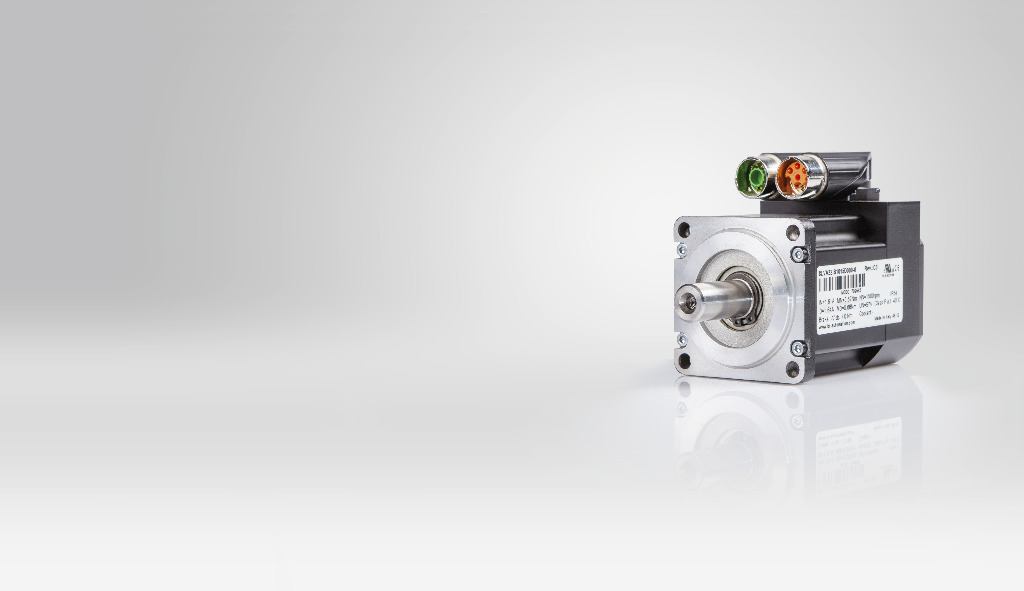
Dynamische Kompaktantriebe
The most modern machine concepts demand excellent dynamics and performance within the smallest amount of space possible. The 8LV three-phase synchronous motors from B&R were specially developed for this area of application and provide users an extremely high power density for the highest level of support when designing machines.
Standard motors (available at short notice)
8LVA1 (size 1)
8LVA2 (size 2)
8LVA3 (size 3)
Accessori
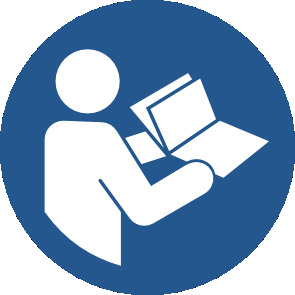
Dokumentation
8LVA - Kompakte Servotechnik
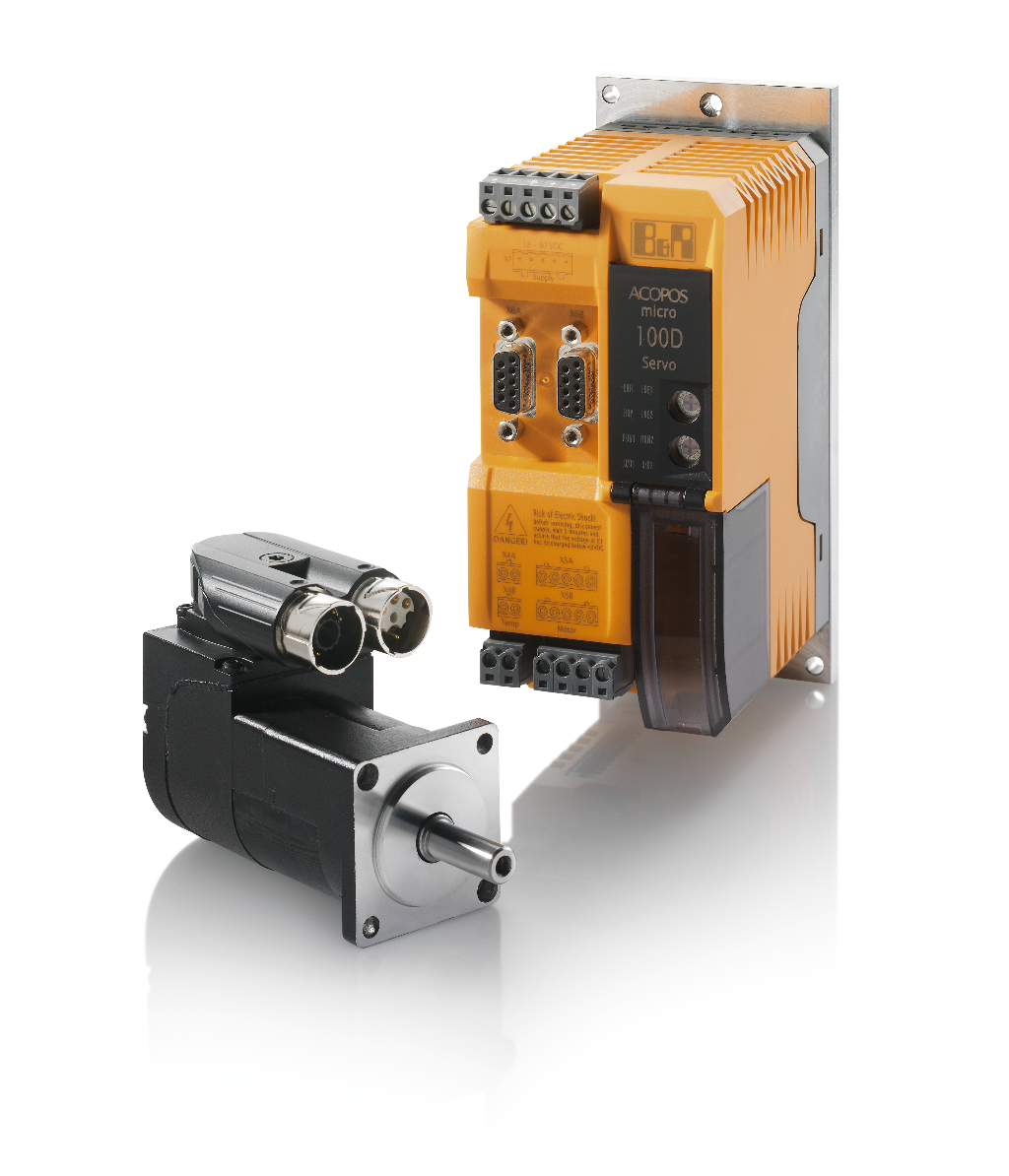
Online-Tools
configuratore CAD Für Motoren und Getriebe. Unsere CAD-Applikation erlaubt Ihnen den Zugriff auf 2D/3D CAD-Daten in verschiedenen Formaten.
Die glatte Oberfläche
Die glatte Oberfläche
Highlights
Highlights
Anschlusstechnik
Anschlusstechnik
Doppel-Winkeleinbaudose
Einkabellösung (hybrid)
Das elektronische Typenschild
Das elektronische Typenschild
Kühlart und Baugrößen
Kühlart und Baugrößen
The 8LV servo motor series is available in three different sizes (1, 2, 3). They have different dimensions (especially flange dimensions) and power ratings. The various sizes can be differentiated by a number (c) in the model number. The larger the number, the larger the flange dimensions and power rating for the respective motor.
The 8LV servo motor series is available in two different lengths. They have different power ratings with identical flange dimensions. The various lengths can be differentiated by a number (d) in the model number.
Length | Available sizes | ||
---|---|---|---|
1 | 2 | 3 | |
2 | --- | Yes | --- |
3 | Yes | Yes | Yes |
Gebertechnik
Gebertechnik
Belastbarkeit des Wellenendes und der Lagerung
Belastbarkeit des Wellenendes und der Lagerung
8LV servo motors are equipped with grooved ball bearings which are sealed on both sides and greased. Radial and axial forces (Fr, Fa) applied to the shaft end during operation and installation must be within the specifications listed below. Bearing elements may not be subjected to shocks or impacts! Incorrect handling will reduce the service life and result in damage to the bearings.
Installation
The axial forces Fa permitted during the installation of pinion gears, couplings, etc. depend on the motor size and can be found in the following table:
Motor size | Permissible axial force Fa [N] |
---|---|
Standard bearing | |
1 | 480 |
2 | 1000 |
3 | 1650 |
Radial force
The radial force Fr on the shaft end is a function of the loads during installation (e.g. belt tension on pulleys) and operation (e.g. load torque on the pinion). The maximum radial force Fr depends on the shaft end type, bearing type, average speed, the position where the radial force is applied and the desired service life of the bearings.
Axial force, shift in shaft position caused by axial force
The axial force Fa on the shaft end is a function of the loads during installation (e.g. stress caused by mounting) and operation (e.g. thrust caused by slanted tooth pinions). The maximum axial force Fa depends on the bearing type and the desired service life of the bearings. The fixed bearing is secured on the A flange (with size 1 the fixed bearing is on the B side flange and the floating bearing is on the A side flange) with a retaining ring. The floating bearing is preloaded on the B flange with a spring in the direction of the A flange. Axial forces in the direction of the B flange can cause the spring bias to be overcome and the shaft is shifted by the amount of axial play in the bearing (approx. 0.1 - 0.2 mm). This shift can cause problems on motors with holding brakes or motors with EnDat encoders. As a result, no axial force is permitted in the direction of the B flange when using these motors.
The shaft ends of motors with holding brakes are not permitted to have axial loads applied. It is especially important to prevent axial forces in the direction of the B flange since these forces can cause the brake to fail!
Determining permissible values for Fr and Fa
Information for determining permissible values of Fr and Fa can be found in the motor data for the respective servo motor. Permissible values are based on a bearing service life of 20,000 h (bearing service life calculation based on DIN ISO 281).