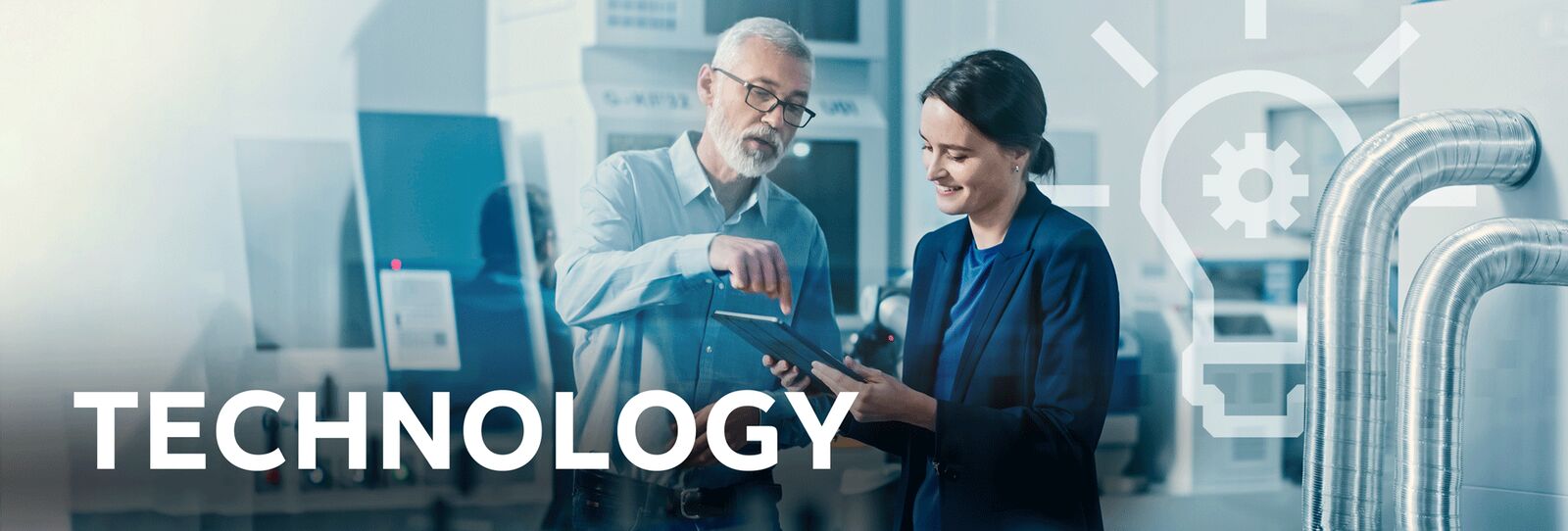
Over the course of the last two decades, it has become hard to keep track of the numerous fieldbus systems that have been developed in the automation industry specifically for purposes of process and factory production control. Yet there remain various restraints that are impeding their performance.
Demand has therefore become more pressing for a reliable communication system that would offer high flexibility and across-the-board compatibility. A new solution in this vein was also expected to allow for ongoing improvements and future upgrades. Ethernet was the first to rise to this challenge: it was a tried and tested technology that was free of patents and widely standardized to boot. Moreover, it had great potential to serve as a consistent, integrated communication solution that could support the interconnection of the control, process and field levels.
Nevertheless, standard Ethernet in combination with an Internet protocol like TCP/IP is unsuitable for data transmission in hard real time. Data traffic can be delayed in unforeseeable ways due to the Carrier Sense Multiple Access/Collision Detection (CSMA/CD) mechanism. An integral part of the Ethernet standard IEEE 802.3, this mechanism helps prevent data collisions on the bus that can occur in Ethernet environments due to the particular nature of Ethernet transmissions.
In order to develop Ethernet-based, but real-time capable fieldbuses, manufacturers have pursued various approaches in their efforts to eliminate such delays. These solutions are commonly referred to as “real-time industrial Ethernet” technologies.
POWERLINK has become one of the most successful real-time industrial Ethernet systems in the world today.
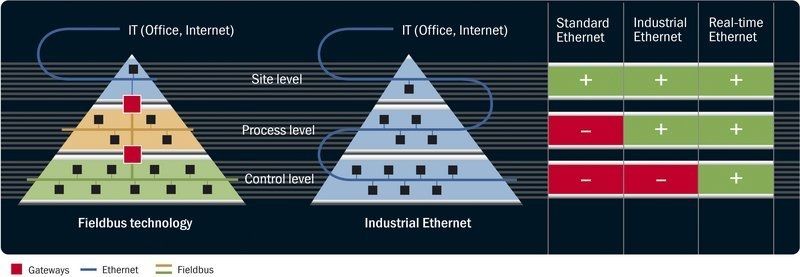
Technology in deep
By combining Ethernet, CANopen and hard real-time capabilities, POWERLINK integrates features and abilities from three different worlds. In contrast to a number of competing products, POWERLINK has remained extremely close to the Ethernet standard, retaining original Ethernet features and so reducing the cost of deployment in industrial environments. The protocol's second major advantage is the integration of CANopen technology, a robust and proven protocol widely used throughout the field of automation whose extensive standardization greatly simplifies network configuration. The third pillar of POWERLINK's success rests on technologies developed by the EPSG, especially the POWERLINK stack, the feature that provides the protocol's real-time capabilities.
Leading PLC and component manufacturers have teamed up in the EPSG to work collectively on technological projects that generate considerable added value for the community at large. This "Technology" section will highlight some of POWERLINK's greatest assets – the features and functions that make up the core of POWERLINK technology.