Flexible. Integrated. Comprehensive.
mapp CNC simplifies the implementation of CNC axes in manufacturing systems, making CNC applications easier to create and deploy. Developers can draw from a wide range of tools for all types of CNC kinematics:
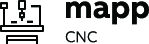
Increase your productivity

Reduce your costs
mapp CNC works with standard automation hardware. You can control multiple CNC axis groups using a single PLC.

Unite CNC and machine control
mapp CNC fully integrates CNC applications into the machine control system – including synchronization with microsecond precision.

Integrate your know-how
mapp CNC can be combined with programs written in C/C++, IEC 61131 languages, G-code and user-defined commands.

CNC programming has never been so easy
The preconfigured components of mapp CNC make implementing CNC technology easier than ever before.
mapp CNC - Added value for your machine
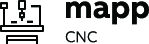
CNC library
The CNC library makes it easier than ever to develop CNC machines. Templates for CNC systems with up to six linear or orientation axes (plus additional axes) allow you to configure countless machine variants with the ease of drag and drop. And all without writing a single line of code.
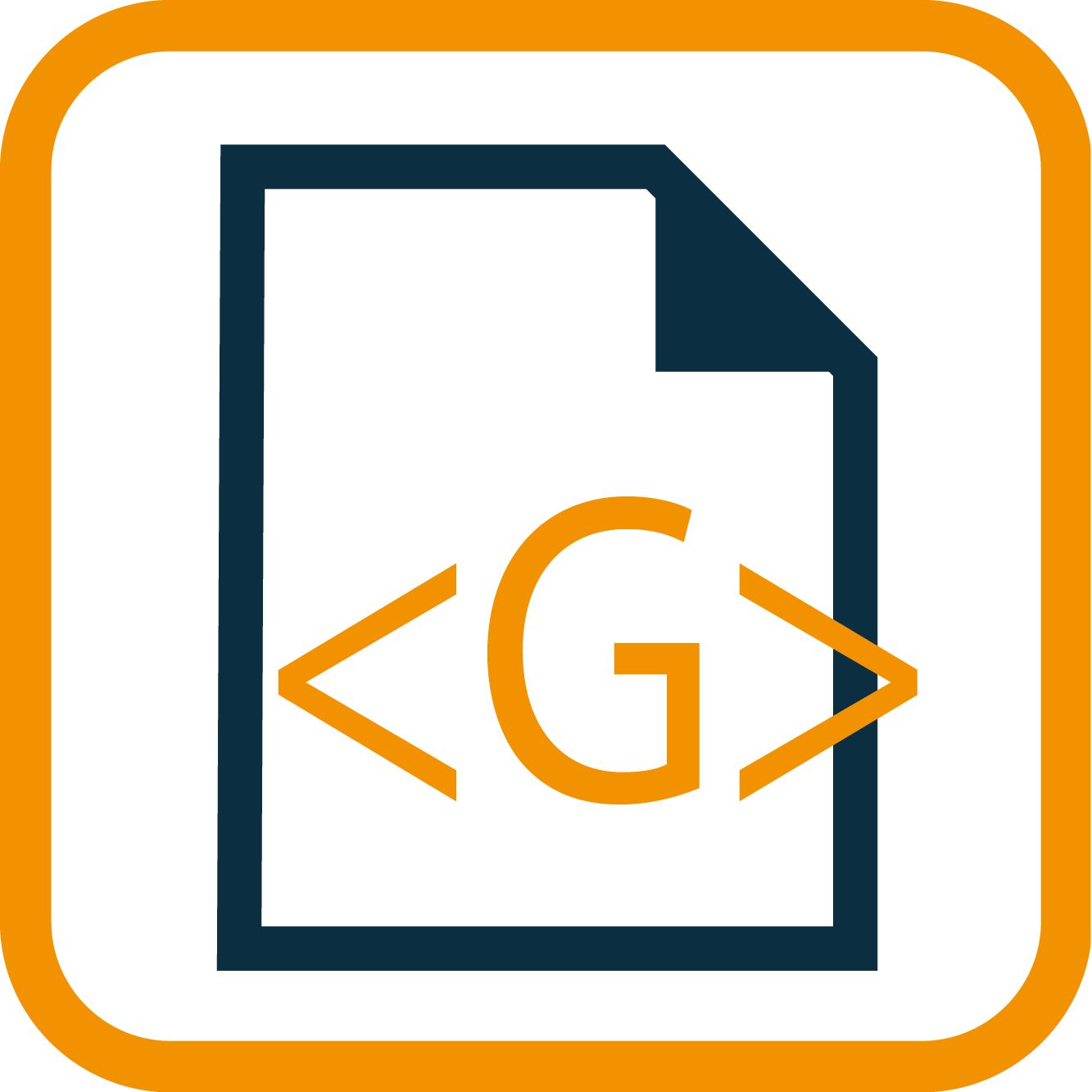
CNC programs
The enormous range of CNC functionality is easily accessible using G-codes and M-codes (DIN 66025). Thanks to the mapp Motion interpreter, it's also possible to execute programs in Structured Text or user-defined languages. Applications can also be created using PLCopen Part 1 / PLCopen Part 4 interfaces in all IEC 61131 languages as well as C and C++. Even programs generated automatically from CAD/CAM systems can be easily integrated.
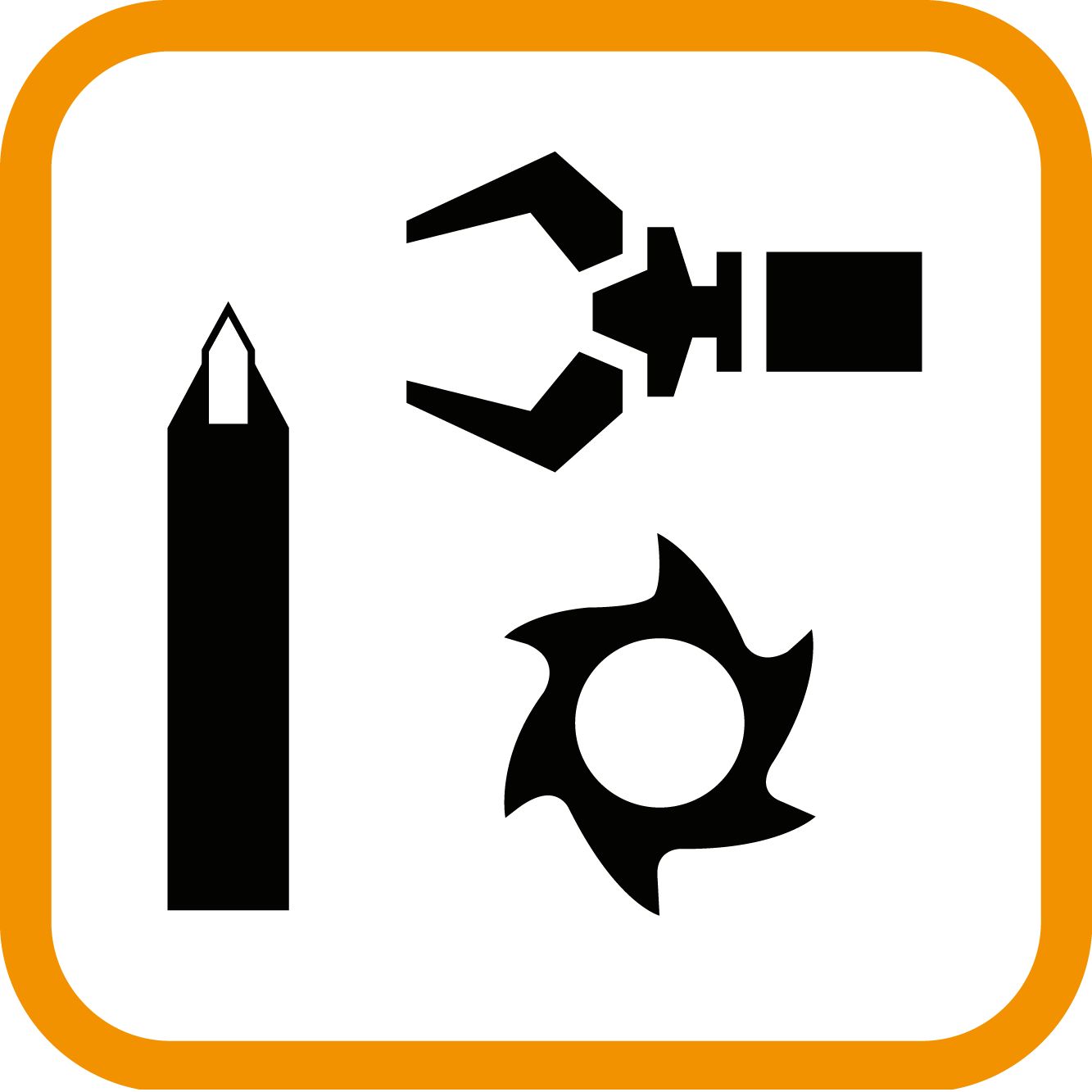
Tools
The tools function makes it easier than ever to use and manage tools. Tool dimensions and orientation can be stored and recalled when switching tools. New tools can even be added at runtime. Tool data is used for path planning and for kinematic transformation of the tool center point (TCP).
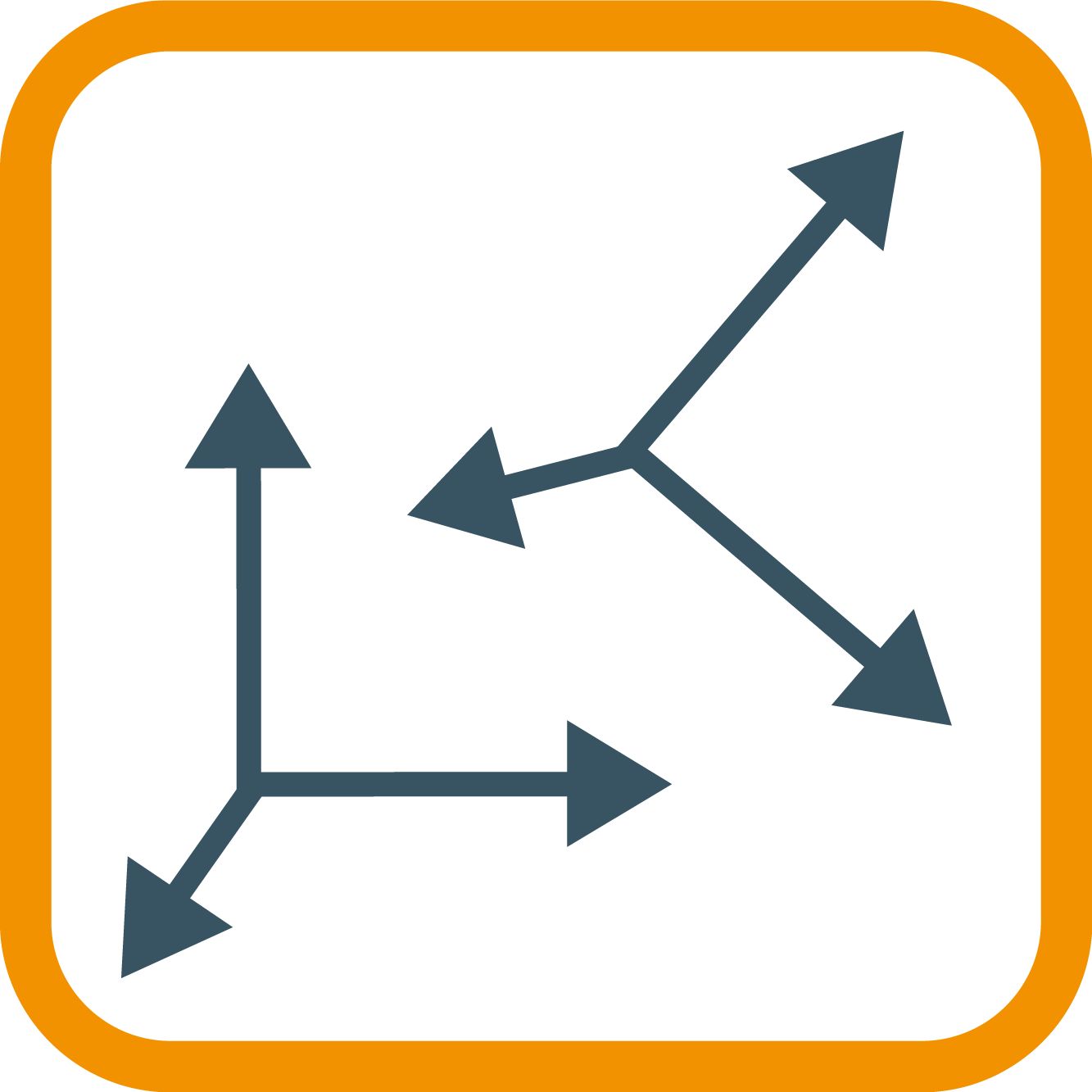
Frames
Frames are used to define the position and orientation of coordinate systems in Cartesian space. The data can be predefined in tables or configured at runtime. This allows you to set and adjust the positioning of the machine and workpiece. Movements can be programmed relative to a processing station or tool changer.
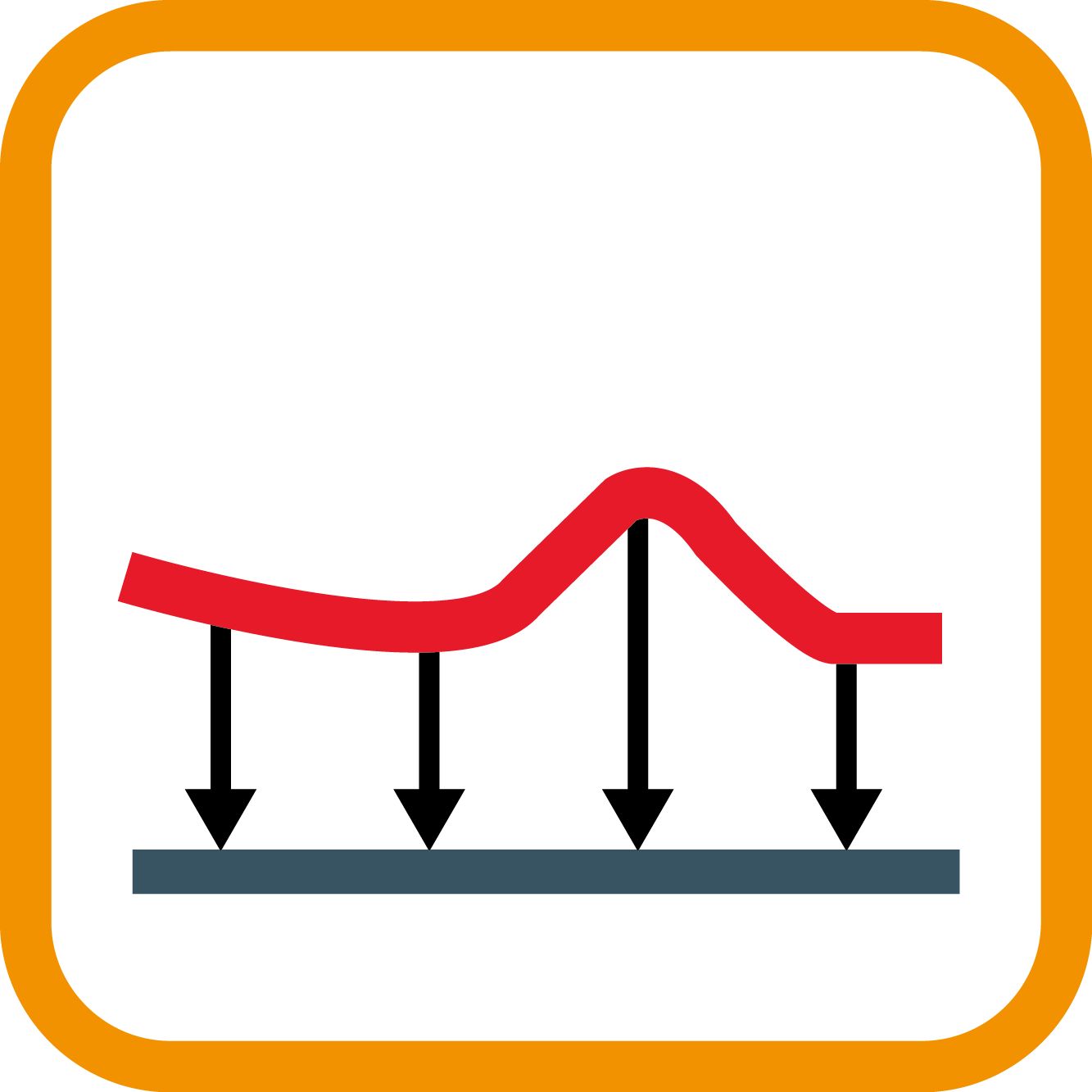
Geometric compensation
Geometric compensation can be used to account for sources of imprecision on the machine, such as production-related tolerances, misalignments or elastic deformations. Simple configuration options for deviations in two or three dimensions can be used multiple times or in combination to achieve high precision throughout the workspace.
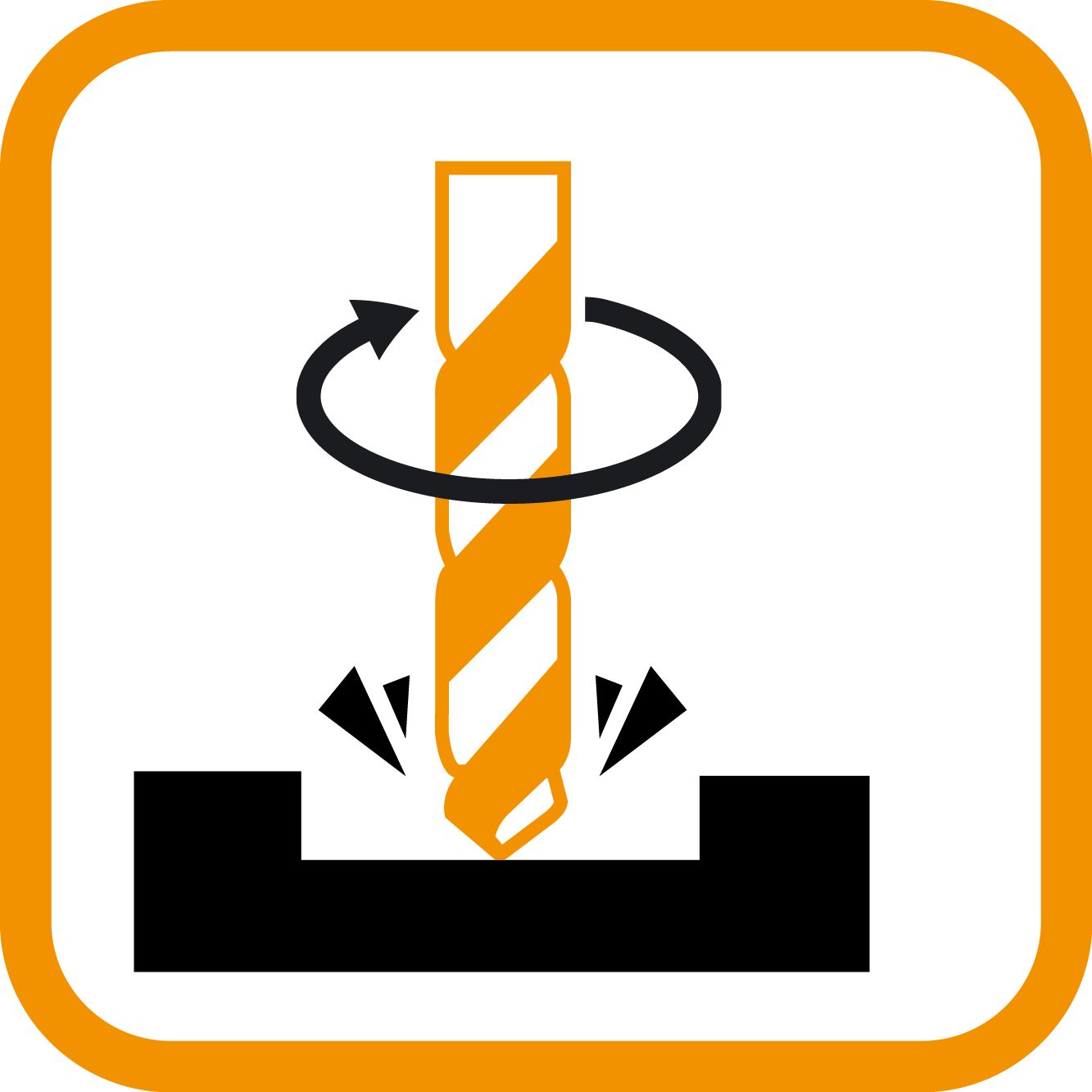
Spindle
mapp CNC provides an integrated spindle controller that makes it easy to implement applications such as turning, drilling or threading. All the necessary functions are integrated, including constant cutting speed and feed per revolution. Positioning tasks can also be implemented using a spindle by seamlessly switching between speed and position control.
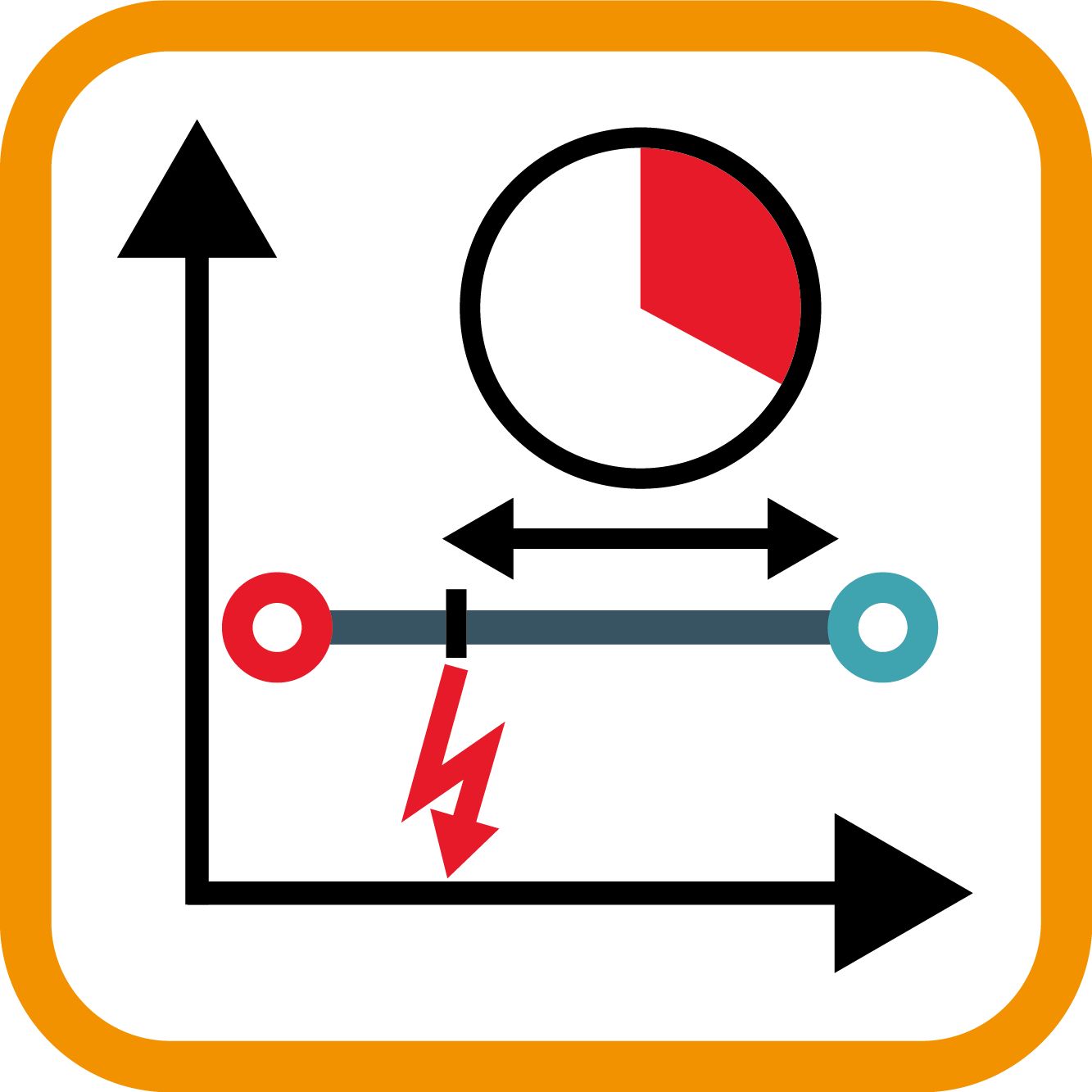
Switching signals
This function can be used to switch signals directly from the running program. This makes it possible to do things like switch lasers on and off with microsecond precision in high-speed applications. The signal position can be defined based on distance or time.
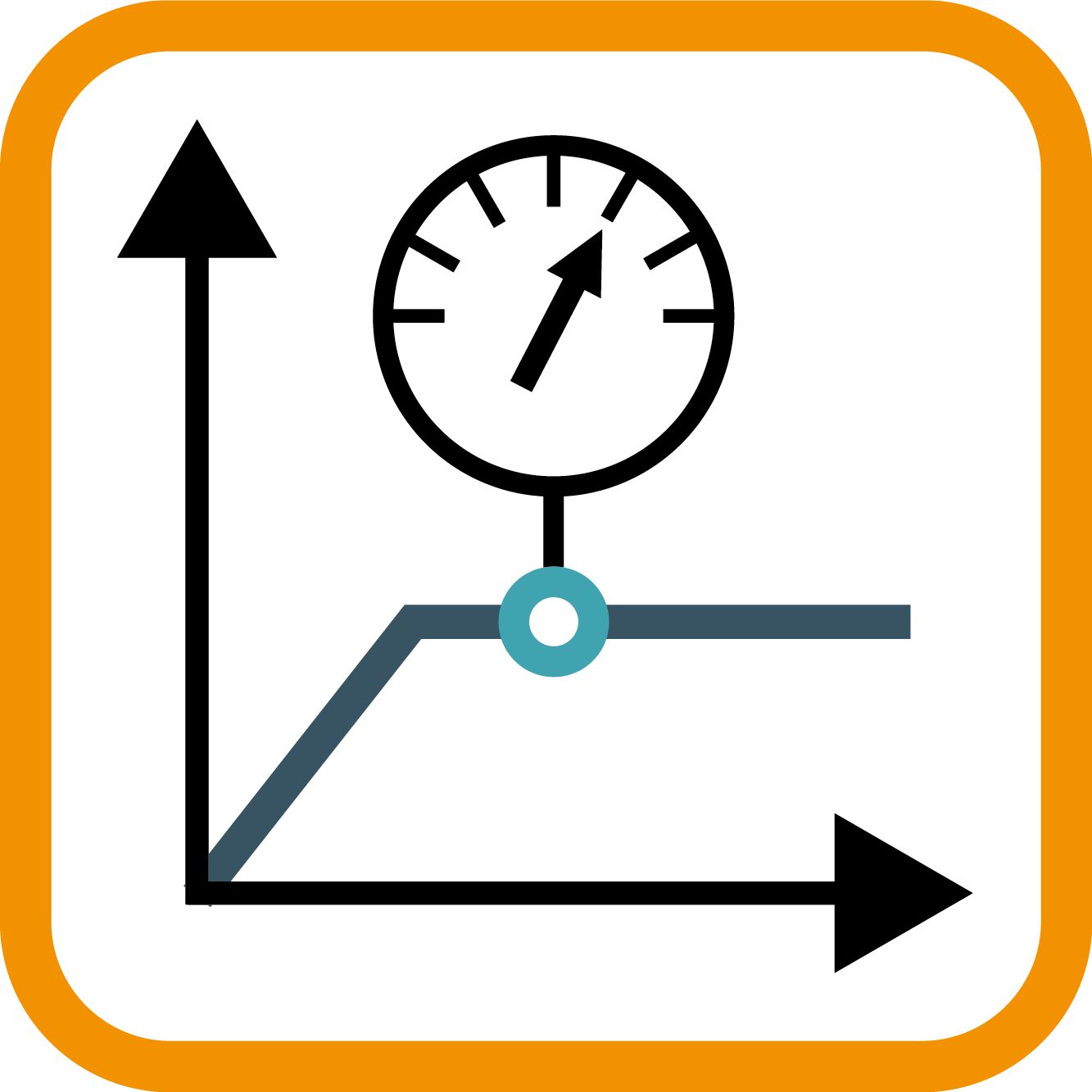
Measurement
The measurement function reads the exact positions of the CNC axes at the time of a trigger signal. This makes it possible to calibrate workpiece positioning and tool dimensions. Path movement can be stopped when a trigger signal occurs.
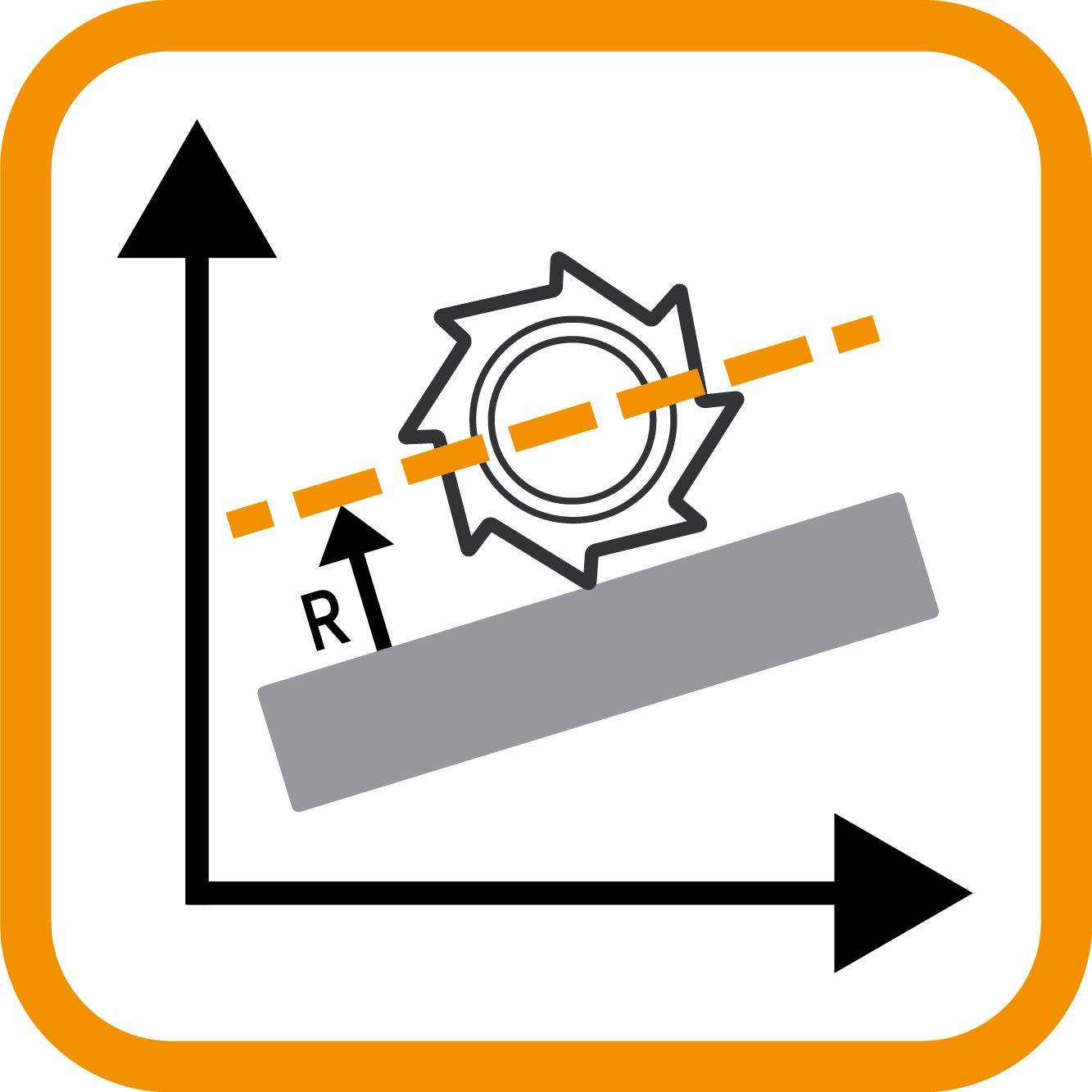
Cutter diameter compensation
Cutter diameter compensation makes it possible to program workpiece contours independently of workpiece geometry. mapp CNC automatically calculates an appropriate path for the current tool – including bottleneck detection. This is a very user-friendly way to implement cutting and milling applications.
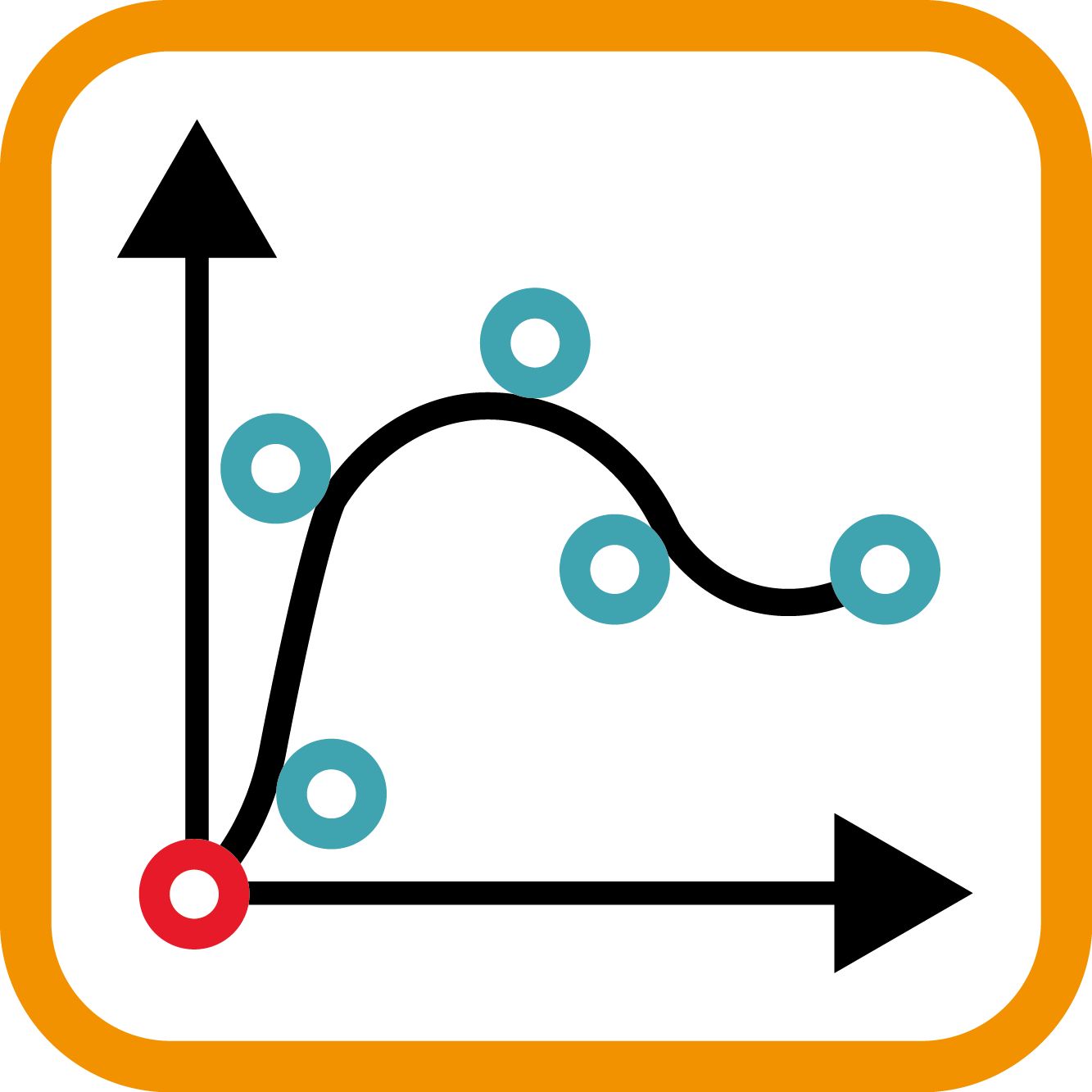
Compressor
The compressor processes successive line segments to create a continuous contour. Data generated from CAD/CAM systems can be transformed into smooth, fast movements for machining free-formed surfaces. Simple configurations allow for a perfect balance between speed and accuracy based on the needs of the application. The result is faster, more efficient processing and reduced wear on the machine.
Usage example:
5-axis milling
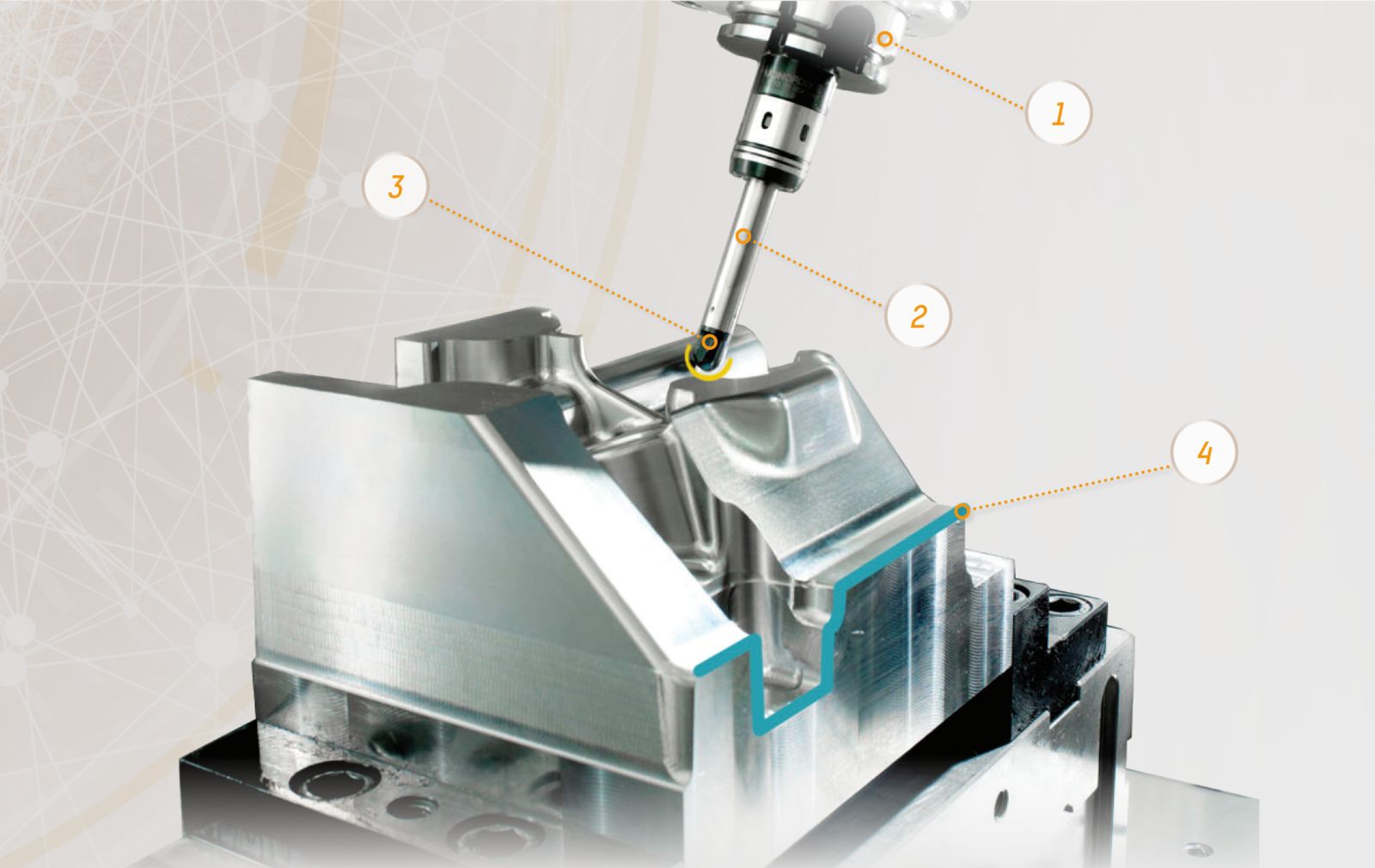
(1) | The rotation of a machining tool is controlled automatically using the Spindle function. |
---|---|
(2) | The Tools function can be used to manage any number of tools. |
(3) | The CNC contour is programmed independently of what tool will be used. The tool radius is accounted for automatically by the Cutter diameter compensation function. |
(4) | Individual path segments, such as those generated by CAD/CAM systems, are smoothed automatically by the Compressor function. |
Sheet metal cutting
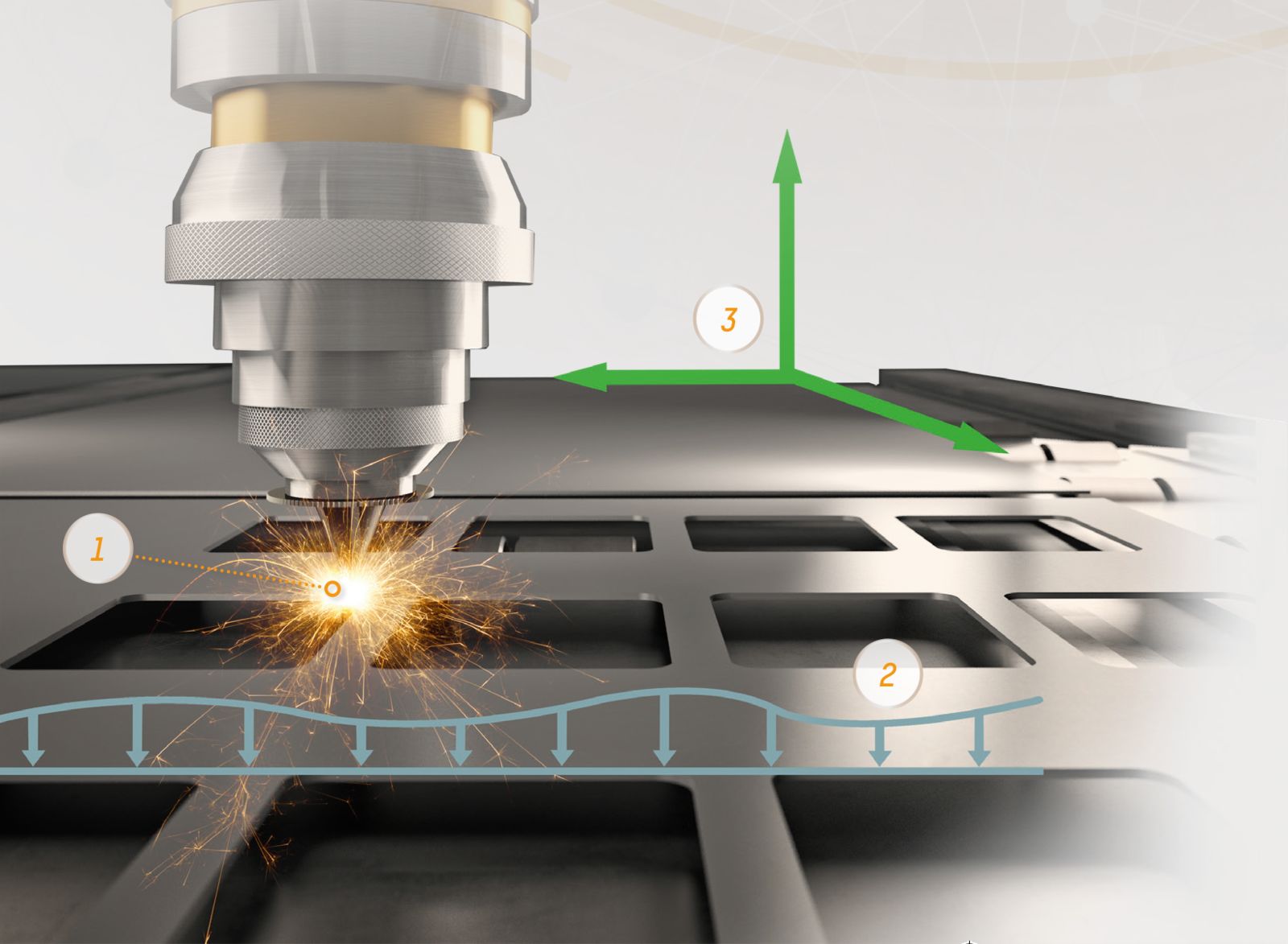
(1) | Lasers can be switched on and off with microsecond accuracy to make highly precise cuts even at high speeds. |
---|---|
(2) | Elastic deformation of machinery or workpieces can be compensated for automatically by the Geometric compensation function. |
(3) | Frames allow you to calculate movements for different coordinate systems relative to one another. Assigning separate coordinate systems to the workpiece carrier and CNC machine simplifies both programming and workpiece processing. |