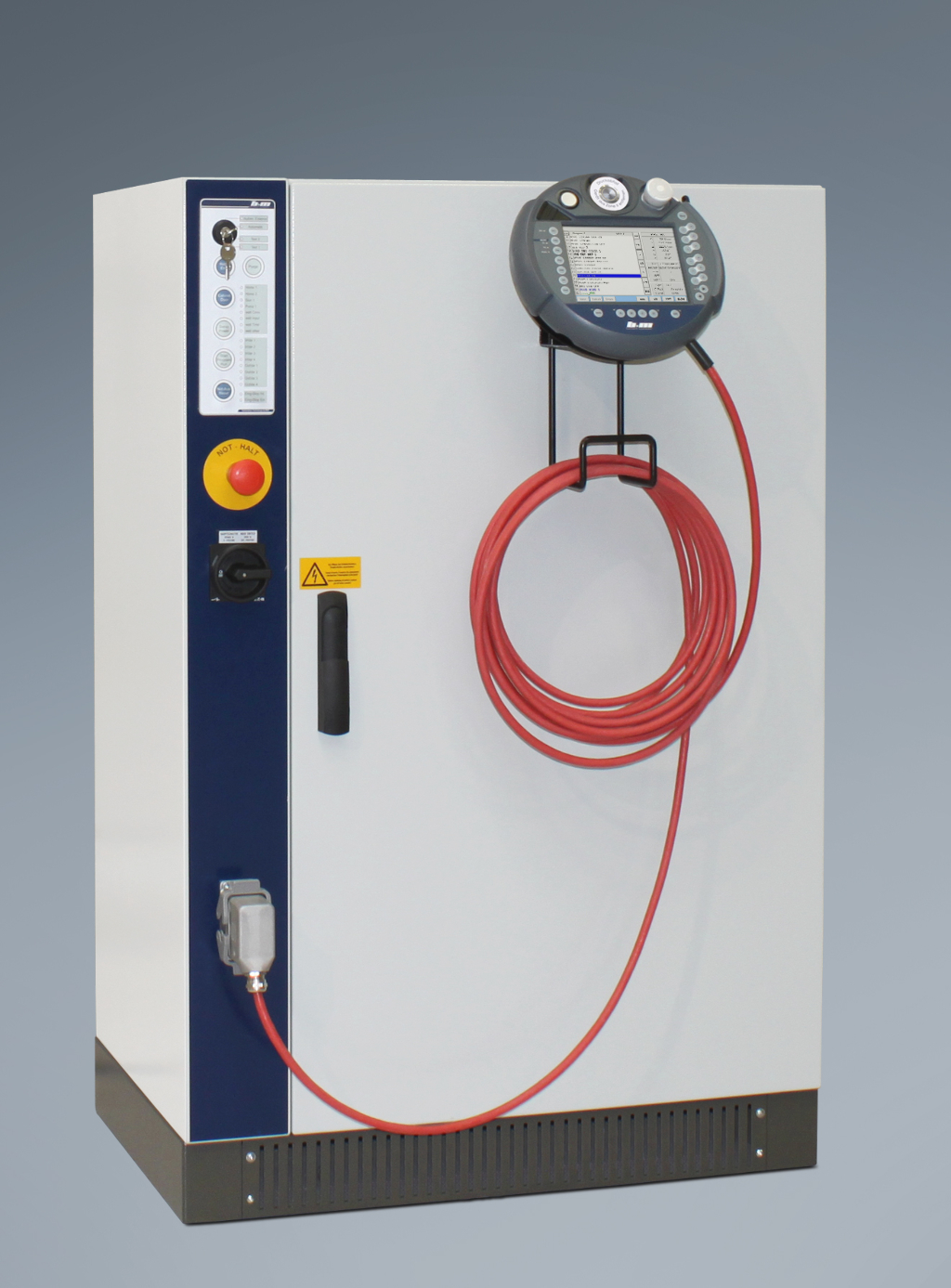
B&R scores big with its safety solution
"If you can master the extensive certification requirements of a safety solution, then a PC-based controller is no problem," reasons b+m's head of robotics development. "That's why we focused our search on suppliers whose portfolio includes safety technology."
By the end of the evaluation, B&R had emerged on top. The full integration of safety technology with the newly available software functions turned out to be the decisive factor.
The first step for b+m was to develop a range of high-speed safety functions based on POWERLINK, openSAFETY and SafeMOTION from B&R. These include integrated motion control functions like Safe Torque Off, Safe Stop 1 and 2, Safely Limited Speed and Safe Maximum Speed, as well as safe monitoring of axis positions. Functions for monitoring the position of the robot and for using safe machine options are also fully integrated in the control application. This allows the machine to be equipped with safety-related add-ons without excessive overhead for programming and recertification.
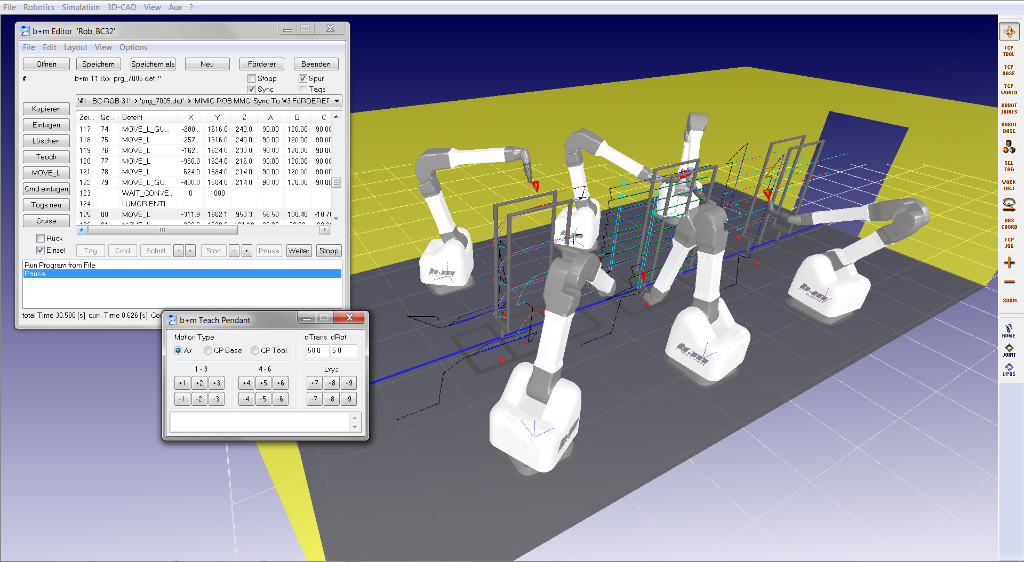
Safely limited speed at the TCP
The second step for b+m was to use the advanced SafeROBOTICS safety functions from B&R to implement safely limited speed at the tool center point (SLS at TCP) as well as a safe serial kinematic chain with safe parameter tables.
"Functionally, we've taken a huge leap forward with B&R's safety technology," says the b+m manager. "With SafeMOTION and POWERLINK, we no longer need a separate safety bus, and installation and commissioning are much faster without all the tedious software configurations."
b+m has reduced both the size and number of components installed in the control cabinet by using two-axis ACOPOSmulti modules with integrated safety functions, which in turn further simplifies installation. The switch to a new cold plate solution has improved cooling performance. The ACOPOS servo drives communicate via POWERLINK with a SafeLOGIC safety controller, an X20 I/O system and the robotics controller – a powerful Automation PC 910.
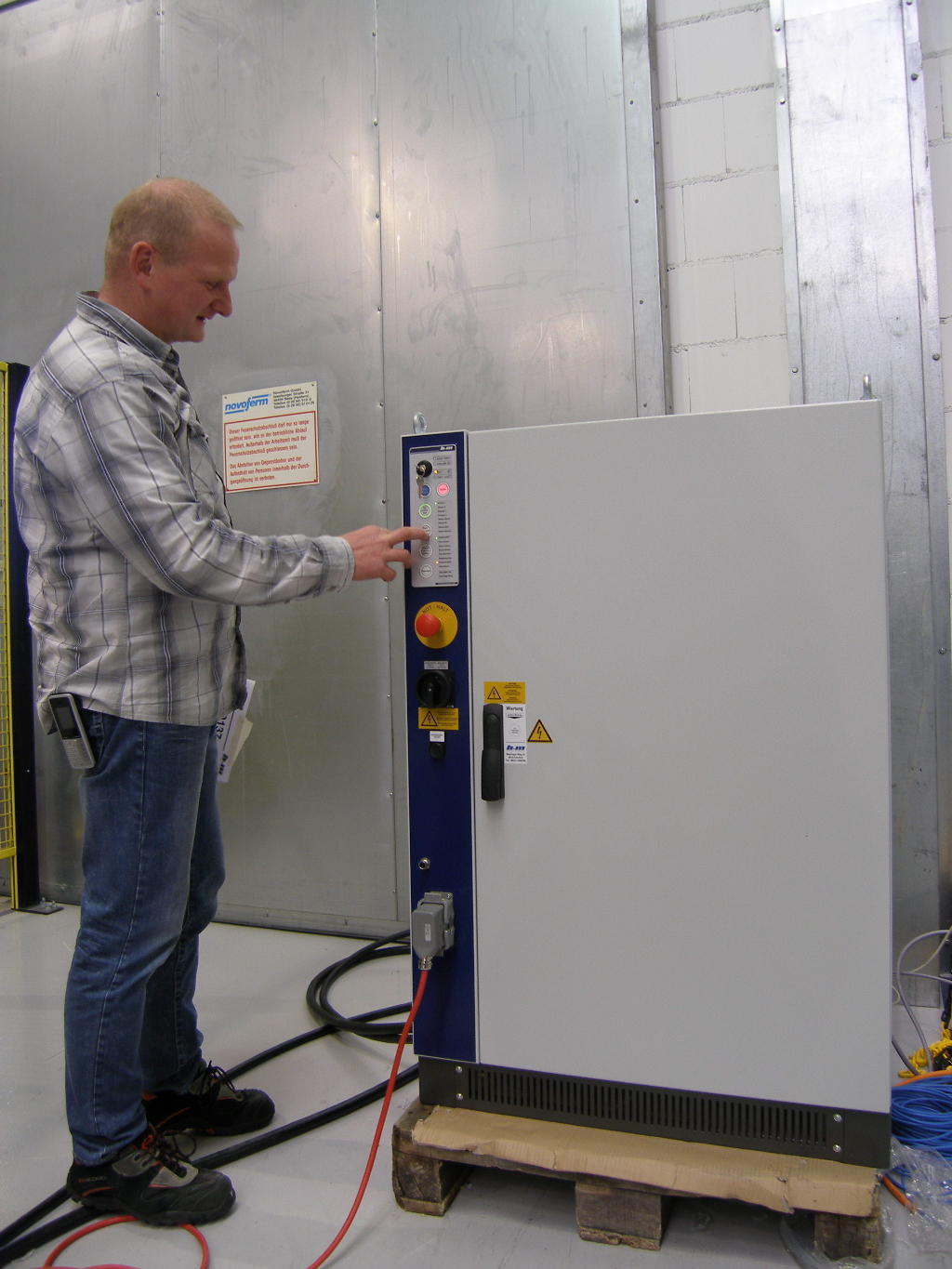
Built according to b+m's specifications, the control cabinet takes up less space and is faster to install and wire thanks to the B&R solution. The reduced number of moving parts and the use of cold plate cooling extended the service life of the system. (Source: Franz Roßmann)
90% of functionality comes from B&R
"With B&R, we've got 90% of our control cabinet functionality covered by one supplier – with no system inconsistencies or interfacing problems. That's a huge win for us," reports b+m's head of robotics development. "We were especially pleased that B&R was also able to provide us with motors for the kinematic chain, an operator panel for the robot and a custom control cabinet keypad with illuminated ring keys and a key switch."
b+m developed the HMI application for the mobile operator panel and the robotics application in-house using Automation Studio. The robotics experts at b+m also programmed the control application themselves using B&R's engineering environment.
B&R developed special robotic safety functions based on the real-time POWERLINK and openSAFETY protocols. b+m used these to equip its 5th generation of painting robots with advanced functions such as safely limited speed at the tool center point (SLS at TCP).
Robotic functions for everyone
"When we first approached B&R, we quickly realized that, while Automation Studio does offer extensive CNC libraries, there were some important robotic functions that weren't completely covered," recalls the b+m robotics specialist. "B&R took this challenge and ran with it, delivering on every aspect of our comprehensive functional specifications." The resulting robotic functions, including transformations and interpolations, are now available to all users of Automation Studio. b+m used them to develop the control application for the painting robot. "We were able to achieve every goal we set for ourselves, and the result is a highly advanced and future-ready generation of robots," concludes the b+m manager. Thanks to the improved mechanical design with more sturdy gearing and the control architecture based on automation and safety technology from B&R, the new generation of T1 robots set new standards in productivity, reliability and service life. In light of the ongoing success of the T1 series, b+m is already working on a new series of robots with the same range of functions but somewhat smaller dimensions. This soon-to-be-released T2 series is specially designed for applications where space is limited and also supports mounting on walls or ceilings. Like the T1 before it, will rely on the proven solutions from B&R.