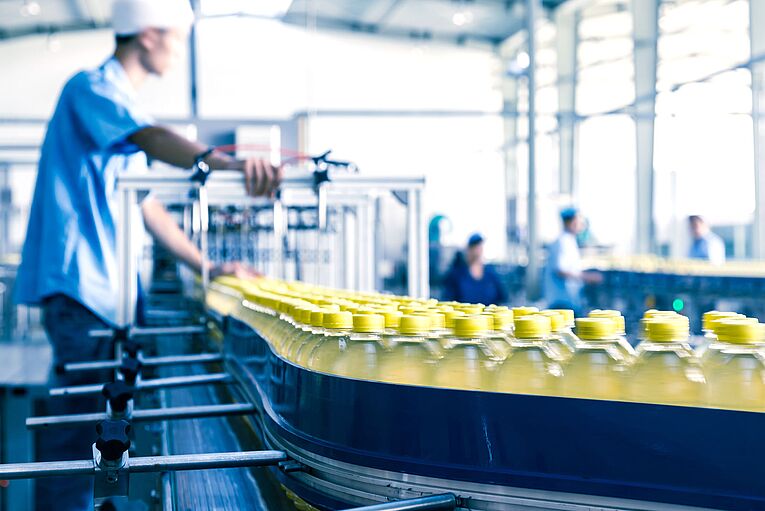
Un système d'automatisation ultra-rapide ne doit pas se payer au prix fort
La technologie reACTION de B&R répartit la charge de traitement pour booster la performance des processus temporellement critiques.
La technologie reACTION de B&R répartit la charge de traitement pour booster la performance des processus temporellement critiques.