Un hombre con una pala trabajaría durante semanas para mover lo que el cucharón de alta capacidad de una excavadora minera puede transportar en una sola carga. Sin embargo, cuanta más tierra mueven estas máquinas enormes con cada palada, con más rapidez cada segundo de mantenimiento no programado afecta al resultado final, razón por la cual las compañías mineras invierten tanto para mantener a sus gigantes en buenas condiciones. El coste para lograr esta fiabilidad fundamental se puede reducir considerablemente a través de un mantenimiento inteligente.
Alejados de la civilización más cercana, elevándose por encima de sus amos humanos, estos monstruos gigantes dan enormes mordiscos al paisaje rocoso. La excavadora minera más grande del mundo tiene 24 metros de largo, 8,8 metros de ancho, 11 metros de alto y pesa 800 toneladas. Sentado cómodamente en la cabina a unos vertiginosos 10 metros del suelo, el conductor maneja los joysticks que controlan una enorme pala con una capacidad de 47 metros cúbicos. En tan solo 20 segundos, la colosal máquina mueve 80 toneladas de material. "Cuando una excavadora tan grande se avería, la compañía no solo sufre costosas pérdidas de productividad, sino que las consecuencias pueden afectar a toda la cadena logística", explica Stefan Taxer, director de productos de B&R para la automatización móvil.
Por lo tanto, prevenir los períodos de inactividad inesperados es una prioridad. Con este fin, los componentes rotativos, como las bombas hidráulicas, los motores y los reductores tienen normalmente un diseño sobredimensionado y se sustituyen a unos intervalos conservadoramente cortos. Para que cualquier período de inactividad sea lo más breve posible, las compañías mineras mantienen un stock considerable de piezas de repuesto a mano. "Lo que todas estas soluciones tienen en común es que implican unos costes adicionales", señala Taxer. Estos costes pueden reducirse aplicando enfoques modernos de análisis y mantenimiento.
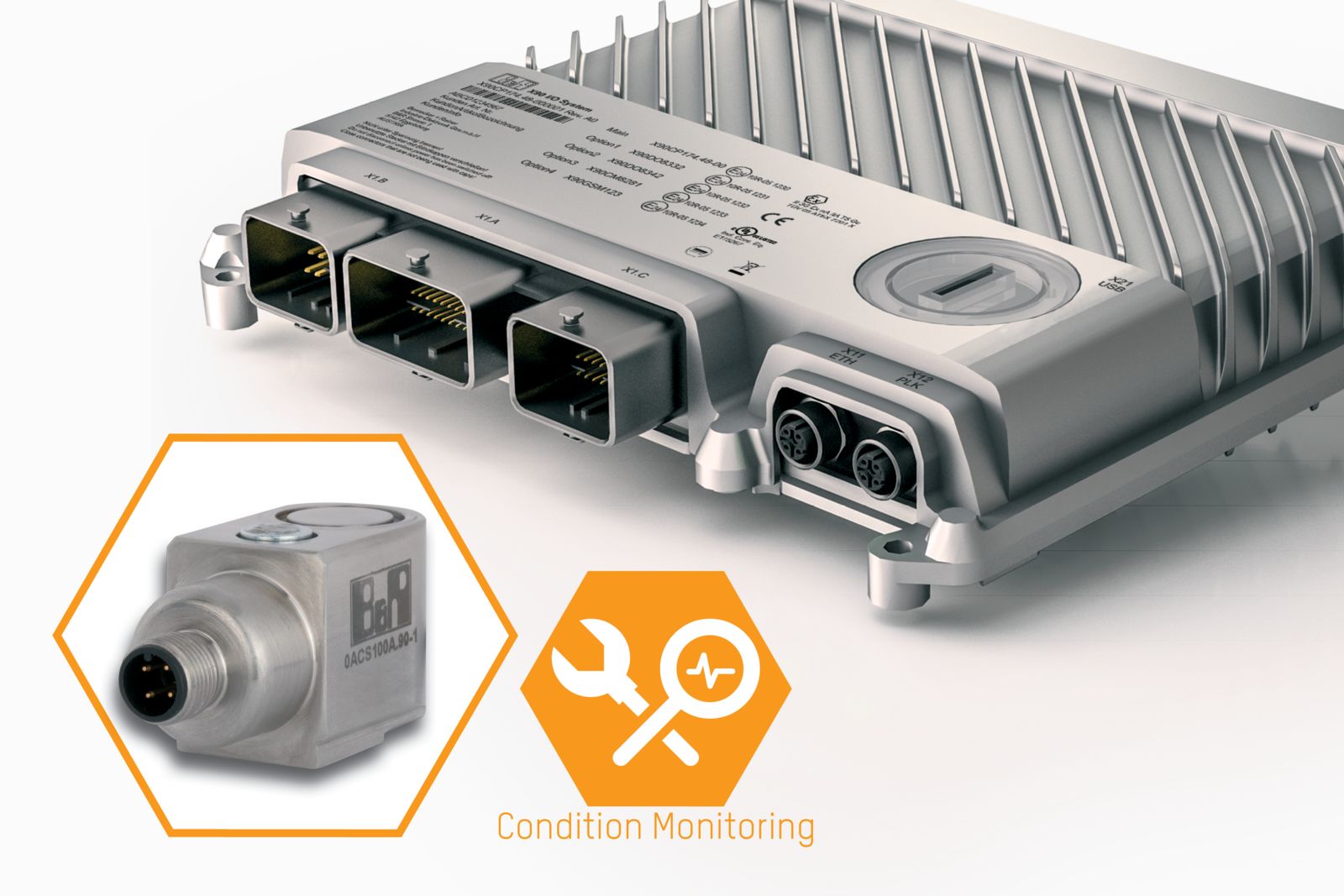
Fallos de pronóstico
Puesto que el paso del tiempo afecta a los componentes rotativos de la máquina, a menudo incluso un oído no entrenado puede detectar la diferencia. "Es relativamente fácil saber cuándo tu automóvil tiene un rodamiento de la rueda defectuoso debido al ruido distinto que genera", nos cuenta Taxer. Sin embargo, las excavadoras mineras son tan ruidosas que es imposible distinguir cualquier cambio audible. "Aquí es donde resulta útil la monitorización del estado basado en las vibraciones".
Después de todo, el ruido audible no es más que vibraciones a cierta frecuencia. Un sistema de monitorización del estado configurado correctamente reconocerá un pico en la amplitud de la vibración en un rango de frecuencia específico como señal de un fallo inminente. La altura del pico denota la gravedad del daño, indicando con qué urgencia debe sustituirse una parte determinada.
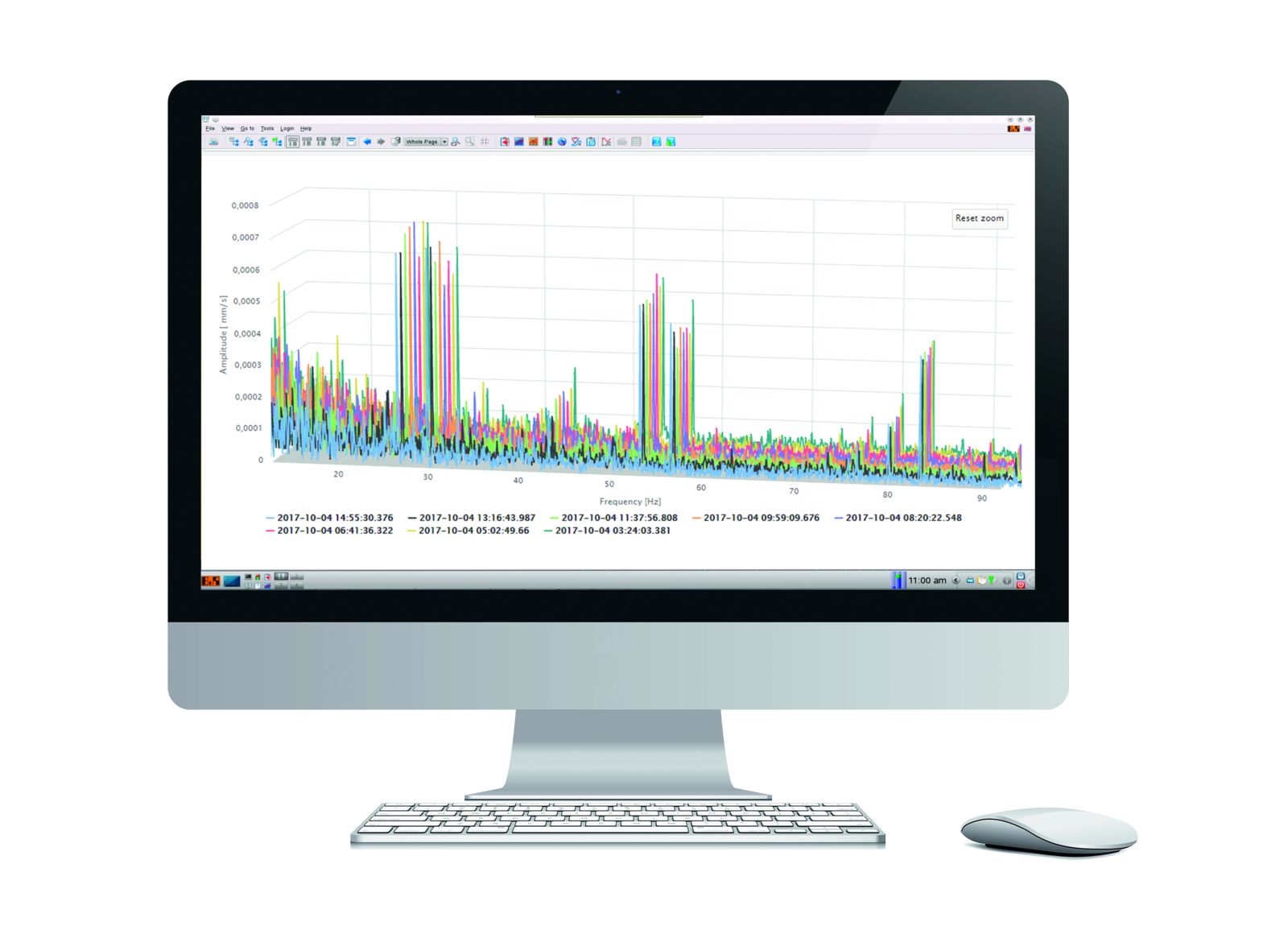
Aprovechamiento de los datos de las vibraciones
"La evaluación de los datos de las vibraciones depende de dos elementos fundamentales", señala Taxer. Por un lado, se necesita un hardware de alto rendimiento que pueda leer los datos a una frecuencia suficientemente alta. Por otro lado, se necesita un software inteligente capaz de detectar las desviaciones más pequeñas en un gran volumen de datos.
"Nuestro control modular X90 y el sistema de E/S ofrece la plataforma de hardware perfecta", comenta Taxer. El núcleo del sistema es el control X90, con un potente procesador ARM y hasta 48 canales multifuncionales de E/S. El control modular puede equiparse con E/S opcionales, interfaces o circuitos integrados, como el que se utiliza para la monitorización del estado.
"Unido a nuestros componentes de software mapp, el resultado es un sistema de muy alto rendimiento que monitoriza el estado de la máquina e informa a los operarios a tiempo para tomar las medidas oportunas", afirma Taxer. "Los componentes mapp se configuran rápidamente y se comunican entre sí automáticamente, reduciendo al mínimo la cantidad de programación real".
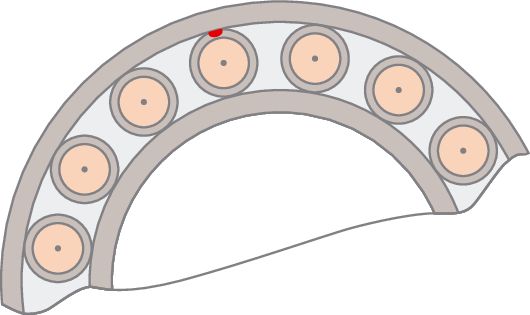
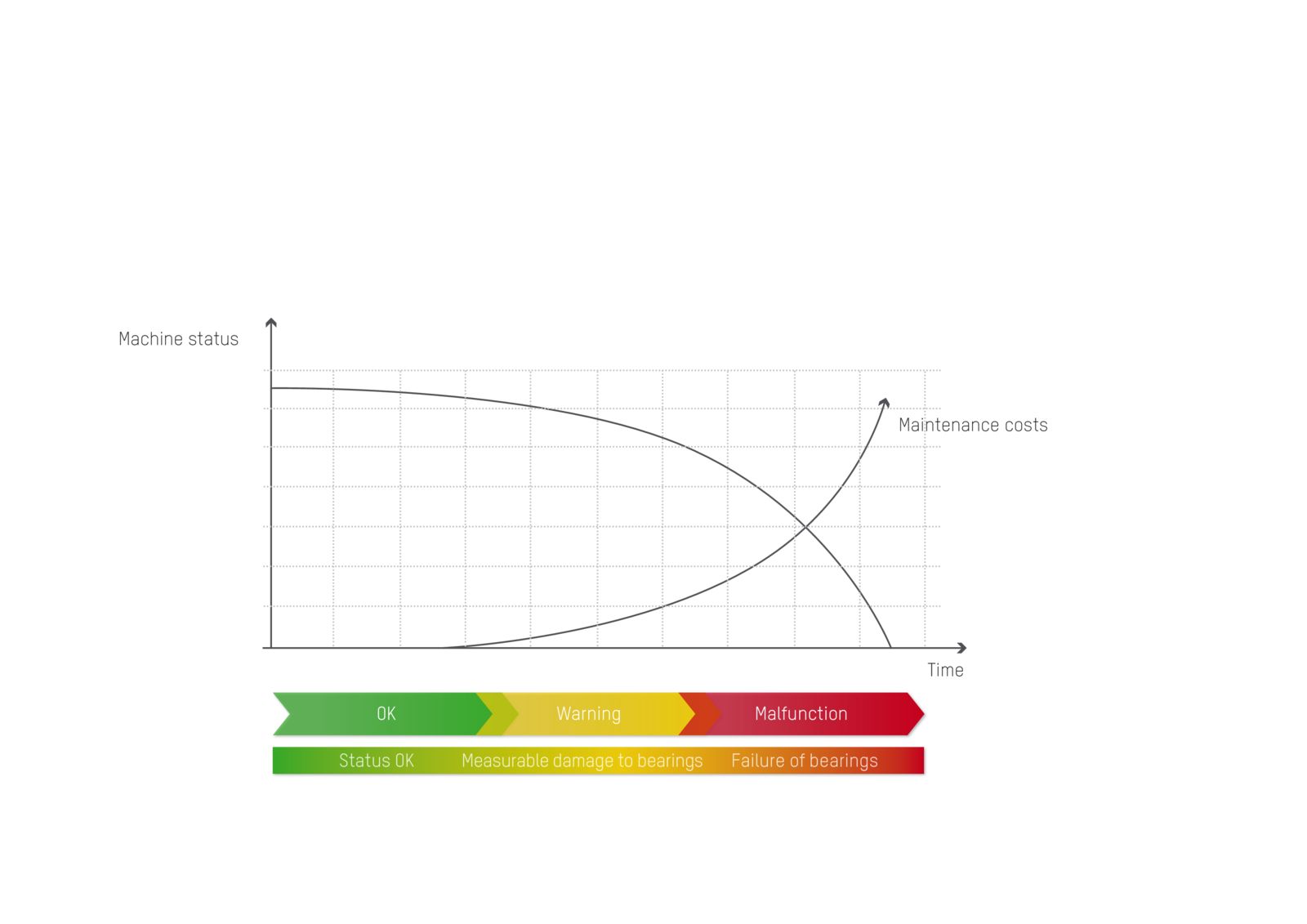
Tiene un correo electrónico... de su máquina
Un ejemplo de cómo se comunican los componentes mapp es la interacción entre los sistemas de alarma y notificación utilizando mapp Alarm y mapp Tweet. "Estos componentes pueden vincularse fácilmente para que, cada vez que salte una alarma, el técnico de mantenimiento reciba un correo electrónico o un mensaje de texto", explica Taxer. Este mensaje puede informar al técnico de que cierto rodamiento está desgastado y que debe sustituirse en un período de tiempo determinado.
"Tan fácil como configurar el sistema de alarmas, la parte más emocionante es la influencia que puede tener en la estrategia general de mantenimiento", reflexiona Taxer, refiriéndose al enorme potencial de ahorro. El mantenimiento basado en el estado agiliza la logística de repuestos y elimina la necesidad de sustituir componentes en perfecto estado mucho antes del final de su vida útil.
Incluso pueden compartirse ciertos datos de monitorización del estado con el fabricante de la máquina. "Si un fabricante puede realizar un seguimiento del estado de sus máquinas, puede reducir drásticamente la probabilidad de fallos", observa Taxer. Esto, por supuesto, también es ideal para el operario.
Los fabricantes de equipos móviles también pueden utilizar ciertos datos para optimizar sus diseños y buscar nuevos modelos de negocio, como ofrecer un servicio de monitorización de equipos. En este caso, el operario se libera de los quebraderos de cabeza que representa el mantenimiento de la flota y simplemente se le informa de cuándo se entregará e instalará una pieza de recambio.

Stefan Taxer, Director de Producto - Automatización Móvil, B&R
Todo el mundo sale ganando
Y ello hace que Taxer señale aún otra ventaja: "Ya no es necesario diseñar tantos componentes sobredimensionados". Un hecho que, una vez más, beneficia a ambos lados: el fabricante se ahorra costes de producción y el operario paga menos por la máquina. Dado que el control X90 puede conectarse a arquitecturas CAN ya existentes, es fácil incluir sistemas de monitorización del estado a una flota operativa. "Se puede avanzar paso a paso hacia un sistema de bus moderno en tiempo real que permita gestionar el volumen de datos que generan las máquinas actuales".
Las estrategias convencionales para evitar fallos inesperados de las excavadoras mineras son costosas y requieren muchos recursos. Con el sistema X90 de B&R y la tecnología de monitorización del estado, tanto los fabricantes como los operarios de equipos móviles pueden generar un valor añadido con soluciones que consiguen que sus gigantes de acero sean más fiables.
Autor: Carmen Klingler-Deiseroth, periodista independiente
Experiencia aplicada
B&R tiene casi 40 años de experiencia creando soluciones de automatización e impulsando innovaciones en una amplia variedad de sectores y ha implementado con éxito protocolos de Ethernet industrial de alto rendimiento como POWERLINK en muchos sectores diferentes. Los equipos móviles actuales pueden aprovechar esta valiosa experiencia para resolver algunos de sus problemas más críticos. Para los fabricantes de maquinaria móvil, el sistema de control móvil X90 es una inversión preparada para el futuro que se centra en la fiabilidad y rentabilidad de sus equipos.