„Das Ganze ist mehr als die Summe seiner Teile.“ – Was der griechische Philosoph Aristoteles schon lange vor Industrie 4.0 und Smart Factory erkannte, beschäftigt heute den Maschinenbau. Denn Hardware, Software und ein Programmcode ergeben nicht automatisch eine funktionierende Maschine. Erst das perfekte Zusammenspiel all dieser Komponenten ergibt ein funktionierendes Ganzes. Um das zu erreichen, spielt die Simulation eine entscheidende Rolle.
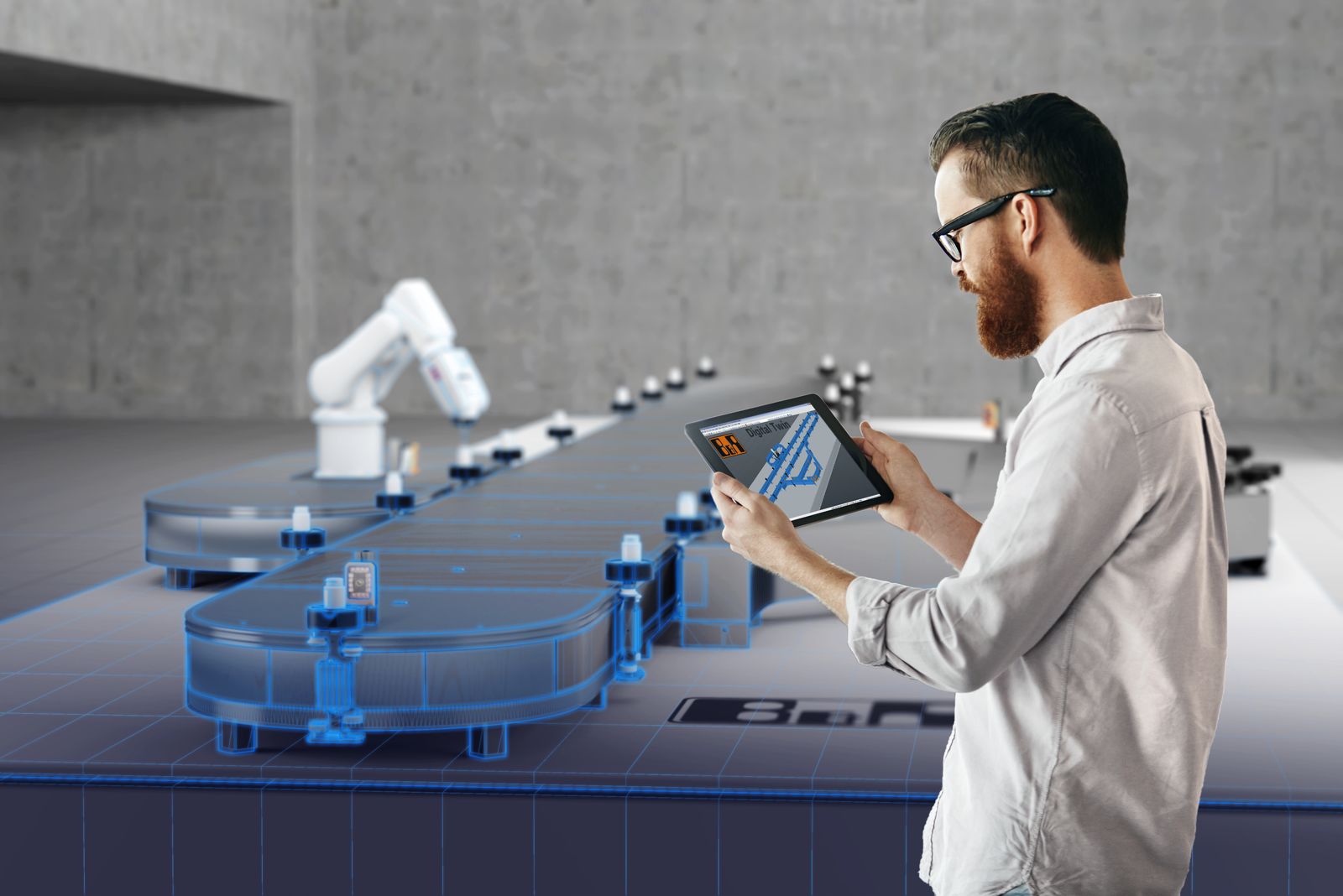
Warum brauchen wir eigentlich Simulation im Maschinen- und Anlagenbau? „Die Antwort ist ganz einfach: Um Maschinen wirtschaftlich zu entwickeln, in Betrieb zu nehmen und langfristig zu betreiben“, sagt Isabella Laasch, Produktmanagerin für Simulation bei B&R.
Maschinen werden immer komplexer. Dementsprechend gestaltet sich auch das Zusammenspiel aus Mechanik, Elektrik und Automatisierung zunehmend diffiziler. Mögliche Maschinenabläufe direkt an einem physischen System auszuprobieren, verursacht hohe Kosten und ist schlichtweg unwirtschaftlich – und zwar in allen drei Phasen des Maschinenlebens: Entwicklung, Inbetriebnahme und laufender Betrieb.
Entwicklungsfehler kosten Geld und Zeit
In der ersten Lebensphase einer Maschine, der Entwicklung, durchläuft die Maschine bereits mehrere Stadien. In jedem davon kann es zu gravierenden Fehlern kommen. Nach der Rule of Ten der Fehlerkosten erhöhen sich die Kosten für die Behebung eines Fehlers um den Faktor 10 für jedes Stadium der Maschinenentwicklung, in dem der Fehler nicht erkannt wurde. Je früher der Fehler also behoben wird, desto günstiger und schneller kann die Maschine entwickelt werden.
Ziehen sich Fehler jedoch durch die gesamte Maschinenentwicklung, zeigen sie sich spätestens bei der Inbetriebnahme des Prototyps. „Taucht bei der Inbetriebnahme ein Problem nach dem anderen auf, ist das fatal“, sagt Laasch. Nicht nur, dass zu diesem Zeitpunkt bereits Kosten für den Prototyp entstanden sind, auch zusätzliche Ressourcen für das Entwicklerteam werden benötigt, da sie sich nun auf Fehlersuche begeben müssen. Entstehen Schäden an der Hardware, bedeutet das zusätzliche Ausgaben für Ersatzteile sowie einen möglichen Zeitverzug aufgrund langer Lieferzeiten. Schlimmstenfalls kommen auf den Maschinenbauer sogar Konventionalstrafen zu, sollte der geplante Auslieferungstermin der neuen Maschine nicht eingehalten werden können.
Simulation ist der Schlüssel
„Wir müssen also einen Weg finden, eine Maschine über alle Lebensphasen hinweg digital abzubilden“, sagt Laasch. „Aus meiner Sicht gibt es dafür nur einen Weg und das ist die Simulation.“ In der virtuellen Simulationsumgebung entsteht ein digitaler Zwilling der Maschine. Mit dem digitalen Zwilling lassen sich das Zusammenspiel der einzelnen Komponenten während der Entwicklung überprüfen sowie eine virtuelle Inbetriebnahme der Maschine durchführen.
![]() | Philipp Wallner Industry Manager bei MathWorks „Mit modellbasierter Entwicklung lässt sich frühzeitig sicherstellen, dass die Maschine funktioniert – das Ausfallrisiko wird auf ein Minimum gesenkt. Simulationsmodelle bilden die Grundlage für Designphase, virtuelle Inbetriebnahme und digitale Zwillinge. Die Investition in die Simulation rentiert sich meist im ersten Jahr.“ |
Hand in Hand mit Simulations-Experten
Maschinenbauer können aus einer Vielzahl an Simulationswerkzeugen auswählen. Das Angebot erstreckt sich von Tools für die Hardware- und Maschinensimulation bis hin zur Prozesssimulation. B&R arbeitet deshalb seit vielen Jahren mit unterschiedlichen Simulationsexperten zusammen und hat verschiedene Werkzeuge in sein Automatisierungssystem eingebunden.
„Mit unseren Partnern wie MathWorks, Maplesoft, machineering und ISG bieten wir eine breite Palette an Simulationsmöglichkeiten und haben für jeden Anwendungsfall eine Lösung parat“, erklärt Laasch. „Entscheidend dabei ist, dass unsere Kunden frei wählen können, welches Simulationswerkzeug sich für ihre Maschine am besten eignet. Die B&R-Entwicklungsumgebung ist in jedem Fall das zentrale Tool.“

Das richtige Werkzeug für jede Anforderung
Mit der Simulationssoftware von Maplesoft und MathWorks lassen sich zum Beispiel Maschinenkomponenten sehr effizient und exakt abbilden sowie Momente und Kräfte etwa für Maschinenauslegungen simulieren. Unterschiedliche Belastungsfälle können einfach getestet werden. Würden diese Tests an einem realen System vorgenommen werden, kosten sie viel Zeit, viele Arbeitsstunden und binden zahlreiche Ressourcen. Im Falle einer zu großen Belastung besteht auch die Gefahr, dass kostbare Hardware beschädigt wird und ersetzt werden muss. In der Simulation erkennt der Maschinenbauer jedoch auf einen Blick, ob die Maschine der Belastung standhalten wird oder nicht.
![]() | Chris Harduwar VP of Business Development, Maplesoft „Wenn Maschinenbauer mit Leistungsproblemen konfrontiert werden, brauchen sie eine schnelle Lösung, die nicht ihre Gewinnmargen auffrisst. Dynamische, physikbasierte digitale Zwillinge ermöglichen Maschinenbauern zu erkennen, wie Probleme bei ihren Designs entstehen und wie sie die Komplikationen – ohne zusätzliche Kosten für Hardware – lösen können." |
Die Tools von machineering und ISG decken hingegen den Bereich der Prozesssimulation ab. Sie zeigen das dynamische Verhalten einer kompletten Maschine in 3D. Damit lassen sich unter anderem sämtliche dynamische Faktoren, die auf den Materialfluss einwirken, mit dem digitalen Zwilling in Echtzeit testen. Der Maschinenbauer sieht sofort, wie sich der Materialfluss verhält, wenn er Komponenten der Maschine austauscht. Auch Stillstandzeiten lassen sich frühzeitig erkennen und eliminieren.
Daten für vorausschauende Wartung nutzen
Nach Abschluss der Maschinenentwicklung und einer erfolgreichen virtuellen sowie realen Inbetriebnahme kann der digitale Zwilling auch in der dritten Lebensphase einer Maschine, dem laufenden Betrieb, von großem Nutzen sein. Basierend auf Echtzeitdaten läuft der digitale Zwilling als virtuelles Pendant im Schaltschrank mit und lässt sich zum Beispiel für Prognosen über die Lebensdauer und den Zustand der realen Maschinenkomponenten heranziehen. „Verändert sich das Verhalten der realen Maschine im Vergleich zum digitalen Zwilling, weil zum Beispiel ein Lager bereits sehr abgenutzt ist, fällt dies unmittelbar auf“, erklärt Laasch. Die gesammelten Daten werden unter anderem für vorausschauende Wartung, Fehlerdokumentationen oder Fernwartungssysteme verwendet.
![]() | Dr. Georg Wünsch Geschäftsführer der machineering GmbH & Co. KG „Unsere Simulationssoftware iPhysics sorgt für Durchgängigkeit im Engineering. Sie vereint alle Disziplinen von MCAD, ECAD sowie Automation bis hin zur Produktion und After Sales. Durch die zusätzliche Anbindung von AR- und VR-Systemen werden komplexe mechatronische Maschinen jederzeit komplett abgesichert.“ |

Einarbeitungszeit verkürzen
Darüber hinaus ergeben sich mit dem digitalen Maschinenpendant zum Beispiel neue Möglichkeiten für das Training von Maschinenbediener und Servicetechniker. Sie können sich unter anderem mit der Handhabung oder dem Human Machine Interface vertraut machen, bevor die Maschine bei ihnen vor Ort eintrifft. Die Einarbeitungszeit verkürzt sich damit wesentlich.
Zudem kommt der digitale Zwilling auch zunehmend in virtuellen Showrooms zum Einsatz. So kann der Vertrieb potenziellen Kunden jederzeit neue Maschinen vorstellen – unabhängig von Messen oder Veranstaltungen. Mit Hilfe einer Augmented-Reality-Brille lässt sich die digitale Maschine sogar in reale Umgebungen einblenden. So sind zusätzliche sogenannte Was-wäre-wenn-Untersuchungen für die Planung und Entwicklung mit bewegten Objekten und Maschinen möglich.
![]() | Dr. Christian Daniel Business Manager Simulation Technology, ISG Industrielle Steuerungstechnik GmbH „Konfiguriert man Simulationsszenarien als digitale Zwillinge mit virtuellen wiederverwendbaren Komponenten aus einer Bibliothek, dann können sie auch vom Betreiber der Anlagen für Produktionsoptimierungen, Umrüstungen und als Basis für innovative Schulungs- und Servicekonzepte genutzt werden.“ |
Maschinen schneller weiterentwickeln
„Der digitale Zwilling bleibt der Maschine ein Leben lang erhalten“, sagt Laasch. „Er bildet aber auch die Basis für zusätzliche Funktionen und für die Weiterentwicklung der Maschine.“ Der Maschinenbauer kann zum Beispiel die Erkenntnisse aus dem laufenden Betrieb für die Optimierung des Systems verwenden. Das Simulationsmodell steht ihm dabei zur Verfügung, um alle geplanten Erweiterungen vorab sicher durchzuspielen. So reduzieren sich Stillstandzeiten bei Aufrüstungen auf ein Minimum und die nächste Generation an Maschinen lässt sich schneller entwickeln.
Autor: Carola Schwankner, Unternehmensredakteurin bei B&R
Isabella Laasch
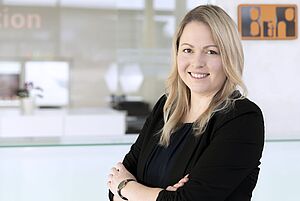
„Mit unseren Partnern wie MathWorks, Maplesoft, machineering und ISG bieten wir eine breite Palette an Simulationsmöglichkeiten und haben für jeden Anwendungsfall eine Lösung parat. Unsere Kunden können frei wählen, welches Simulationswerkzeug sich für ihre Maschine am besten eignet. Die B&R-Entwicklungsumgebung ist in jedem Fall das zentrale Tool.“