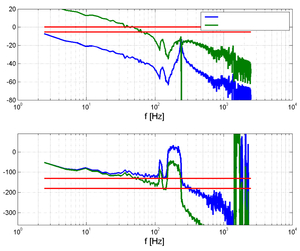
With the help of the auto-tuning function for drive axes, it is possible to automatically and optimally configure the drive controller for the ACOPOSmulti drive system (this includes the position controller and the underlying speed controller). The control parameters are detected while the machine is practically at a standstill. Parameters to compensate for the effects of inertia and friction are also determined.
Procedure
Before the actual auto-tuning process, a safe operation area is specified where the drive can move during automatic controller configuration. Then the fully automatic controller configuration is started with a mouse click. Within a short time, the autotuning function determines the optimal controller configuration for the mechanical system that is connected. The parameters for reference variable implementation are then calculated using a defined drive movement. This includes, for example, inertia as well as speed-proportional and static friction.
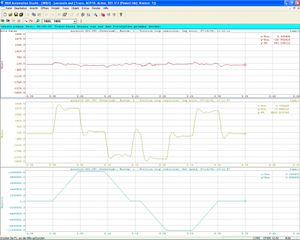
The biggest advantages of the auto-tuning function are that Automation Studio beginners are provided support when commissioning axes and people without a lot of technical knowledge concerning drives can quickly achieve good results because of the simple operation. Advanced users can work in expert mode, which allows custom tuning of individual control loops.
In this way, it is possible for beginners and experts to achieve more dynamic operation of a drive. Extensive testing in the field has shown that this procedure is very robust when using different mechanics and encoder systems and provides very good lag error characteristics. In most cases, manually adjusting the control parameters afterwards is not necessary.
A variety of application possibilities
The advantage of being independent of the encoder system results in a wide spectrum of application possibilities. Typical areas of use include highly dynamic direct drive torque motors or geared power transmission systems, drives with synchronous or induction motors and linear drives. The auto-tuning function can also be used on machines with a limited range of movement or with limitations regarding movement direction after it has been configured accordingly. Additionally, decreased dynamics caused by mechanical resonances on two-mass systems can be reduced using passive damping.